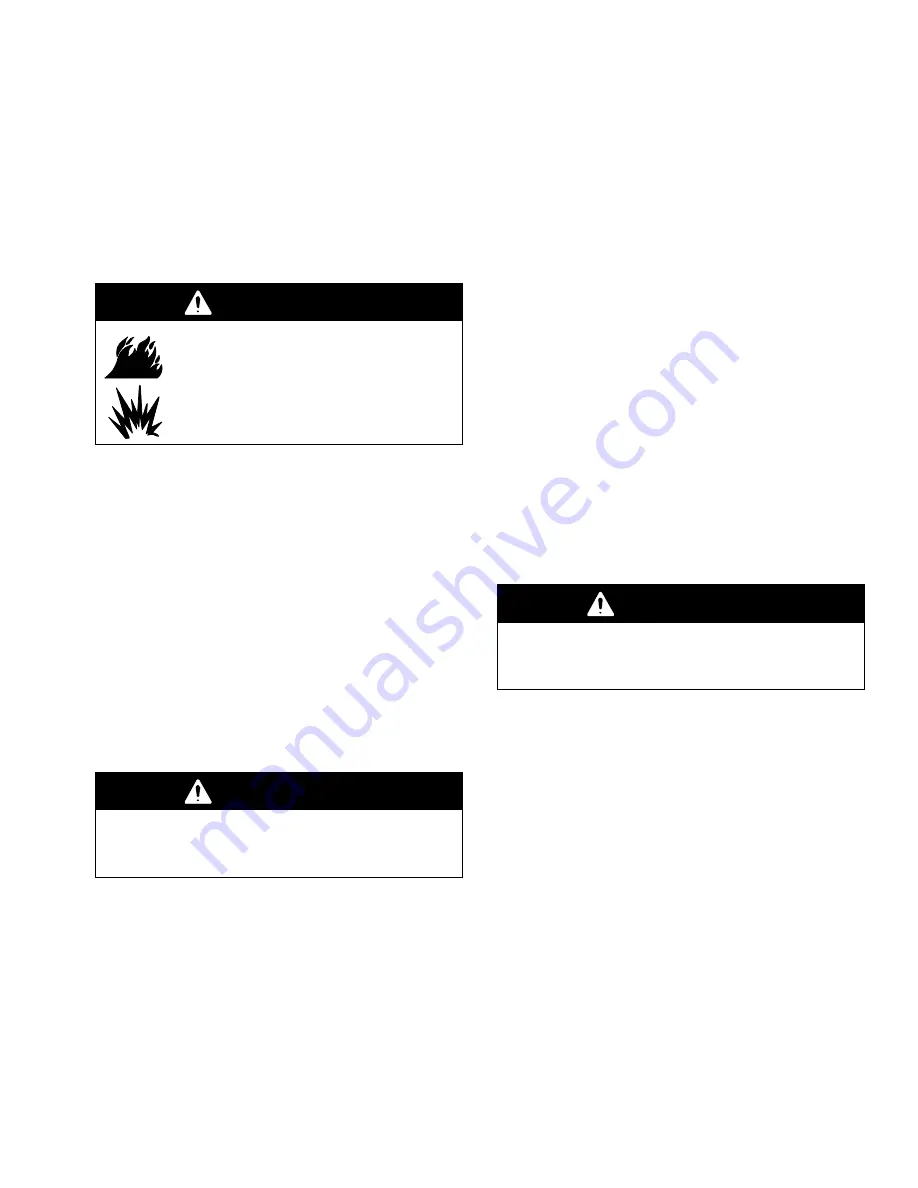
310570
13
Maintenance
Preventive Maintenance Schedule
The operating conditions of your particular system
determine how often maintenance is required. Estab-
lish a preventive maintenance schedule by recording
when and what kind of maintenance is needed, and
then determine a regular schedule for checking your
system.
Flushing
WARNING
FIRE AND EXPLOSION HAZARD
Before flushing, read the section
FIRE
AND EXPLOSION HAZARD
on page
4. Be sure the entire system and flush-
ing pails are properly grounded. Refer to
Grounding
on page 9.
Fig. 4. Flush the pump:
D
Before the first use
D
When changing colors or fluids
D
Before fluid can dry or settle out in a dormant pump
(check the pot life of catalyzed fluids)
D
Before storing the pump.
Flush with a fluid that is compatible with the fluid you
are pumping and with the wetted parts in your system.
Check with your fluid manufacturer or supplier for
recommended flushing fluids and flushing frequency.
WARNING
To reduce the risk of serious injury whenever you
are instructed to relieve pressure, always follow the
Pressure Relief Procedure
on page 10.
1.
Fig. 4. Relieve the pressure.
2.
Remove the air cap and spray tip from the gun.
See the gun manual.
3.
Fig. 4. Remove the filter element from the fluid
filter (8). Reinstall the filter bowl.
4.
Hold a metal part of the gun firmly to the side of a
grounded
metal
pail.
5.
Start the pump. Always use the lowest possible
fluid pressure when flushing.
6.
Trigger the gun. Flush the system until clear
solvent flows from the gun.
7.
Release the gun trigger and lock the trigger safety.
The pump will continue to cycle as long as air is
supplied.
8.
Direct drain hose into a waste container. Continue
flushing until clear fluid comes from the hose.
9.
Relieve the pressure.
10. Clean the air cap, spray tip, and fluid filter element
separately, then reinstall them.
Fluid Filter Service
WARNING
To reduce the risk of serious injury whenever you
are instructed to relieve pressure, always follow the
Pressure Relief Procedure
on page 10.
1.
Fig. 4. Relieve the pressure.
2.
Replace the fluid filter as required to maximize
filtering efficiency and to avoid excessive pressure
drop.
3.
Close two filter ball valves (4). Open filter drain
valve (2) and partially loosen filter top to allow fluid
in filter to drain into waste container.
4.
Install new filter, close filter drain valve (2) and
open filter ball valves (4).
Summary of Contents for 96A390
Page 15: ...310570 15 Notes...