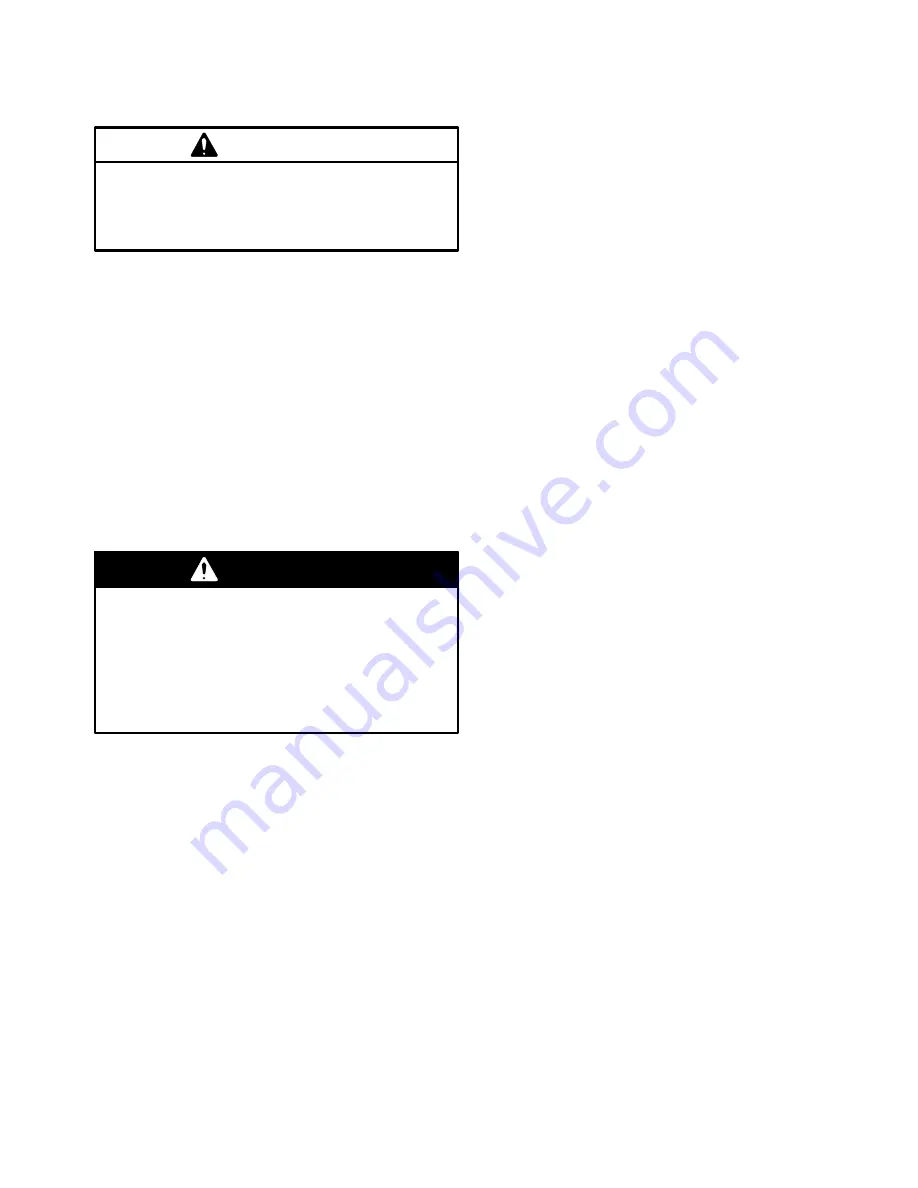
308368
5
Installation
Mountings
CAUTION
The pump exhaust air may contain contaminants.
Ventilate to a remote area if the contaminants
could affect your fluid supply. See
Air Exhaust
Ventilation
on page 8.
D
Be sure the mounting surface can support the
weight of the pump, hoses, and accessories, as
well as the stress caused during operation.
D
For all mountings, be sure the pump is bolted
directly to the mounting surface.
D
For ease of operation and service, mount the pump
so the air valve cover (2), air inlet, and fluid inlet
and outlet ports are easily accessible.
D
Rubber Foot Mounting Kit 236452 is available to
reduce noise and vibration during operation.
Air Line
WARNING
A bleed-type master air valve (B) is required in
your system to relieve air trapped between this
valve and the pump. Trapped air can cause the
pump to cycle unexpectedly, which could result in
serious injury, including splashing in the eyes or on
the skin, injury from moving parts, or contamination
from hazardous fluids. See Fig. 2.
1.
Install the air line accessories as shown in Fig. 2.
Mount these accessories on the wall or on a
bracket. Be sure the air line supplying the acces-
sories is grounded.
a.
Install an air regulator (C) and gauge to control
the fluid pressure. The fluid outlet pressure will
be the same as the setting of the air regulator.
b.
Locate one bleed-type master air valve (B)
close to the pump and use it to relieve trapped
air. See the
WARNING
above. Locate the
other master air valve (E) upstream from all air
line accessories and use it to isolate them
during cleaning and repair.
c.
The air line filter (F) removes harmful dirt and
moisture from the compressed air supply.
2.
Install a grounded, flexible air hose (A) between
the accessories and the 1/2 npt(f) pump air inlet
(N). See Fig. 2. Use a minimum 1/2” (13 mm) ID
air hose. Screw an air line quick disconnect cou-
pler (D) onto the end of the air hose (A), and screw
the mating fitting into the pump air inlet snugly. Do
not connect the coupler (D) to the fitting until you
are ready to operate the pump.
Installation of Remote Pilot Air Lines
1.
Refer to Parts Drawings. Connect air line to pump
as in preceding steps.
2.
Connect 1/4 in. O.D. tubing to push type connec-
tors (14) on air motor of pump.
NOTE:
by replacing the push type connectors, other
sizes or types of fittings may be used. The new fittings
will require 1/8 in. npt threads.
3.
Connect remaining ends of tubes to external air
signal, such as Graco’s Cycleflo (P/N 195264) or
Cycleflo II (P/N195265) controllers.
Fluid Suction Line
1.
Use grounded fluid hoses (G).
The pump fluid
inlet (R) is 2” npt(f). Screw the fluid fitting into the
pump inlet securely.
2.
If the fluid inlet pressure to the pump is more than
25% of the outlet working pressure, the ball check
valves will not close fast enough, resulting in
inefficient pump operation.
3.
At inlet fluid pressures greater than 15 psi
(0.1 MPa, 1 bar), diaphragm life will be shortened.
4.
See the
Technical Data
on page 28 for maximum
suction lift (wet and dry).