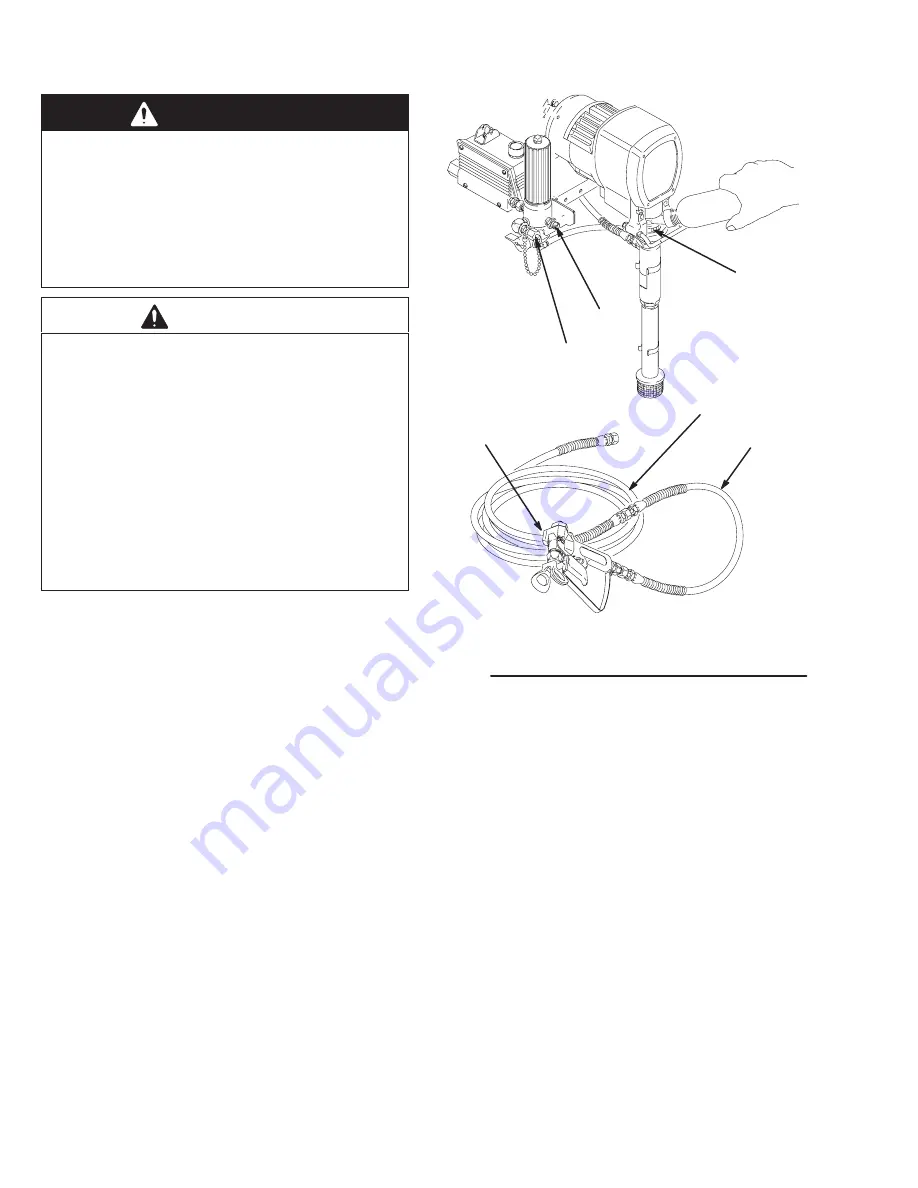
6
308-709
Setup
WARNING
If you supply your own hoses and spray gun, be
sure the hoses are electrically conductive, that the
gun has a tip guard, and that each part is rated for
at least
3000 psi (210 bar, 21 MPa) Maximum
Working Pressure. This is to reduce the risk of
serious bodily injury caused by static sparking, fluid
injection or over-pressurization and rupture of the
hose or gun.
CAUTION
To avoid damaging the pressure control, follow these
precautions.
1.
Always use nylon spray hose at least 50 ft (15.2
m) long.
2.
Never use a wire braid hose; it is too rigid to act
as a pulsation dampener.
3.
Never install a ball valve or shutoff device be-
tween the filter and the 50 ft (15 m) hose.
4.
Always use the main filter outlet for one gun op-
eration. Never plug this outlet.
1.
Connect hose and gun. Remove the plastic cap
plug from the 1/4 npsm(m) outlet nipple (W).
Assemble the 50 ft (15 m) hose (121), 3 ft (0.9 m)
whip hose (122) and gun (123), and connect them
to the outlet nipple.
2.
DO NOT use thread sealant on the hose and gun
connections. DO NOT install the spray tip until the
system is primed.
3.
Two gun hookup. Unscrew the cap (L) from the
secondary hose outlet. Connect an accessory
hose and gun to the 1/4 npsm(m) nipple.
4.
Fill the packing nut/wet-cup (216) 1/3 full with
Graco Throat Seal Liquid (TSL), supplied, and
keep it filled, to help extend the pump life.
Fig. 2
06882
121
122
123
216
L
W