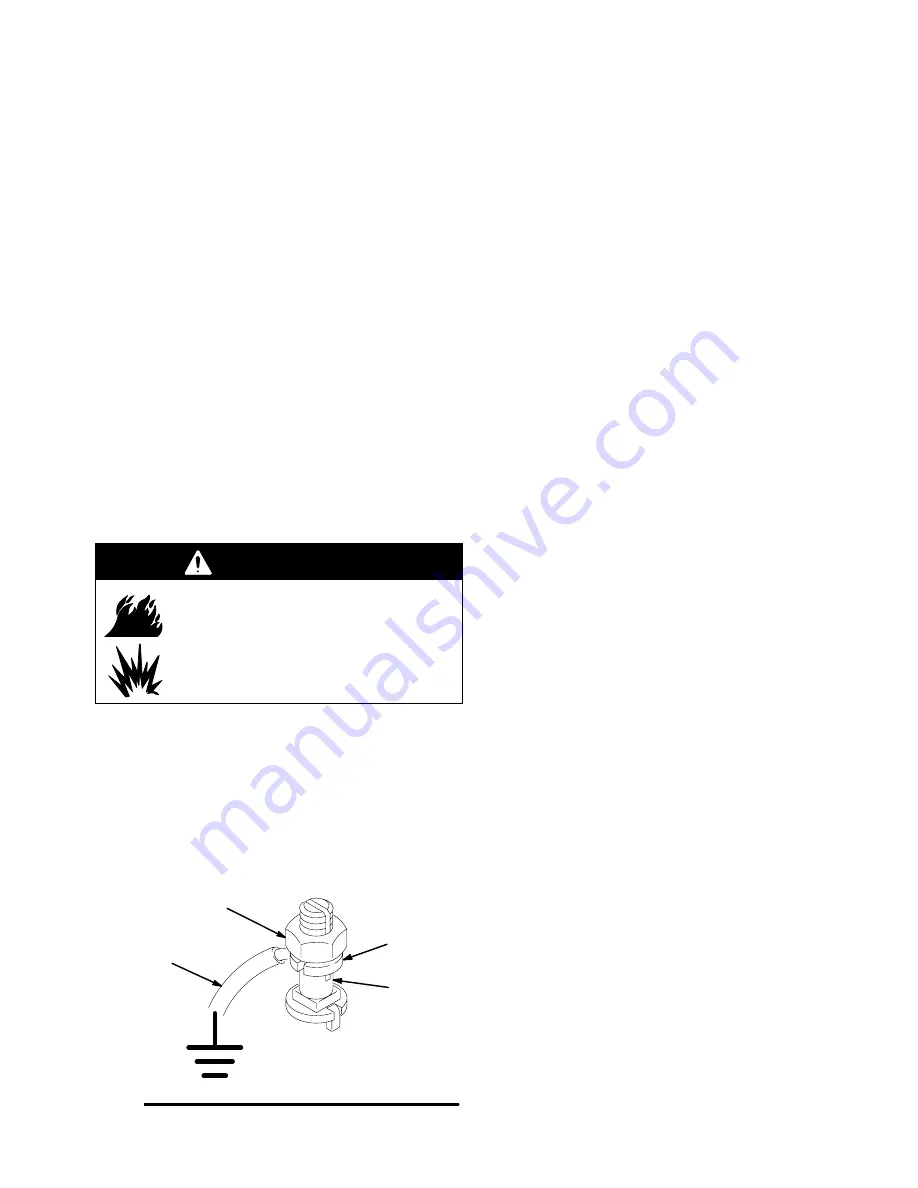
308996
5
Installation
General Information
NOTE: Reference numbers and letters in parentheses
in the text refer to the callouts in the figures and the
parts drawing.
NOTE: Always use Genuine Graco Parts and Acces-
sories, available from your Graco distributor. If you
supply your own accessories, be sure they are ade-
quately sized and pressure rated for your system.
Prepare the Operator
All persons who operate the equipment must be
trained in the safe, efficient operation of all system
components as well as the proper handling of all fluids.
All operators must thoroughly read all instruction
manuals, tags, and labels before operating the equip-
ment.
Grounding
WARNING
FIRE AND EXPLOSION HAZARD
Before operating the pump, ground the
system as explained below. Also read
the section FIRE AND EXPLOSION
HAZARD on page 4.
1.
Pump: use a ground wire and clamp. See Fig. 1.
Loosen the grounding lug locknut (W) and washer
(X). Insert one end of a 1.5 mm
@
(12 ga) minimum
ground wire (Y) into the slot in lug (Z) and tighten
the locknut securely. Connect the other end of the
wire to a true earth ground. Order Part No. 238909
Ground Wire and Clamp.
Fig. 1
W
X
Y
Z
0864
2.
Pump air supply and fluid hoses: Use only electri-
cally conductive hoses with a maximum of 500 feet
(150 m) combined hose length to ensure ground-
ing continuity. Check the electrical resistance of
your air and fluid hoses at least once a week. If the
total resistance to ground exceeds 29 megohms,
replace the hose immediately.
NOTE: Use a meter that is capable of measuring
resistance at this level.
3.
Air compressor: follow manufacturer’s recommen-
dations.
4.
Spray gun: ground through connection to a prop-
erly grounded fluid hose and pump.
5.
Fluid supply container: follow your local code.
6.
Object being sprayed: follow your local code.
7.
Solvent pails used when flushing: follow your local
code. Use only metal pails, which are conductive,
placed on a grounded surface. Do not place the
pail on a nonconductive surface, such as paper or
cardboard, which interrupts the grounding continu-
ity.
8.
To maintain grounding continuity when flushing or
relieving pressure, hold a metal part of the spray
gun firmly to the side of a grounded metal pail,
then trigger the gun.
System Accessories
Fig. 2 is only a guide for selecting and installing sys-
tem components and accessories. Contact your Graco
distributor for assistance in designing a system to suit
your particular needs.
Air and Fluid Hoses
Ensure that you have an adequate compressed air
supply. Bring a compressed air supply line from the air
compressor to the pump location.
Be sure all air hoses (H and D) and fluid hose (N) are
properly sized and pressure-rated for your system.
Use only electrically conductive hoses. Fluid hoses
must have spring guards on both ends.
The air hose (H) should have a 3/8 npt (m) thread. A
quick disconnect coupling is recommended.
Mounting Accessories
Mount the pump (A) to suit the type of installation
planned. Fig. 2 illustrates a wall mount system. Pump
dimensions and the mounting hole layout are shown
on page 25.