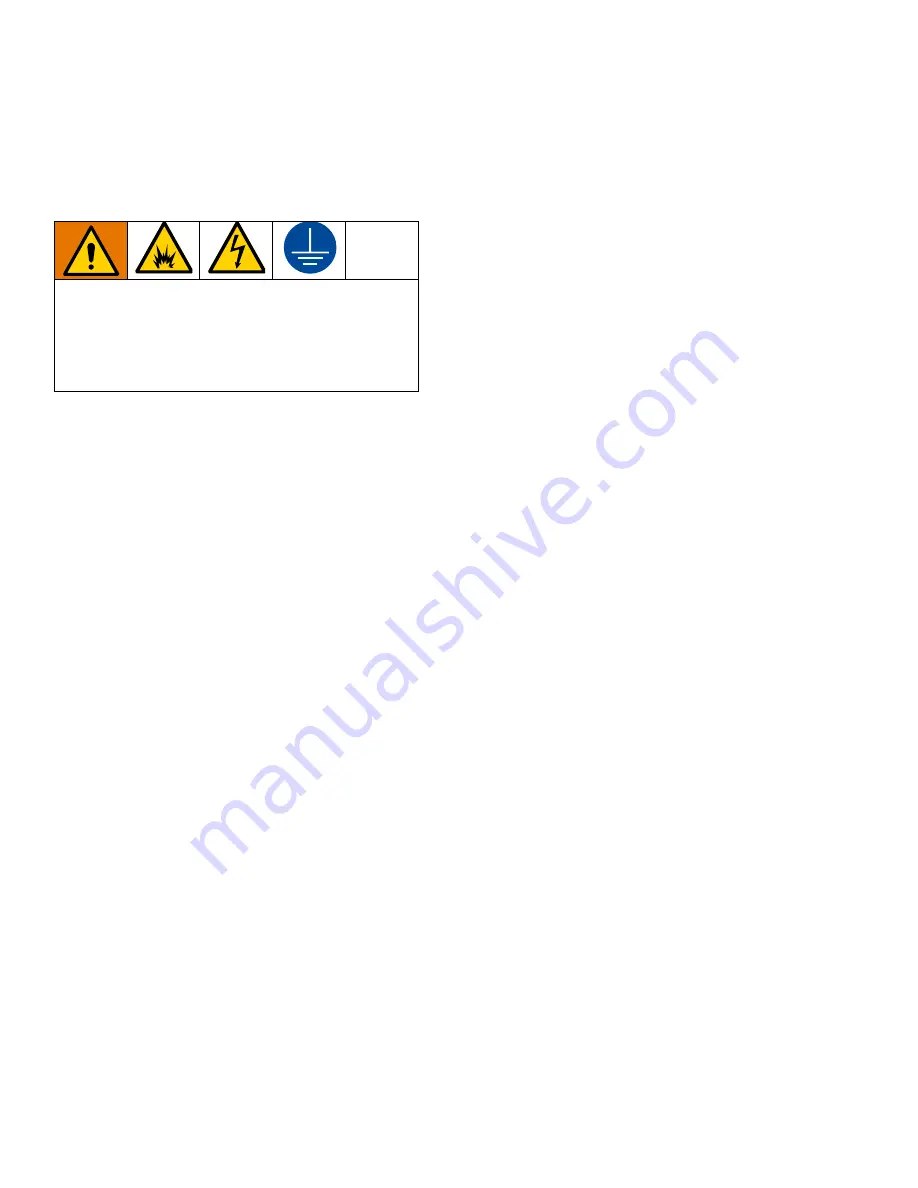
Installation
6
3A8109A
Installation
Grounding
Pump:
Fluid lines:
use only electrically conductive lines.
Fluid supply container:
follow local codes and regula-
tions.
Accessories
Install the following required accessories in the order
shown in
Typical Installation
, page 7, using adapters
as necessary. These required accessories must be sup-
plied and installed by the customer before use.
•
Fluid Filter (Y-Strainer) (included in K):
with a 60
mesh (250 micron) stainless steel element to filter
particles from the fluid before it reaches the pump.
•
Fluid Shutoff Valves (L):
shuts off fluid flow.
•
Pressure Relief Valve (D):
overpressure protec-
tion.
Flush Before Using Equipment
The equipment was tested with lightweight oil, which is
left in the fluid passages to protect parts. To avoid con-
taminating your fluid with oil, flush the equipment with a
compatible solvent before using the equipment. See
, page 10.
The equipment must be grounded to reduce the risk
of static sparking and electric shock. Electric or static
sparking can cause fumes to ignite or explode.
Improper grounding can cause electric shock.
Grounding provides an escape wire for the electric
current.