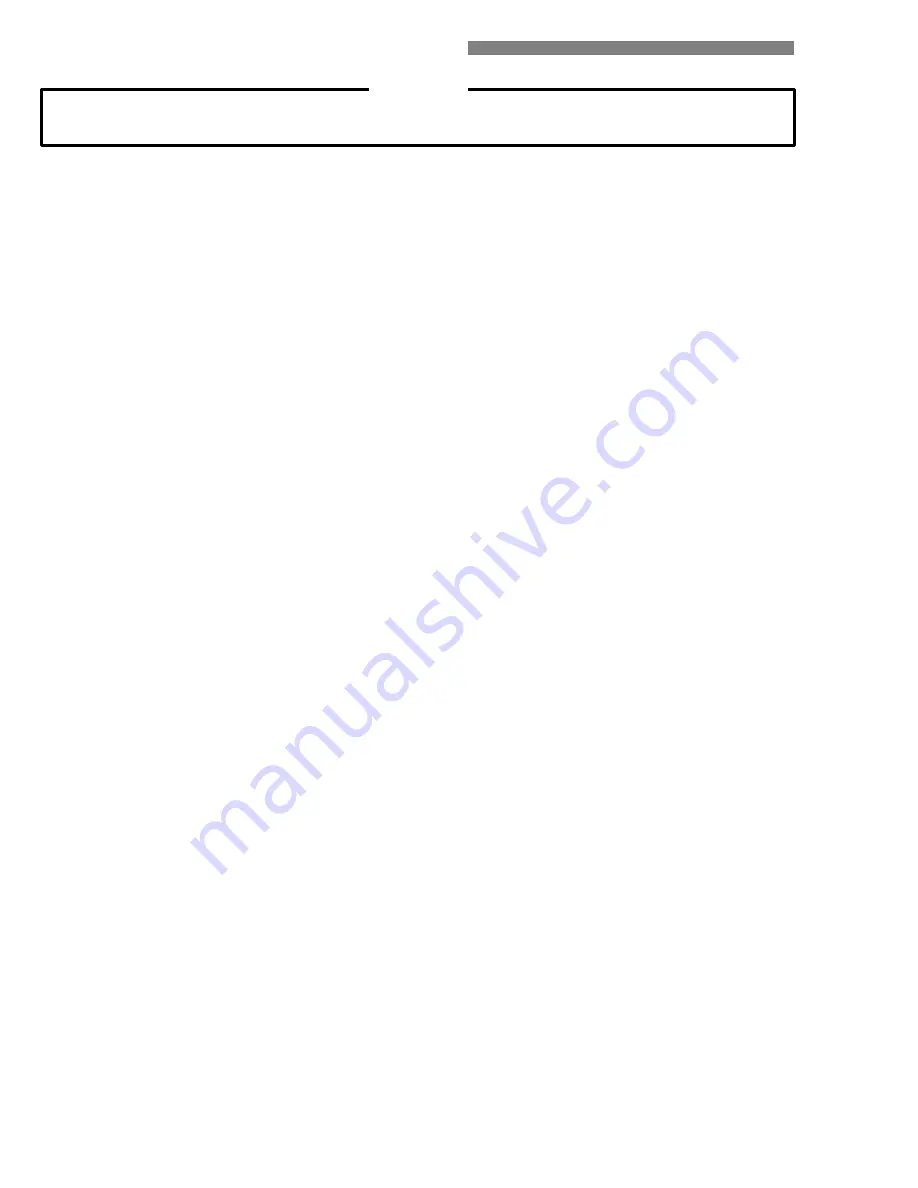
18
308–530
GEAR REDUCER SERVICE (Models 2040 & 2540)
WARNING
To reduce the risk of serious bodily injury, including fluid injection, splashing in the eyes or on the skin or injury from
moving parts, always follow the
Pressure Relief Procedure Warning
on page 2 before proceeding.
Replacing the Gasket (9)
NOTE: To maintain a good seal, the gasket must be
replaced whenever the gear reducer is
disassembled.
1. Remove the four bolts, lockwashers and washers.
Pull the pump and gear reducer assembly of f the
engine.
2. Drain the gear reducer oil by placing a container
under it and removing the drain plug with a 22 mm
wrench. Replace the o–ring (15) if damaged.
3. Remove the nine screws with a 6 mm wrench and
pull the gear case off the gear cover.
4. Remove the old gasket (9). Clean the gear cover and
case surface. Lightly coat the new gasket with
grease and install it in on the gear case.
5. Follow steps 5 through 7 under Assembling the Gear
Reducer if this is all the service required.
Replacing the Oil Seals (21)
1. Follow steps 1 through 3 under Replacing the
Gasket.
2. Loosen the setscrew, using a 4 mm wrench, and pull
the gear (4) off the pump with a gear puller.
3. Using a 6 mm wrench, remove the four screws. Keep
them separate from the other nine screws removed
previously.
4. Remove the four oil seals (21) and replace them.
5. Follow steps 2 through 7 under Assembling the Gear
Reducer if this is all the service required.
Replacing the O–Ring (1)
1. Follow the instructions under Replacing the Gasket
and Replacing the Oil Seals to disassemble the gear
reducer.
2. Pull the gear cover of f the pump and replace the
o–ring (1).
3. Follow instructions under Assembling the Gear
Reducer if this is all the service required.
Replacing the Oil Seal (14)
NOTE:
The oil seal MUST be replaced if removed.
1. Follow steps 1 and 3 under Replacing the Gasket.
2. Remove the snap ring (6) from the gear case, using a
snap ring pliers. Pull the gear and bearing.
3. Push the seal from the inside to the outside of the
gear case by placing screwdriver against the seal
and lightly tapping it with hammer.
4. Wipe the inner surface of the case clean, then lightly
coat it with grease. Place the oil seal into the gear
case. Use a socket, placed against the surface of the
seal, to push the seal into the case until its top
surface is past the ridge in the bore.
5. Place the gear and bearing back into the gear case
and install the snap ring (6).
6. Follow steps 4 through 7 under Assembling the Gear
Reducer if this is all the service required.
Assembling the Gear Reducer
1. Grease the o–ring and make sure it’s properly placed
on the gear cover.
2. Place the four oil seals and screws in the gear cover.
Place the o–ring on the screw to hold it in the cover.
3. Apply low strength Loctite
(blue) on the screw
threads, align the screws with the holes in the pump,
and tighten the screws oppositely and evenly.
4. Grease the pump shaft. Align the gear’s slot with the
key on the pump shaft and slide the gear onto the
shaft, up to the pump’s shoulder. Apply low strength
Loctite
on the setscrew threads and tighten the
setscrew to lock the gear on the shaft.
5. Make sure the gasket is in place (refer to step 4 under
Replacing the Gasket). Install the gear cover on the
case, aligning the holes, and secure it with the nine
screws and lockwashers. Tighten the screws evenly
in a crisscross pattern.
6. Grease the engine shaft. Align the gear’s slot with the
key on the engine shaft and slide the gear reducer
onto the shaft, up to the engine’s shoulder.
7. Secure the gear reducer to the engine with the four
bolts, lockwashers and washers.