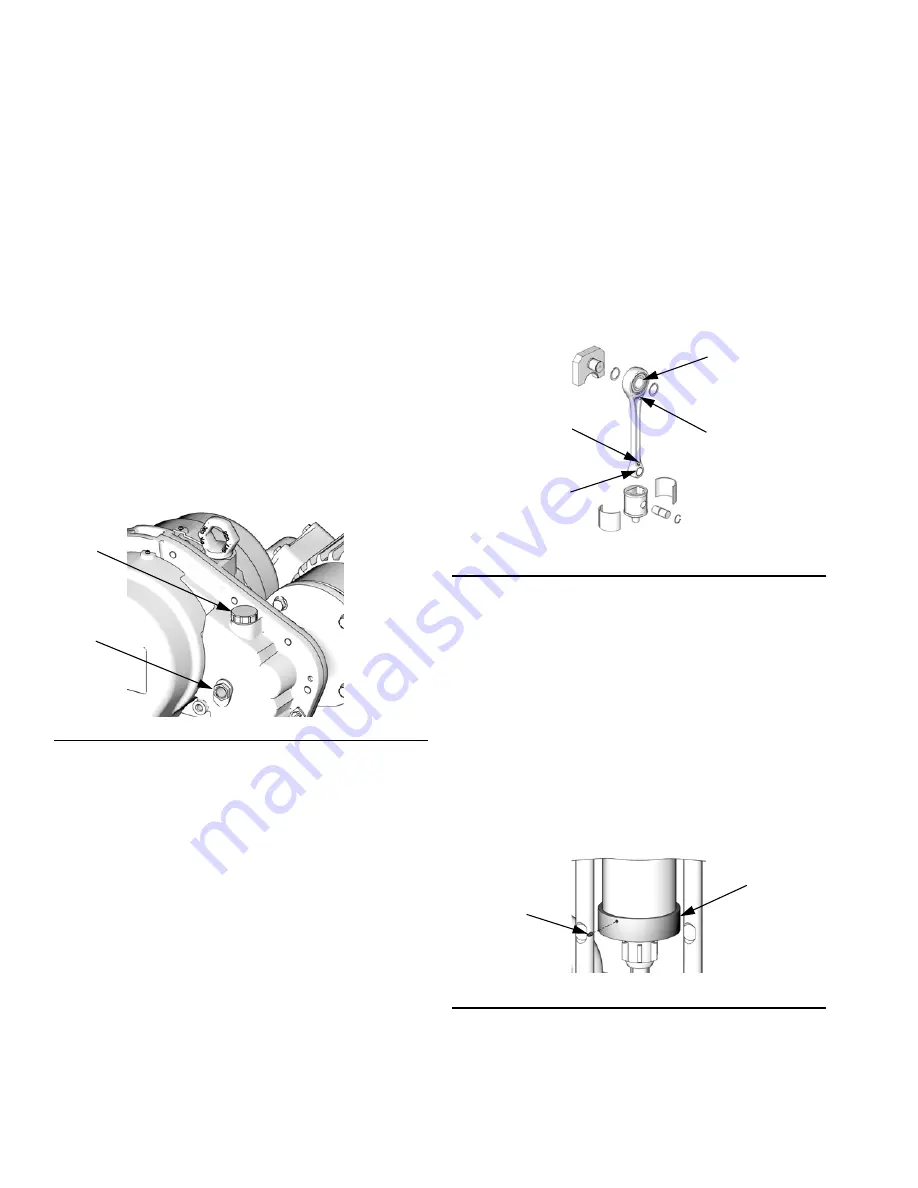
Maintenance
16
311593R
Maintenance
Preventive Maintenance
Schedule
Establish a preventive maintenance schedule based on
the equipment’s repair history.
Check Gear Reducer Oil Level
Every day, check the oil level in the sight glass (SG) on
the gear reducer, with the motor running. Oil level (with
motor running) should fall between top and bottom of
the sight glass (SG). Open the fill cap (FC) and fill the
gear reducer oil reservoir as required with Graco
288414 Oil (package includes twelve 1 quart bottles).
Do not overfill. See F
IG
. 8.
Gear Box and Drive Lubrication
Replace the gear box lubricant after a break-in period of
200,000-300,000 cycles. Order 288414 Replacement
Oil.
Following the break-in period, replace the gear box
lubricant once a year.
See F
IG
. 9. Every 6 months, lubricate the wrist pin bear-
ing (7a) on the connecting rod with 1 shot (1 cc) of
107411 Grease or equivalent, using grease zerk (GZ).
Replace both wrist pin bearings annually. Order Wrist
Pin Replacement Kit 255216. Lubricate the crank pin
bearing (X) annually, using grease zerk (GZ).
NOTE: A faint clicking may be heard while the motor is
running. This is normal and is due to necessary clear-
ances between the coupler (28), motor shaft, and motor
key. If the intensity increases significantly over time, it
could indicate the coupler is wearing and should be
replaced. Do not open the gear reducer. The gear
reducer is not field serviceable beyond the maintenance
recommended in this manual
Clean the Slider Cylinder
Collectors
Every month, check the slider cylinder collectors for dirt
or debris. Remove the 2-piece shield covering the cou-
pling assembly. Loosen the three set screws (SS) on the
collector (CL). Lower the collector and wipe the inside
with a clean, damp cloth. Return the collector to its oper-
ating position. Tighten the screws finger tight. Reinstall
the shields.
F
IG
. 8. Oil Fill
SG
FC
ti8914a
F
IG
. 9. Lubricate Wrist Pin Bearing Every 6 Months
F
IG
. 10. Slider Cylinder Collector
ti8717a
GZ
7a
GZ
X
ti9539a
CL
SS
Summary of Contents for E-Flo 1500
Page 4: ...Models 4 311593R...
Page 10: ...Overview 10 311593R...