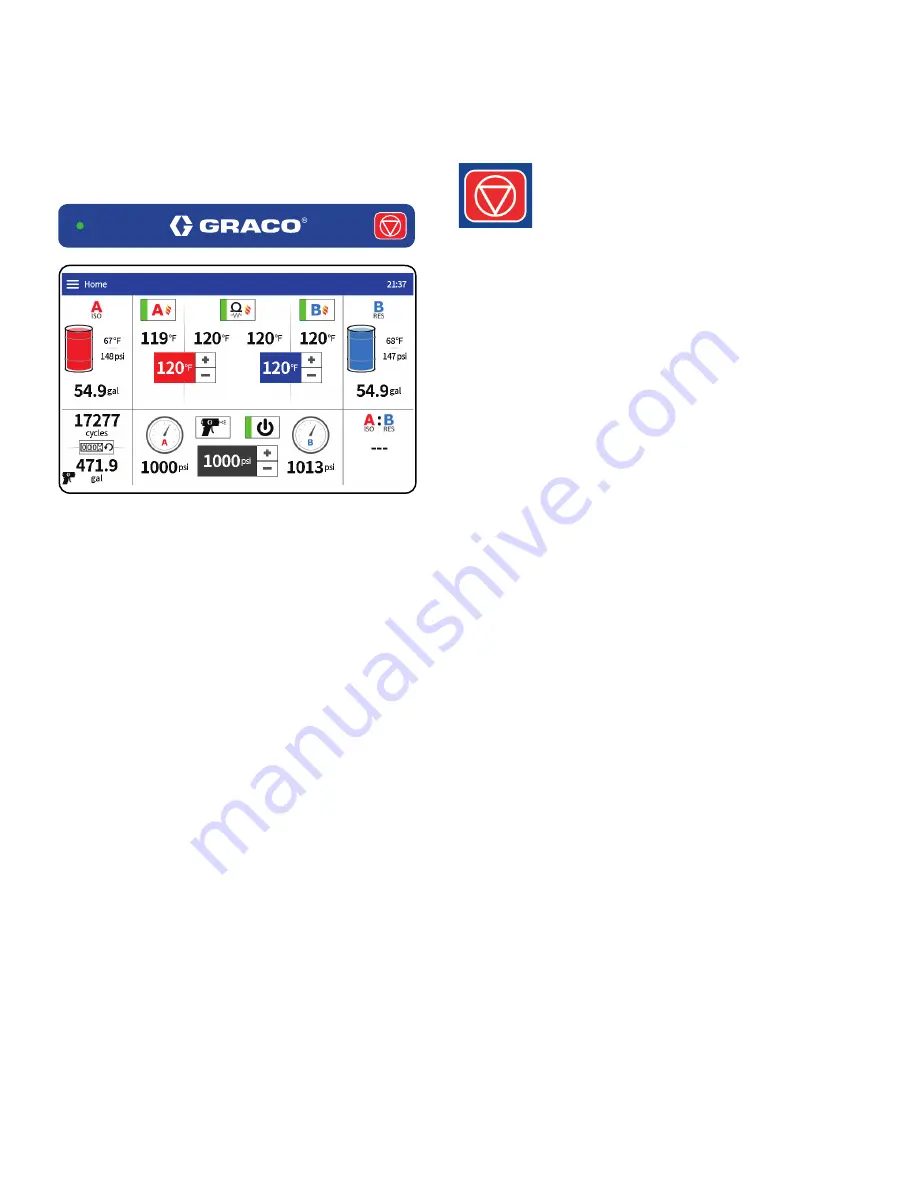
Component Identification
18
3A8501A
Advanced Display Module (ADM)
The ADM display shows graphical and text information
related to setup and spray operations.
ADM Keys and Indicators
NOTE:
For complete description of the ADM icons and
screens, refer to your Reactor 3 operation manual.
ti40087a
Press to stop all proportioner processes.
This is not a safety or emergency stop.
Summary of Contents for 26R310
Page 13: ...Notes 3A8501A 13 Notes ...
Page 49: ...Notes 3A8501A 49 Notes ...
Page 66: ...Parts 66 3A8501A ti39929a ...