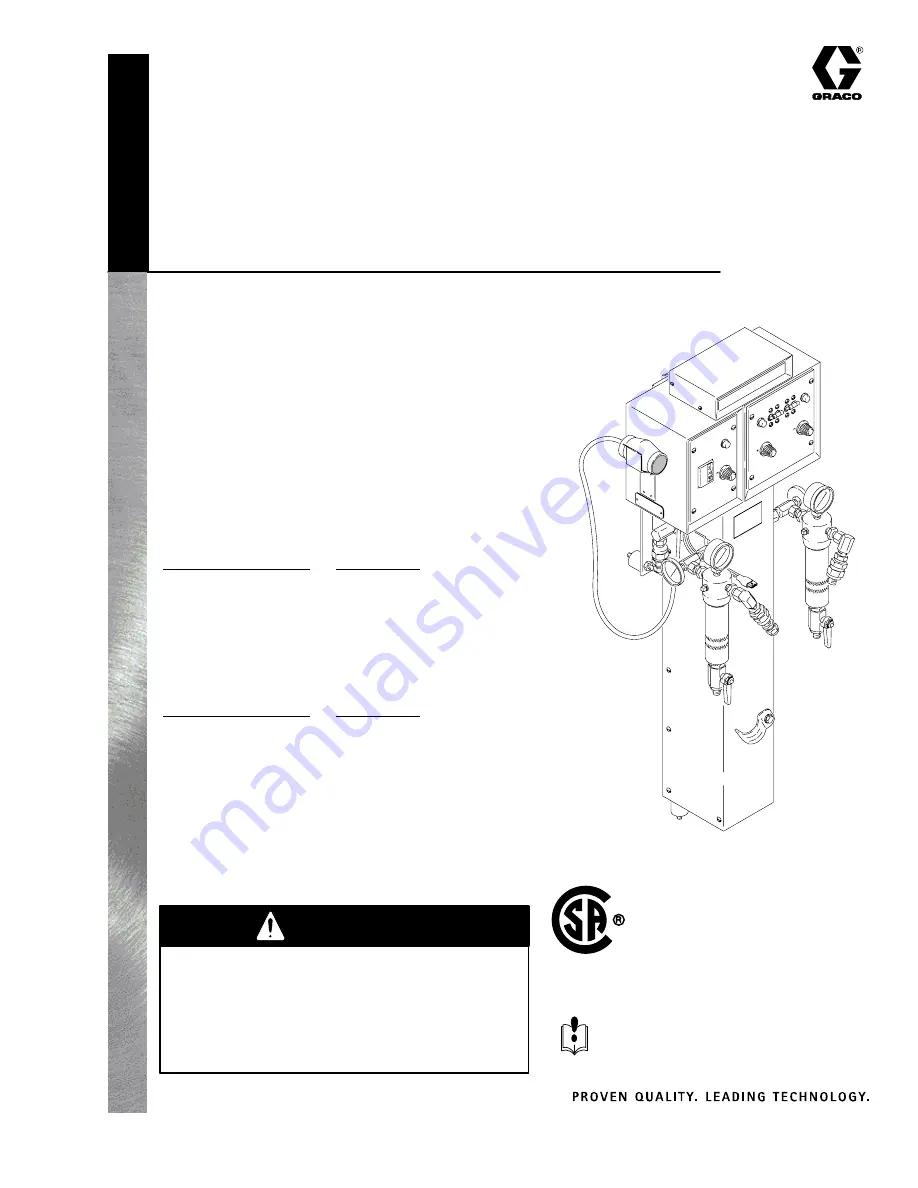
Instructions – Parts List
GRACO INC.ąP.O. BOX 1441ąMINNEAPOLIS, MNą55440-1441
Copyright 1992, Graco Inc. is registered to I.S. EN ISO 9001
308219G
WARNING
FIRE, EXPLOSION, AND ELECTRIC
SHOCK HAZARD
The operating and safety features of this heater are
designed for use
only
with the Graco Foam-Cat
r
Heated Hoses: Models 218613 and 218614. To
reduce the risk of serious injury, never connect
other hoses to this heater.
CSA certified for use with 218613,
Series B, and 218614, Series B,
Heated Hoses.
Read warnings and instructions.
See page 2 for Table of Contents.
FOAM–CAT
R
HEATER
For use ONLY with two component urethane fluids that are unfilled
and non–flammable.
3000 psi (21 MPa, 210 bar) Maximum Working Pressure
Temp. Class T2C (230
_
C) Maximum Fault Temperature
Nominal Operating Temperature: 95–158
_
F (35–70
_
C)
Ambient Temperature Range: 40–104
_
F (5–40
_
C)
This heater includes a heating element and an independent
temperature for each of two fluids, Isocyanate and Resin,
and an independent temperature control for the Foam–Cat
r
Heated Hose.
Foam-Cat
r
200
15
lb/min
Model 235259
With Heated Hose Control
Series B
8880 Watt
Model 235839
Without Heated Hose Control
Series B
5100 Watt
Foam-Cat
r
400
30
lb/min
Model 235260
With Heated Hose Control
Series B
13,980 Watt
Model 235840
Without Heated Hose Control
Series B
10,200 Watt
U.S. Patent No. 4,501,952; 4,725,713
U.K. Patent No. 2,138,601
Patented Bréveté 1986 Canada
01292
Summary of Contents for FOAM-CAT 200 Series
Page 33: ...33 308219 Notes...