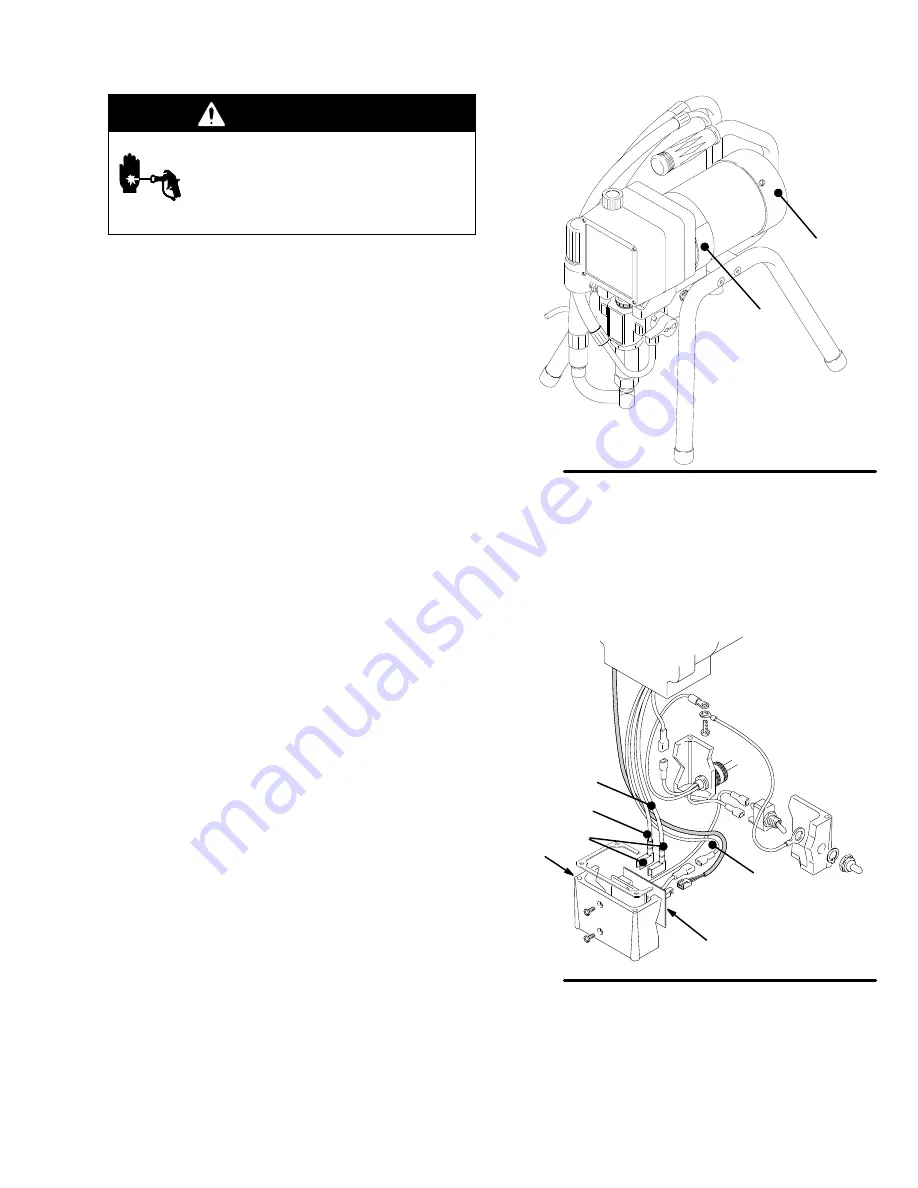
308-256
17
Motor Test
WARNING
INJECTION HAZARD
To reduce the risk of serious injury,
whenever you are instructed to relieve
pressure, follow the
Pressure Relief
Procedure
on page 9.
For checking armature, motor winding, and brush
electrical continuity.
Setup
Remove the drive housing. See page 26. This is to
ensure that any resistance you notice in the armature
test is due to the motor and not to worn gears in the
drive housing.
Remove the motor brush inspection covers (A). See
Fig. 12.
Remove the junction box screws (56). Lower the
junction box. Disconnect the two leads (C) from the
motor to the board (47). See Fig. 13.
Armature Short Circuit
Remove the handle (24) and the fan cover (B). See
Fig. 12.
Spin the motor fan by hand. If there are no shorts, the
motor will coast two or three revolutions before coming
to a complete stop. If the motor does not spin freely,
the armature is shortened and the motor must be
replaced. See page 24.
Armature, Brushes, and Motor Wiring
Open Circuit Test (Continuity)
Connect the two black motor leads together with a test
lead. Turn the motor fan by hand at about two revolu-
tions per second.
When turning the fan on a DC motor, normally you
sense an even, pulsing resistance. If there is irregular
turning resistance, check and repair the following as
needed: broken brush springs, brush leads, motor
leads; loose brush terminal screws or motor lead
terminals; worn brushes. See page 19.
If there is still uneven or no turning resistance, replace
the motor. See page 24.
A
B
Fig. 12
02829A
MOTOR
BLACK/
WHITE
BLACK
C
59
RED
Fig. 13
47
Summary of Contents for Fuller O'brien Paints Pro 501st 231
Page 5: ...Notes...