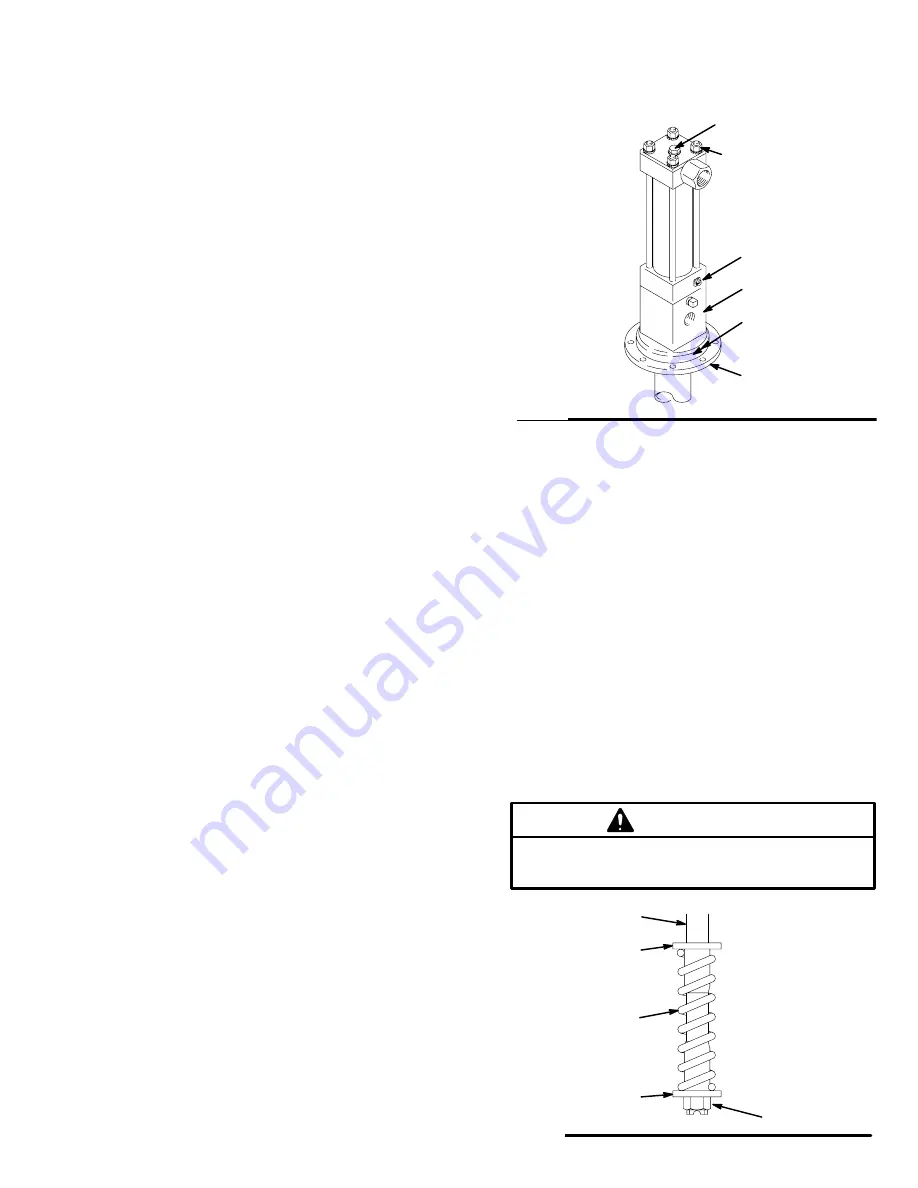
308156
13
Reciprocator Repair
Reciprocator Repair
NOTES
D
Clean and inspect all parts for wear or damage.
Replace parts as needed. For the best results,
always replace all the o-rings and seals when you
disassemble the pump. Repair Kit 223426 is
available. Parts included in the kit are marked with
one asterisk, for example (23*), in the text and
drawings. Always replace the seals (23*,24*) and
the seals (16*, 44*) together.
D
Assembly Tool 189305 is required for
reassembling the reciprocator.
D
Loctite
r
242 thread sealant and Loctite
r
Primer T
or Perma-Loc
r
115 thread sealant and
Perma-Bond
r
Surface Conditioner I are required.
Be sure their shelf life is within the manufacturer’s
recommendations.
Note: Use Loctite
r
609 on yoke (9) and rod (12) on
page 14, step 9 only. Use Loctite
r
242 or
Perma-Loc
r
115 on other threaded surfaces as
required.
Before you begin, drain the oil out of the reciprocator
as follows: Place the reciprocator in a drain pan, push
the piston all the way up/in, then all the way down/out.
1.
Place the adapter (43) in a vise. Remove the four
capscrews (46) and the base (33). Pull the bottom
cap (32) off of the adapter (43). See Fig. 7. If
needed, replace the seals as described on
page 11.
2.
Loosen both nuts on the fluid tube (45). Use a
wrench to rotate the tube fittings (1,58) to the side,
and then remove the tube (45). Check the o-rings
(1a,58a) on the fittings and replace them if they
are worn or damaged. Install plugs in the fittings to
prevent contamination. See Fig. 4 and the Parts
Drawing.
3.
Remove the capscrew (3), nuts (36) and
lockwashers (37) on top of the reciprocator. See
Fig. 7.
Fig. 7
43
36,37
33
32
3,39,2
46
hidden from view
06146B
See Fig. 9 for Steps 4 to 20, except where noted.
4.
Tap on the bottom of the displacement rod (34)
with a plastic mallet to loosen the cylinder (25).
5.
Grasp the valve spool (31) and pull it off the
cylinder and tie rods (38). Pull the cylinder and
piston off the bottom cap (32). It is not necessary
to remove the tie rods from the bottom cap.
6.
Lay the assembly on its side. Place a clean rag
around the yoke (9) to prevent losing the detent
balls. Slide the yoke (9) sideways off the valve
sleeve (29) while holding the balls (7) and spring
(6) in place.
7.
Slide the cylinder (25) off the displacement rod
(34). Hold the hex end of the displacement rod in a
vise and use a spanner wrench in the pin holes of
the piston (22) to screw it off the rod.
CAUTION
Be careful not to scratch the outside of the dis-
placement rod or the inside of the cylinder.
20
21
20
Fig. 8
01664
18
12