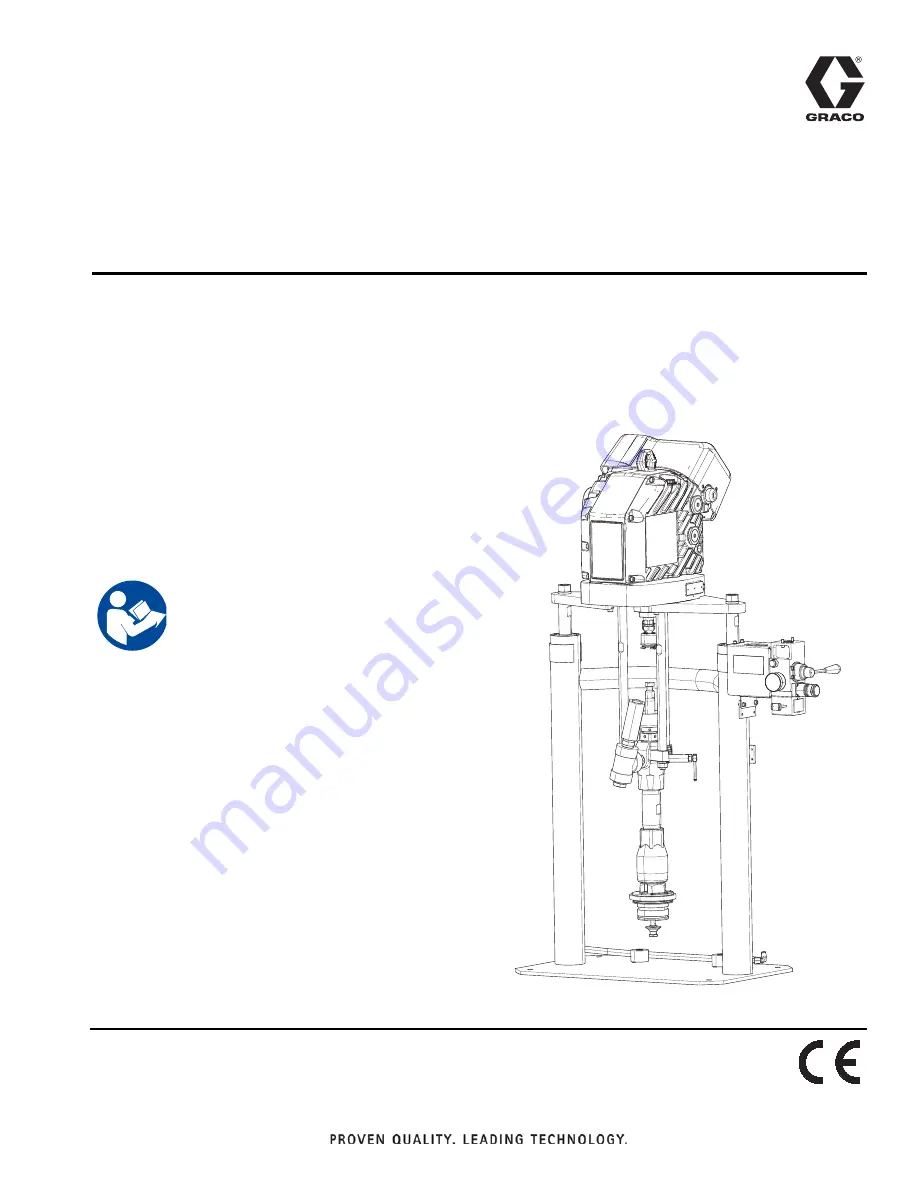
3A5379B
EN
Operation
Electric Supply
Systems for Sealants
and Adhesives
For use with non-heated bulk supply of medium to high viscosity sealants and adhesive
materials. For professional use only.
Not approved for use in explosive atmospheres or hazardous locations.
D60 3 inch dual post
60 liter (16 gallon) size, 30 liter (8 gallon),
20 Liter (5 gallon) sizes
150 psi (1.0 MPa, 10 bar) Maximum Air Inlet Pressure
See page 3 for model information, including maximum
working pressure and approvals.
Important Safety Instructions
Read all warnings and instructions in this
manual and in your pump manual before
using the equipment. Save all instruc
-
tions.