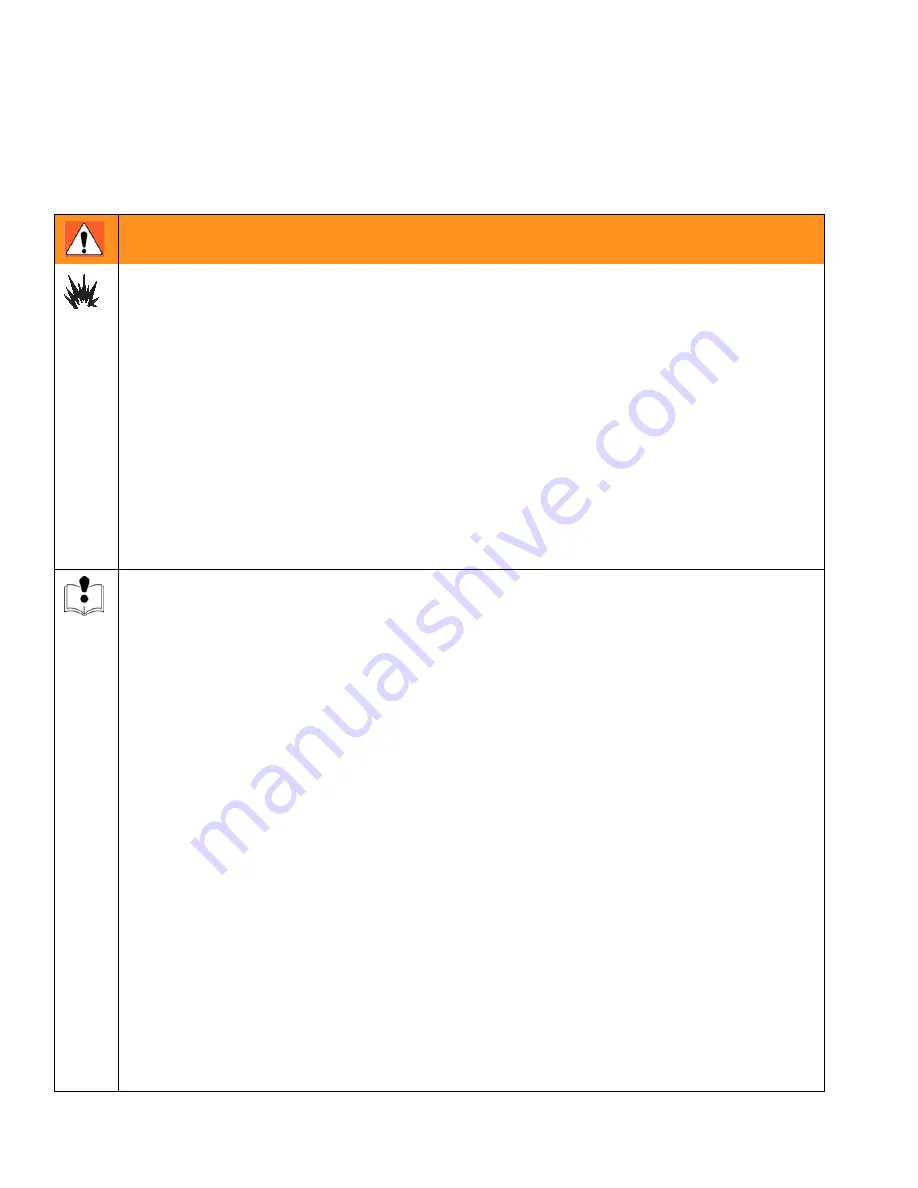
Warnings
2
311772G
Warnings
The following are general warnings related to the setup, use, grounding, maintenance and repair of this equipment.
Additional, more specific warnings may be found throughout the body of this manual where applicable. Symbols
appearing in the body of the manual refer to these general warnings. When these symbols appear through the
manual, refer back to these pages for a description of the specific hazard.
Warnings
Fire and Explosion Hazard
Improper grounding, poor ventilation, open flames or sparks can cause a hazardous condition and result
in fire or explosion and serious injury.
• The system is for use with water-based materials only. Only use fluids compatible with the
equipment. Refer to Technical Data of all equipment manuals. Read fluid and solvent manufacturers
warnings.
• Ground all equipment in the work area. See
Grounding and Electrical Requirements
, page 6.
• If there is any static sparking or you feel an electric shock while using this equipment, stop spraying
immediately. Do not use the equipment until you identify and correct the problem.
• Keep work area free of debris, including solvent, rags and gasoline.
• Comply with all applicable state and national fire, electrical and safety regulations.
• Keep a fire extinguisher in the work area.
Equipment Misuse Hazard
Equipment misuse can cause equipment to rupture, malfunction, or start unexpectedly and cause serious
injury.
• Before operating this equipment, read all manuals, tags, and labels, including material labels and
instructions.
• Do not expose system to rain. Always store system indoors.
• Do not alter or modify equipment.
• Do not spray cementitious materials.
• Do not exceed maximum working pressure of lowest rated component in your system.
• Check equipment daily. Repair or replace worn or damaged parts immediately.
• To reduce risk of serious injury, including electric shock and splashing fluid in eyes, follow
Pressure
Relief Procedure
on page 6 before servicing the unit.
• Do not kink or over bend hoses or use hoses to pull equipment.
• Route hoses away from traffic areas, sharp edges, moving parts and hot surfaces. Do not expose
Graco hoses to temperatures above 130° F (55° C) or below -35° F (-37° C).
• Air hoses at the compressor end, can get very hot! Allow sprayer to cool down 15 minutes before
removing air hose.
• Store hazardous fluid in an approved container. Dispose of hazardous fluid according to all local,
state and national guidelines.
• Never directly inhale compressed air. Compressed air may contain toxic vapors.