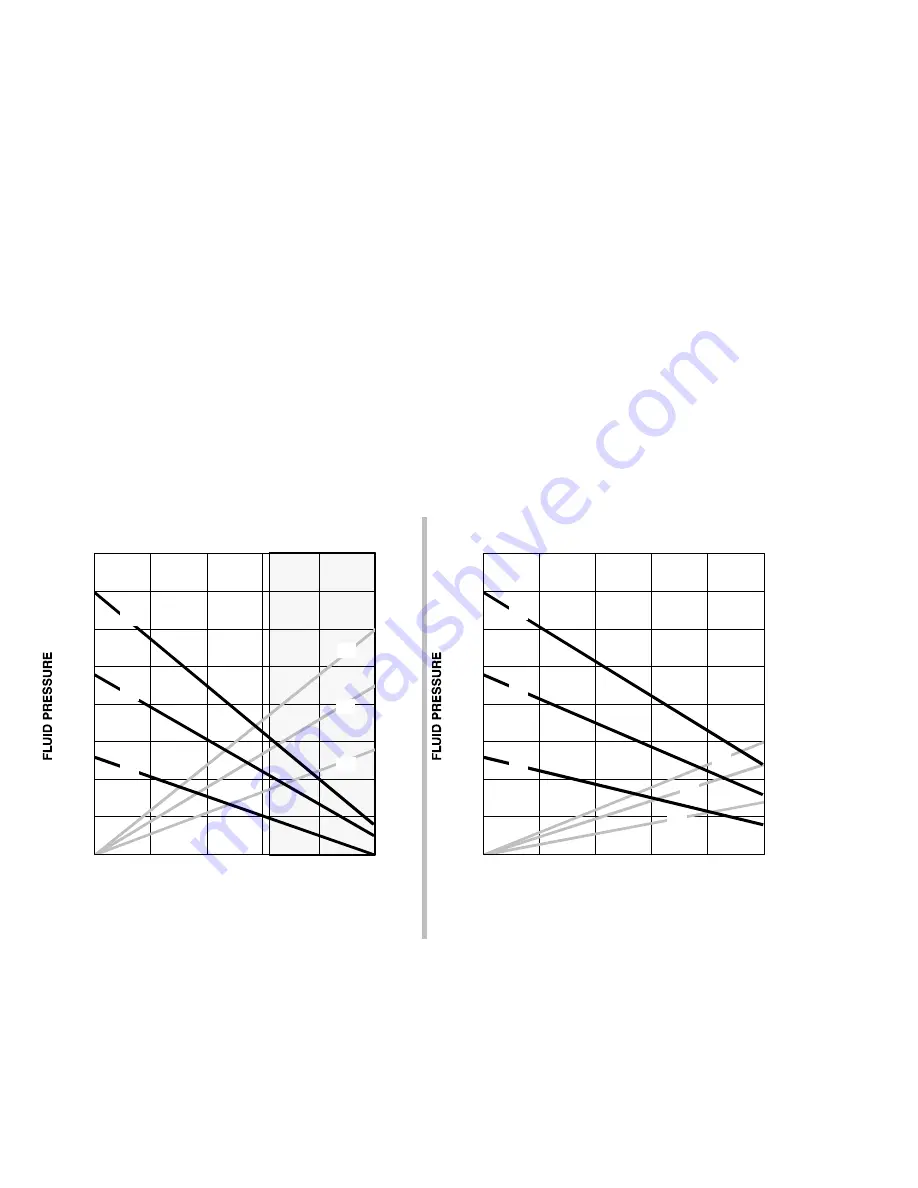
34
308149
Technical Data
(Model 222940 Premier Pump)
Ratio
39:1 (Premier Air Motor)
. . . . . . . . . . . . . . . . . . . . . . . . . . . . . . . . . . . . . . . . . . . . . . . . . . . . . .
Maximum fluid working pressure
26.9 MPa, 269 bar (3900 psi)
. . . . . . . . . . . . . . . . . . . . . . . . . .
Maximum air input pressure
0.7 MPa, 7 bar (100 psi)
. . . . . . . . . . . . . . . . . . . . . . . . . . . . . . . . . .
Pump cycles per 3.8 liters (1 gal.)
8
. . . . . . . . . . . . . . . . . . . . . . . . . . . . . . . . . . . . . . . . . . . . . . . . .
