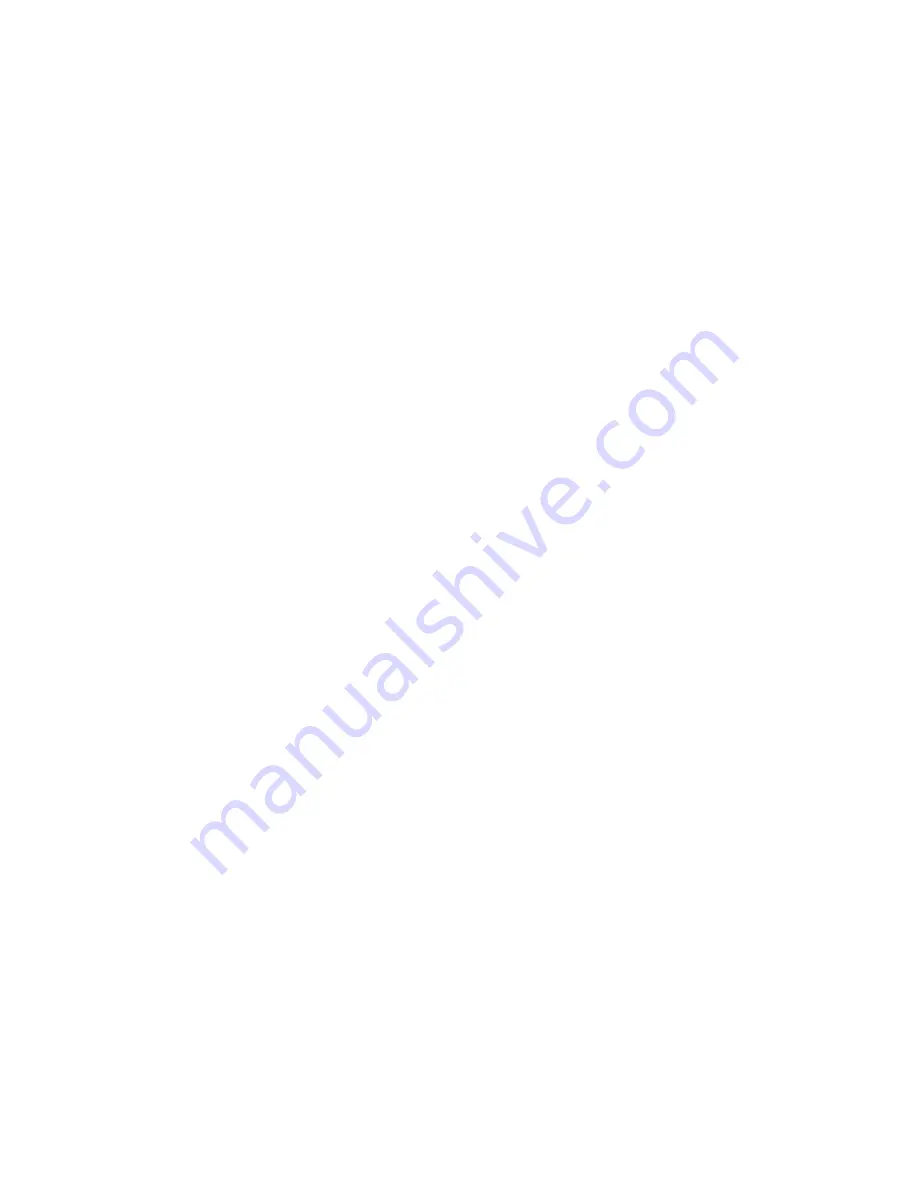
bleed-type master air valve, and turn the air
regulator knob clockwise until the pump starts.
4.
Allow the pump to cycle slowly until all the air is
pushed out of the lines. Release the trigger. The
pump will stall against the pressure.
5.
The manifold handle controls fluid flow. With the
lever of the manifold in the open (down) position,
base and catalyst are supplied to the gun. To
stop the flow, move the handle to the closed (up)
position.
Standard
Standard
Standard Operation
Operation
Operation
Flushing
Flushing
Flushing
Use the solvent valves to flush contaminants and
mixed fluids from the mixer manifold, hose and spray
gun. Follow the procedure provided with the mix
manifold assembly
Check
Check
Check The
The
The Ratio
Ratio
Ratio
The mix ratio must be checked at the normal
operating fluid pressure of the pump. Most mixer
manifolds provide a means for checking mix ratio
that includes needle valves for adjusting the fluid
pressure during the test. The following procedure is
an example of how to properly check the mix ratio.
1.
Open the mixer manifold and trigger your spray
gun.
2.
Set your operating pressure. After determining
the operating pressure, release the spray gun
trigger and engage the safety latch.
3.
Close the mixer manifold inlet valves.
4.
Slightly open the sampling valve on the
secondary pump side. Slightly open the sampling
valve on the primary pump side. This will prevent
pressure from building up on the secondary
pump and causing the relief valve to open.
5.
Place a grounded waste container under the
sampling valve.
6.
Open the mixer manifold. Use the sampling
valves to adjust the pressures to your
normal
normal
normal
operating
operating
operating pressures
pressures
pressures
.
7.
Close the mixer manifold. Put the sampling
containers under the sampling valves.
8.
Open the mixer manifold. Check the ratio; make
sure the pressure is within 20% of your normal
operating pressure. Close the mixer manifold
when enough fluid has been dispensed into the
sampling containers.
Note
If the pressure readings are not within 20%
of your normal operating pressure, follow
, then take a sample again.
If your sample ratio is incorrect, there is
a problem with the sampling valves, ratio
setting, or pump operation. Check the ratio
setting or service the sampling valves or
pump.
3A3092A
13