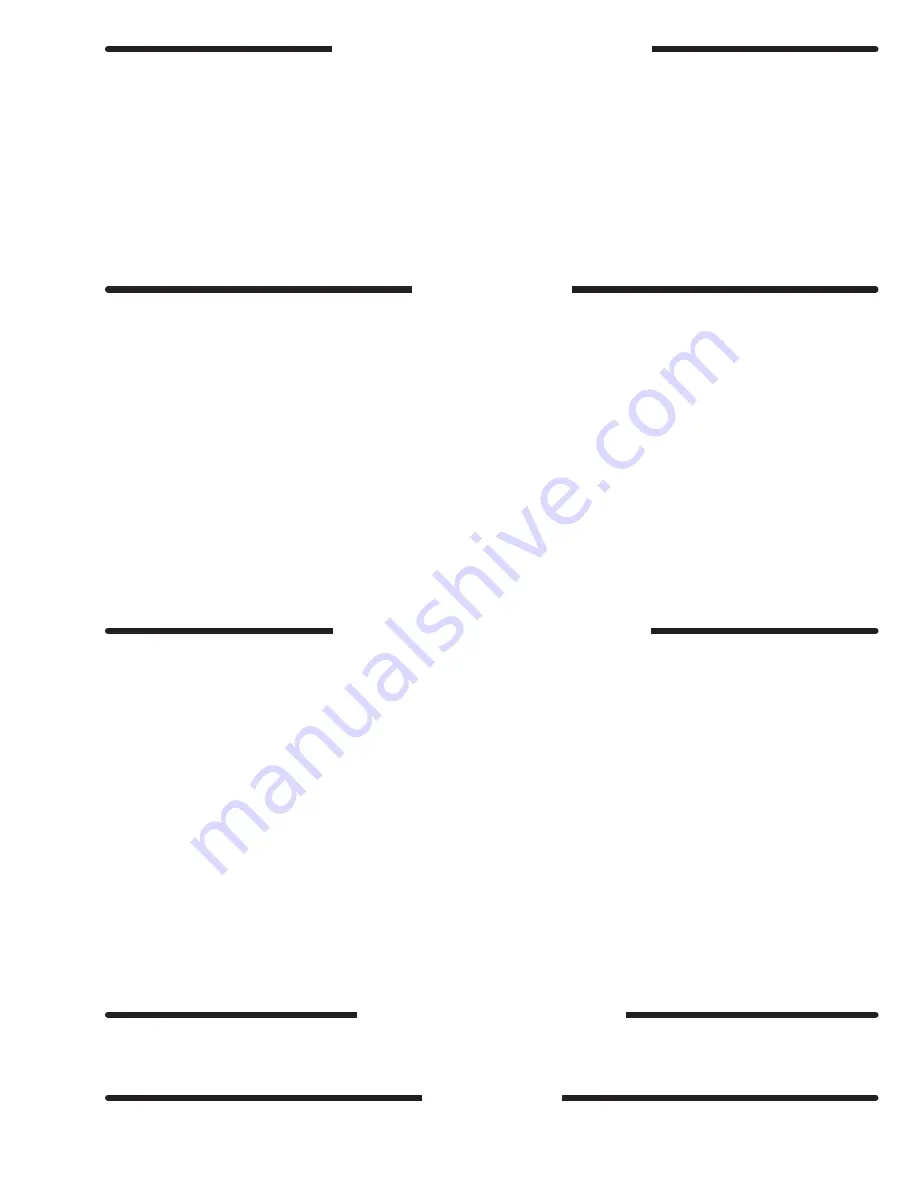
3
308127
EQUIPMENT MISUSE HAZARD
General Safety
Any misuse of the spray equipment or accessories, such as
overpressurizing, modifying parts, using incompatible chemi-
cals and fluids, or using worn or damaged parts, can cause
them to rupture and result in fluid injection, splashing in the
eyes or on the skin, or other serious bodily injury, or fire, ex-
plosion or property damage.
NEVER alter or modify any part of this equipment; doing so
could cause it to malfunction.
CHECK all spray equipment regularly and repair or replace
worn or damaged parts immediately.
Always wear protective eyewear, gloves, clothing and respi-
rator as recommended by the fluid and solvent manufacturer.
System Pressure
This sprayer can develop 3000 psi (210 bar)
MAXIMUM
WORKING PRESSURE. Be sure all spray equipment and
accessories used are rated to withstand the this pressure.
DO NOT exceed the maximum working pressure of any com-
ponent or accessory used in the system.