Recommended pump speed for continuous operation
50 cycles per min
. . . . . . . . . . . . . . . . . .
Maximum flow
23.75 liters/min (6.25 gpm) at 50 cycles/min
. . . . . . . . . . . . . . . . . . . . . . . . . . . . .
Air motor piston effective area
800 cm
(38.5 in.
)
. . . . . . . . . . . . . . . . . . . . . . . . . . . . . . . . . . . . .
Stroke length
120 mm (4.75 in.)
. . . . . . . . . . . . . . . . . . . . . . . . . . . . . . . . . . . . . . . . . . . . . . . . . . . . .
Displacement pump effective area
21 cm
(3.255 in.
)
. . . . . . . . . . . . . . . . . . . . . . . . . . . . . . . . . .
Maximum pump operating temperature
65.5
C (150
F)
. . . . . . . . . . . . . . . . . . . . . . . . . . . . . . . .
Air inlet size
3/4 npsm(f)
. . . . . . . . . . . . . . . . . . . . . . . . . . . . . . . . . . . . . . . . . . . . . . . . . . . . . . . . . . .
Fluid outlet size
1–1/2” npt(m)
. . . . . . . . . . . . . . . . . . . . . . . . . . . . . . . . . . . . . . . . . . . . . . . . . . . . . .
Weight
approx. 113 kg (248 lb)
. . . . . . . . . . . . . . . . . . . . . . . . . . . . . . . . . . . . . . . . . . . . . . . . . . . . .
Displacement Pump Weight
approx. 37 kg (81 lb)
. . . . . . . . . . . . . . . . . . . . . . . . . . . . . . . . . . . . .
Wetted parts
Carbon Steel; Chrome, Zinc, and Electroless Nickel Plating;
. . . . . . . . . . . . . . . .
304 and 17–4 PH Grades of Stainless Steel; E52100 Alloy Steel;
Ductile Iron; Acetal; PTFE; Ultra-High Molecular Weight Polyethylene
0
500
1000
1500
2000
2500
3000
3500
4000
0
2
4
6
8
10
NOTE:
Recommended pump speed for continuous operation
(to shaded area): 50 cpm
FLUID FLOW
(TEST FLUID: 100,000 CENTIPOISE SEALANT)
psi
bar
MPa
gpm
liters/min
To find Fluid Outlet Pressure
(MPa/bar/psi) at a specific fluid flow
(lpm/gpm) and operating air pressure (MPa/bar/psi):
1.
Locate desired flow along bottom of chart.
2.
Follow vertical line up to intersection with selected fluid outlet
pressure curve (black). Follow left to scale to read fluid outlet
pressure.
To find Pump Air Consumption
(m
/min or scfm) at a specific fluid
flow (lpm/gpm) and air pressure (MPa/bar/psi):
1.
Locate desired flow along bottom of chart.
2.
Read vertical line up to intersection with selected air consumption
curve (gray). Follow right to scale to read air consumption.
cycles/min
scfm
m
/min
50
100
200
7.6
1.40
2.80
5.60
16
32
80
250
7.00
15.2
22.8
30.4
38.0
35
3.5
105
10.5
64
50
48
cycles/min
16
32
40
8
24
gpm
liters/min
7.6
15.2
3.8
11.4
19.0
FLUID FLOW
(TEST FLUID: 4,000,000 CENTIPOISE SILICON)
210
21.0
140
14.0
300
8.40
KEY:
Fluid Outlet Pressure – Black Curves
A
0.7 MPa, 7 bar (100 psi) Air Pressure
Air Consumption – Gray Curves
B
0.49 MPa, 4.9 bar (70 psi) Air Pressure
C
0.28 MPa, 2.8 bar (40 psi) Air Pressure
A
B
C
A
B
C
70
7.0
175
17.5
245
24.5
280
28.0
150
4.20
0
500
1000
1500
2000
2500
3000
3500
4000
0
1
2
3
4
5
psi
bar
MPa
scfm
m
/min
50
100
200
1.40
2.80
5.60
250
7.00
300
8.40
A
B
C
A
B
C
150
4.20
35
3.5
105
10.5
210
21.0
140
14.0
70
7.0
175
17.5
245
24.5
280
28.0
Summary of Contents for Check-Mate 2100 A Series
Page 6: ...6 308149 Notes...