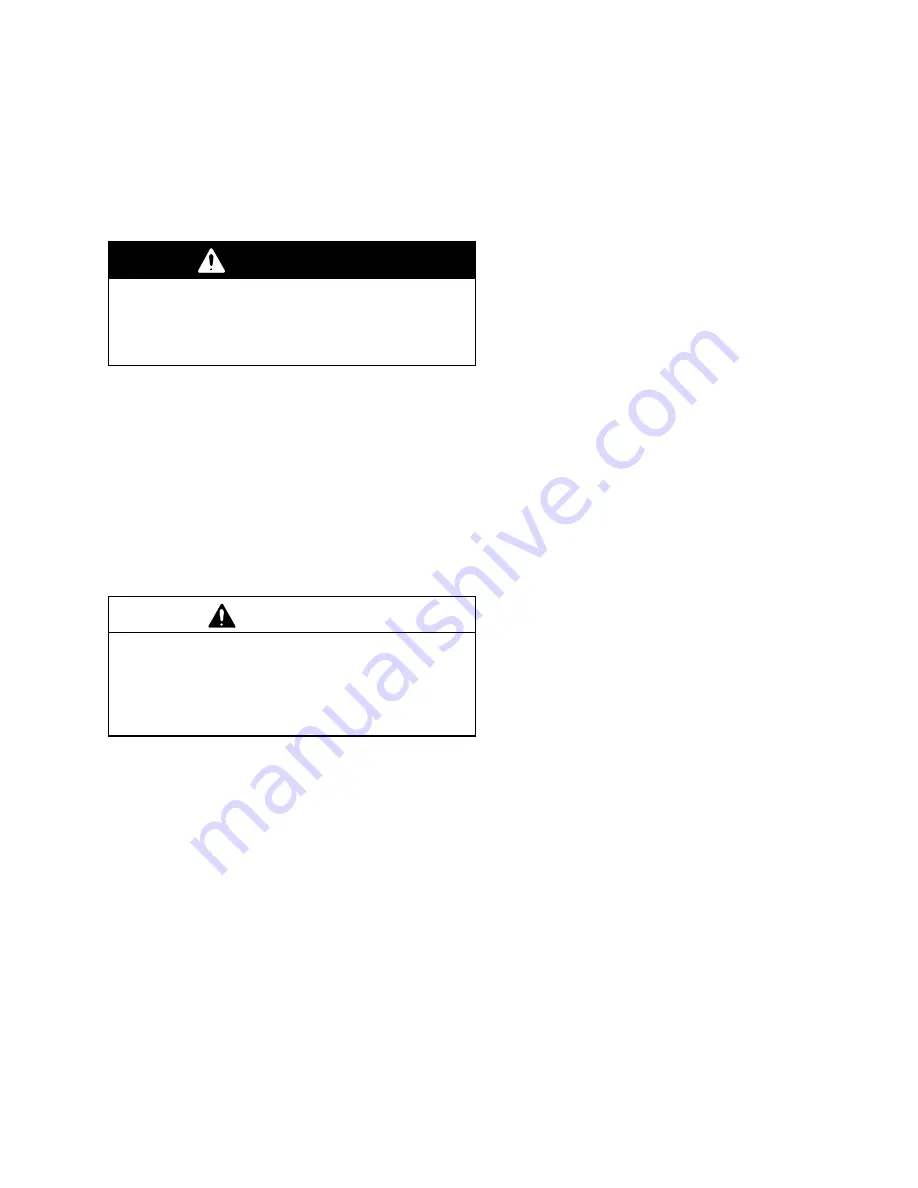
307456
7
Service
NOTE: Repair Kit 214584 is available. For best results,
use all the new parts in the kit, even if the old parts
look good. Parts included in the kit are marked with a
dagger, for example (6†), in the text and illustrations.
Air Piston and Lower Spring Service
WARNING
To reduce the risk of injury from trapped air pres-
sure when servicing the air motor, always remove
air cap (7) from air cylinder (8) before removing air
cylinder from base (22).
1.
Unscrew the cylinder cap (7) from the cylinder (8).
To remove the spring (5), pry gently under the coils
in the direction of the helix.
2.
Unscrew the cylinder (8) from the base (22) and lift
the cylinder off the air piston (11). Using a pliers
(B) on the air exhaust plate (16) and a wrench (C)
on the piston shaft (23), unscrew the piston from
the shaft. See Fig. 2.
CAUTION
Ketone fumes may damage the piston o-rings. When
pumping ketones (such as acetone, MEK, etc.), use
Conversion Kit 221038. This kit replaces the stan-
dard fluoroelastomer o-rings with EPDM o-rings
which are resistant to ketones.
3.
Disassemble the piston and wash all parts in
compatible solvent. Refer to the parts list on
page 9. Blow parts dry and inspect for wear or
damage. If any of the valve plate spacers (13) are
damaged, replace all three to maintain proper
clearance between the valve plates and the seats.
4.
Remove and inspect the lower spring (20). Re-
place if necessary, and reinstall.
5.
A decrease in performance accompanied by a
slower than normal cycle rate is commonly caused
by icing. It is recommended that the pump is shut
down, and the ice is allowed to thaw.
6.
Reassemble the air piston (11), using new parts as
needed. Apply a good grade of thread sealant to
the threads of the screws (12). and torque evenly
to 1.1–1.6 N
S
m (10–14 in-lb). With the washer (4)
in place, apply thread sealant to the threads of the
piston. Carefully screw the piston (11) onto the
shaft (23) by hand so it is securely fastened. Do
not use pliers on the air exhaust plate while tight-
ening. When installed, there should be 0.8 mm
(0.032 in.) minimum clearance between the wash-
er (4) and the piston shaft shoulder. See Fig. 2.
Packing Replacement
1.
Unscrew the cylinder cap (7) from the cylinder (8).
To remove the spring (5), pry gently under the coils
in the direction of the helix.
2.
Unscrew the cylinder (8) from the base (22) and lift
the cylinder off the air piston (11). Disconnect the
piston shaft (23) from the pump connecting rod
and pull the shaft up out of the air motor base.
Remove and inspect the packing (9†), being
careful not to mar the inner lip. See Fig. 2.
NOTE: Fluoroelastomer packing 111383 is available as
an accessory, for use with solvents not compatible with
the standard nitrile rubber packing.
3.
Replace the packing and reassemble the air motor
in the reverse order of disassembly.
Upper Spring Replacement
Unscrew the cylinder cap (7) from the cylinder (8). To
remove the spring (5), pry gently under the coils in the
direction of the helix.
Cleaning the Muffler
To clean the muffler (26), remove it from the unit and
soak it in mineral spirits, then blow dry with air to
remove excess solvent.