Fluid and Solvent Compatibility
All chemicals used in the sprayer must be chemically com-
patible with the wetted parts shown in the
TECHNICAL DATA
on page 16. Consult your chemical supplier to ensure com-
patibility.
HOSE
SAFETY
High pressure fluid in the hoses can be very dangerous. If the
hose develops a leak, split or rupture due to any kind of wear,
damage or misuse, the high pressure spray emitted from it
can cause a fluid injection injury or other serious bodily injury
or property damage.
All fluid hoses must have strain reliefs on both ends! The
strain reliefs help protect the hose from kinks or bends at or
close to the coupling which can result in hose rupture.
Tighten all fluid connections securely before each use. High
pressure fluid can dislodge a loose coupling or allow high
pressure spray to be emitted from the coupling.
Never use a damaged hose. Before each use, check the en-
tire hose for cuts, leaks, abrasion, bulging cover, or damage
or movement of the hose couplings. If any of these conditions
exist, replace the hose immediately. Do Not try to recouple
high pressure hose or mend it with tape or any other device.
A repaired hose cannot contain the high pressure fluid.
HANDLE AND ROUTE HOSES CAREFULLY. Do not pull on
hoses to move equipment. Keep hoses clear of moving parts
and hot surfaces of the pump and gas engine. Do not use
fluids or solvents which are not compatible with the inner tube
and cover of the hose. DO NOT expose Graco hoses to tem-
peratures above 180 F (82 C) or below –40 F (–40 C).
Hose Grounding Continuity
Proper hose grounding continuity is essential to maintaining a
grounded spray system. Check the electrical resistance of
your fluid hoses at least once a week. If your hose does not
have a tag on it which specifies the maximum electrical resis-
tance, contact the hose supplier or manufacturer for the maxi-
mum resistance limits. Use a resistance meter in the appro-
priate range for your hose to check the resistance. If the
resistance exceeds the recommended limits, replace it imme-
diately. An ungrounded or poorly grounded hose can make
your system hazardous. Also read
FIRE OR EXPLOSION
HAZARD, below.
Always read the chemical manufacturer’s literature before
using them in this sprayer.
FIRE OR EXPLOSION HAZ-
ARD
Static electricity is created by the flow of fluid through the
pump and hose. If every part of the spray equipment is not
properly grounded, sparking may occur, and the system may
become hazardous. Sparking may also occur when plugging
in or unplugging a power supply cord or using a gasoline en-
gine. Sparks can ignite fumes from solvents and the fluid be-
ing sprayed, dust particles and other flammable substances,
whether you are spraying indoors or outdoors, and can cause
a fire or explosion and serious bodily injury and property
damage.
If you experience any static sparking or any slight shock
while using this equipment,
stop spraying immediately.
Check the entire system for proper grounding. Do not use the
system again until the problem is identified and corrected.
Grounding
To reduce the risk of static sparking, ground the sprayer and
all other spray equipment used or located in the spray area.
Check your local electrical code for detailed grounding in-
structions for your area and type of equipment. Be sure to
ground all of this spray equipment:
1.
Sprayer: Connect a ground wire and clamp (supplied) to a
true earth ground.
2.
Fluid hoses: use only grounded hoses with a maximum
o
f
500 ft. (150 m) combined hose length to ensure grounding
continuity. See
Hose Grounding Continuity, above.
3.
Spray gun: obtain grounding through connection to a prop-
erly grounded fluid hose and sprayer.
4.
Object being sprayed: according to local code.
5.
Fluid supply container: according to local code.
6.
All solvent pails used when flushing, according to local
code. Use only metal pails, which are conductive. Do not
place the pail on a non–conductive surface, such as paper
or cardboard, which interrupts the grounding continuity.
7.
To maintain grounding continuity when flushing or relieving
pressure, always hold a metal part of the gun firmly to the
side of a grounded metal pail, then trigger the gun.
Flushing Safety
Reduce the risk of fluid injection injury, static sparking, or
splashing by following the flushing procedure given on page
6 of this manual. Follow the
PRESSURE RELIEF PROCE-
DURE on page 2, and remove the spray tip before flushing.
Hold a metal part of the gun firmly to the side of a grounded
metal pail and use the lowest possible fluid pressure during
flushing.
MOVING PARTS HAZARD
Moving parts can pinch or amputate your fingers or other body parts. KEEP CLEAR of moving parts when starting or operating
the sprayer. Follow the
Pressure Relief Procedure on page 2 before checking or servicing any part of the sprayer, to prevent it
from starting accidentally.
IMPORTANT
United States Government safety standards have been adopted under the Occupational Safety and Health Act. These standards
– particularly the General Standards, Part 1910, and the Construction Standards, Part 1926 – should be consulted.