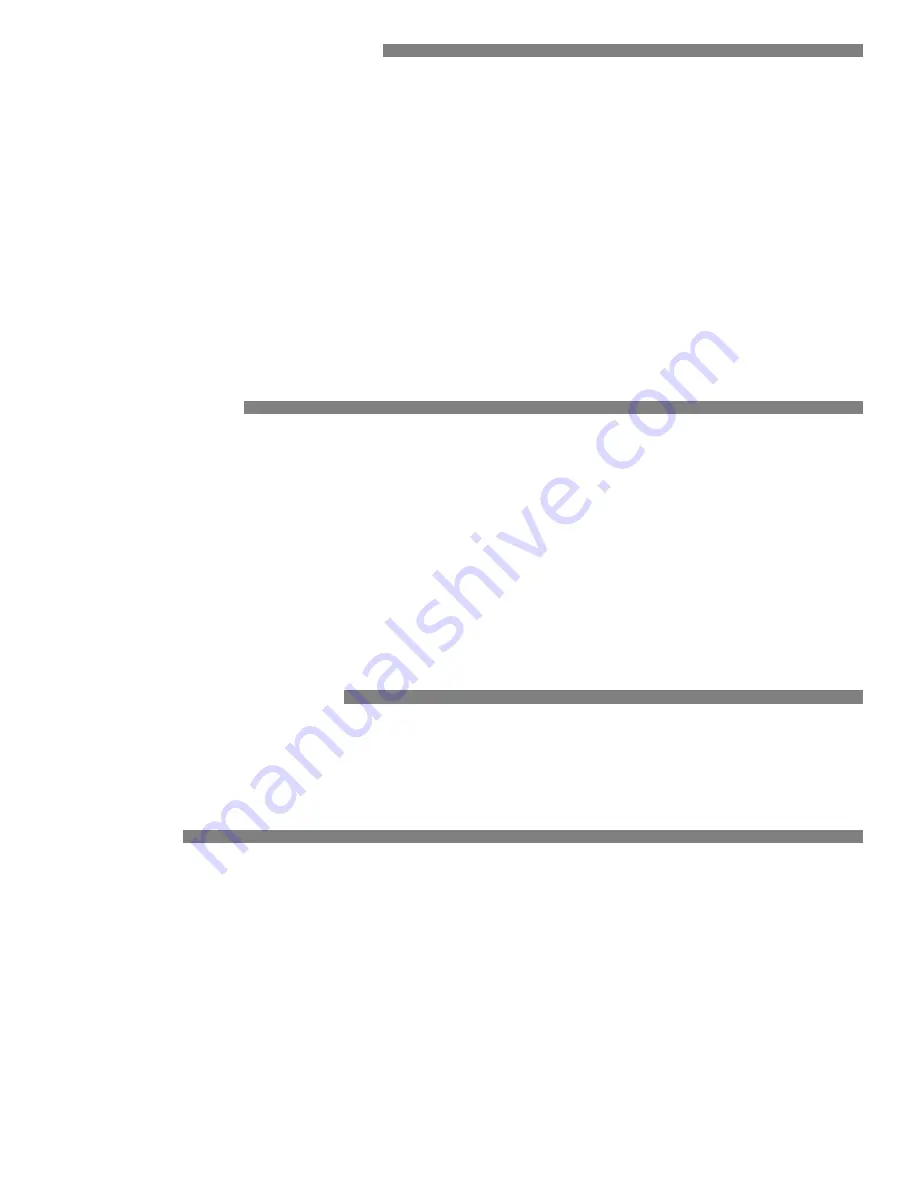
308–507
3
EQUIPMENT MISUSE HAZARD
General Safety
Any misuse of the pressure washer or accessories, such
as overpressurizing, modifying parts, using incompatible
chemicals and fluids, or using worn or damaged parts,
can cause them to rupture and result in fluid injection,
splashing in the eyes or on the skin, or other serious
bodily injury, fire, explosion or property damage.
NEVER alter or modify any part of this equipment; doing
so could cause it to malfunction.
CHECK all spray equipment regularly and repair or
replace worn or damaged parts immediately.
ALWAYS wear protective eyewear and appropriate
clothing. If using a chemical injector, read and follow the
chemical manufacturer’s literature for recommendations
on additional protective equipment, such as a respirator.
System Pressure
This sprayer can develop high operating pressures. Be
sure that all spray equipment and accessories are rated
to withstand the maximum working pressure of
this
sprayer.
DO NOT exceed the maximum working
pressure of any component or accessory used in the
system.
Chemical Compatibility
BE SURE that all chemicals used in the chemical injector
are compatible with the wetted parts of the hose, gun,
wand and tip, as given in the Technical Data (inside back
cover). Always read the chemical manufacturer
’s
literature before using any chemical in this pressure
washer.
HOSE SAFETY
High pressure fluid in the hoses can be very dangerous. If
the hose develops a leak, split or rupture due to any kind
of wear , damage or misuse, the high pressure spray
emitted from it can cause a fluid injection injury or other
serious bodily injury or property damage.
ALL FLUID HOSES MUST HA VE STRAIN RELIEFS
ON BOTH ENDS.
The strain reliefs help protect the hose
from kinks or bends at or close to the coupling, which can
result in hose rupture.
TIGHTEN all fluid connections securely before each use.
High pressure fluid can dislodge a loose coupling or allow
high pressure spray to be emitted from the coupling.
NEVER use a damaged hose. Before each use, check
entire hose for cuts, leaks, abrasion, bulging cover , or
damage or movement of the hose couplings. If any of
these conditions exist, replace the hose immediately.
DO
NOT try to recouple high pressure hose or mend it with
tape or any other device. A repaired hose cannot contain
the high pressure fluid.
HANDLE AND ROUTE HOSES CAREFULL Y.
Do not
pull on hoses to move the pressure washer. Do not use
chemicals which are not compatible with the inner tube
and cover of the hose.
DO NOT expose Graco hose to
temperatures above 200
F (93
C) or below –40
F
(–40
C).
MOVING PARTS HAZARD
Moving parts can pinch or amputate fingers or other body
parts.
KEEP CLEAR of moving parts when starting or
operating the pressure washer.
NEVER operate the pressure washer without all guards
and interlocks installed and functioning. Follow the
Pressure Relief Procedure
before checking or
servicing the pressure washer to prevent discharging
high pressure fluid from the gun.
TERMS
WARNING:
Alerts user to avoid or correct conditions
that could cause bodily injury.
NOTE:
Identifies helpful procedures and information.
CAUTION:
Alerts user to avoid or correct conditions that
could cause damage to or destruction of equipment.
IMPORTANT
United States Government safety standards have been adopted under the Occupational Safety and Health Act. These
standards—particularly the General Standards, Part 1910, and the Construction Standards, Part 1926—should be
consulted.