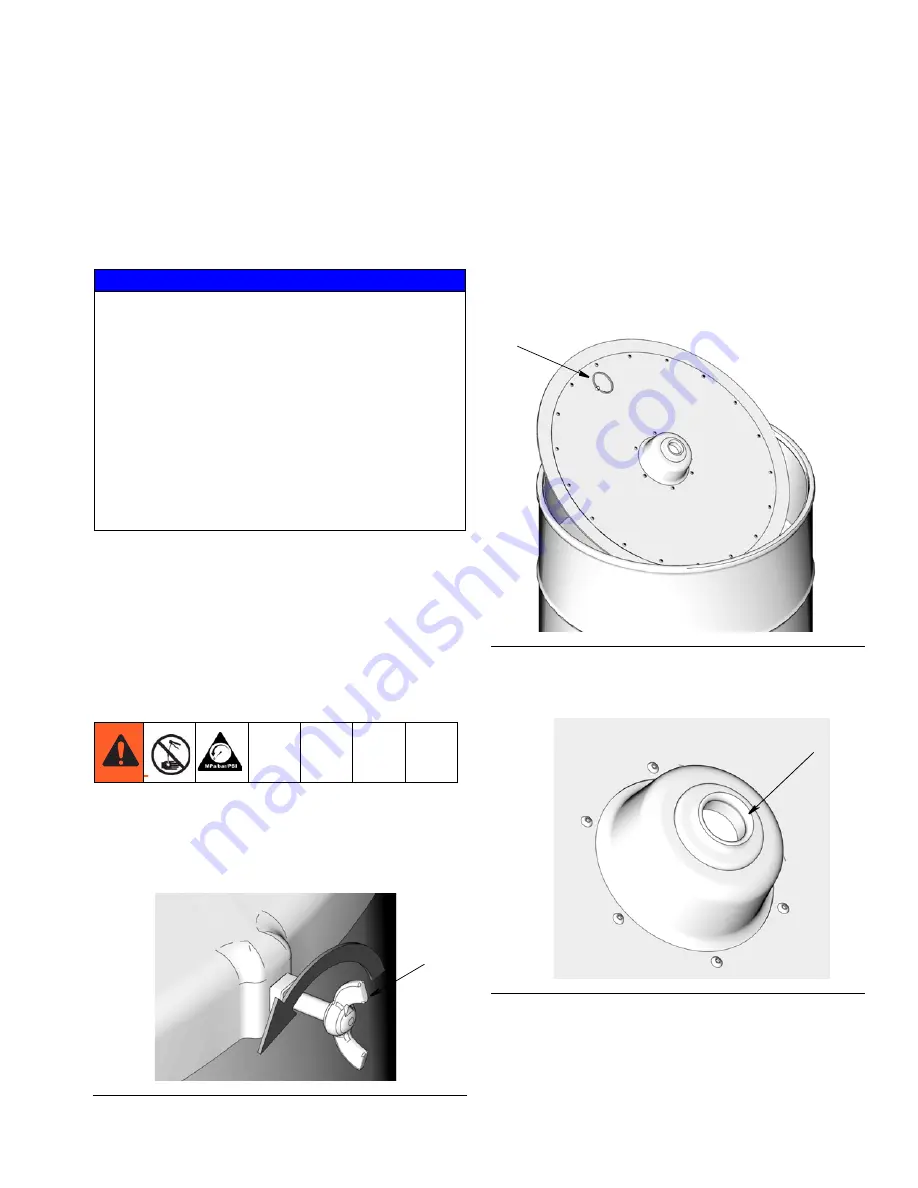
Operation
3A1334P
11
Step 6 is for Oil Pumps Only:
6.
The thermal relief feature of this oil pump can
increase the amount of time needed to fully prime
the pump when compared to pumps without a ther-
mal relief feature. To minimize this effect, prime the
pump
before
connecting it to an already primed dis-
tribution system.
7.
Read and follow the instructions supplied with each
component in your system.
8.
When shutting off the system and before checking
or servicing, relieve pressure following pressure
relief procedure, page 9.
Changing Grease Drum and Installing
Follow Plate (grease models only)
1.
Relieve pressure
, page 9.
2.
Remove drum cover by loosening thumb screws (a)
(F
IG
. 5).
3.
Remove pump and cover from drum and place on a
clean paper, cardboard, or clean shop rags. DO
NOT PLACE ON SHOP FLOOR.
4.
If this is an existing installation, reach into drum and
pull on follow plate ring (b) to remove follow plate
(F
IG
. 6). Place follow plate on a clean paper, card-
board or clean shop rags. DO NOT PLACE ON
SHOP FLOOR.
Remove drum and install new one.
5.
Examine follow plate to make sure rubber grommet
(c) is in place in center of the plate (F
IG
. 7).
6.
Set follow plate on top of fresh grease (F
IG
. 8).
Remove air by pushing on the follow plate until the
NOTICE
Never allow the pump to run dry of the fluid being
pumped. A dry pump will quickly accelerate to a high
speed, possibly damaging itself. If your pump acceler-
ates quickly, or is running too fast, stop it immediately
and check the fluid supply. If the supply container is
empty and air has been pumped into the lines, prime
the pump and lines with fluid, or flush it and leave it
filled with a compatible solvent. Be sure to eliminate
all air from the fluid system.
NOTE:
A pump runaway valve can be installed on the
air line to automatically shut off the pump if it starts to
run too fast.
F
IG
. 5
a
F
IG
. 6
F
IG
. 7
b
c
Summary of Contents for LD Series
Page 13: ...Notes 3A1334P 13 Notes ...
Page 31: ...Notes 3A1334P 31 Notes ...