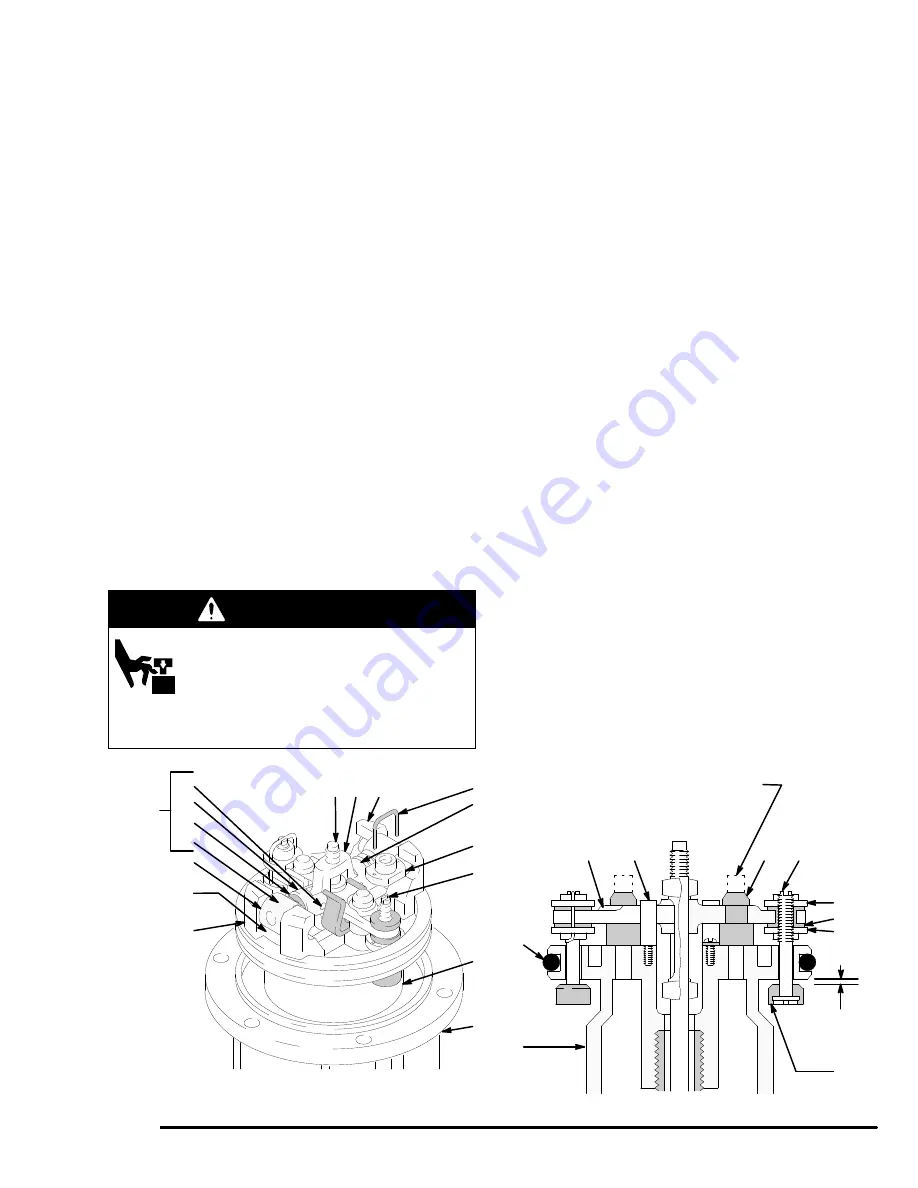
9
307-043
Air Motor Service
7.
Pull the piston assembly (G) from the air motor
base (F), and set it aside.
8.
Remove the bearing housing assembly (26 or 27)
for all Models except Model 206–955. Remove and
wipe the seat clean with a cloth. For model
206–955, remove retainer ring (3) and bearing (4).
Remove seal (2, 27 or 28).
9.
Remove the base from the vise, and set it upright
on the workbench.
10. Place the piston rod flats in a vise.
11. Use a screwdriver to push down on the trip rod
yoke (O), and snap the toggles down. See Fig. 3.
WARNING
MOVING PARTS HAZARD
To reduce the risk of pinching or ampu-
tating your fingers, keep your fingers
clear of the toggle assemblies when you
are snapping the toggles (U in Fig. 3 ) up
or down.
12.
In this step, while you are prying with the screw
-
driver with one hand, cover the toggle assemblies
with your other hand so as to catch the spring-
loaded toggle assemblies when they snap out of
the lugs. Place the tip of a screwdriver into the
piston between the piston lugs (P) below the pivot
pins (Q) on the toggles, pry up with the screw-
driver handle to compress the springs on the
toggle assembly (U) up and away from the piston
lugs, and remove the parts. See Fig. 3.
13. Straighten the lockwires (L**) and remove them
from the upper valve nuts (J**). Screw the upper
valve nuts off. Remove the trip rod yoke (O),
actuator (V), and trip rod (C).
14. Unscrew the bottom valve nuts (K**), and remove
the poppets (N**). Make sure the valve bar spring
clips (W) are not worn or damaged and that they
properly guide the actuator (V).
15. Remove the exhaust valve poppets (M) by cutting
them with a side cutter, then pull them out of the
actuator (V).
16. Remove piston o-ring (Z) and internal base o-ring
(15** or 19**). Inspect o-rings.
17. Clean all the parts carefully in a compatible solvent
and inspect them for wear or damage. Use all the
repair kit parts during reassembly, and replace
other parts as necessary.
18. Check the surfaces of the piston, piston rod, and
cylinder wall for scratches or wear. A scored rod
will cause premature packing wear and leaking.
Fig. 3
04118
C O U
L
J
X
G
F
T
T
04119
W
V
G
M
X
J
K
N
0.145 in.
(3.7 mm)
P
Q
S
R
Z
U
Y
Cutaway View
Cut off the tops of the poppets
as indicated by the dotted lines
Z
Insert Screw
Driver Here