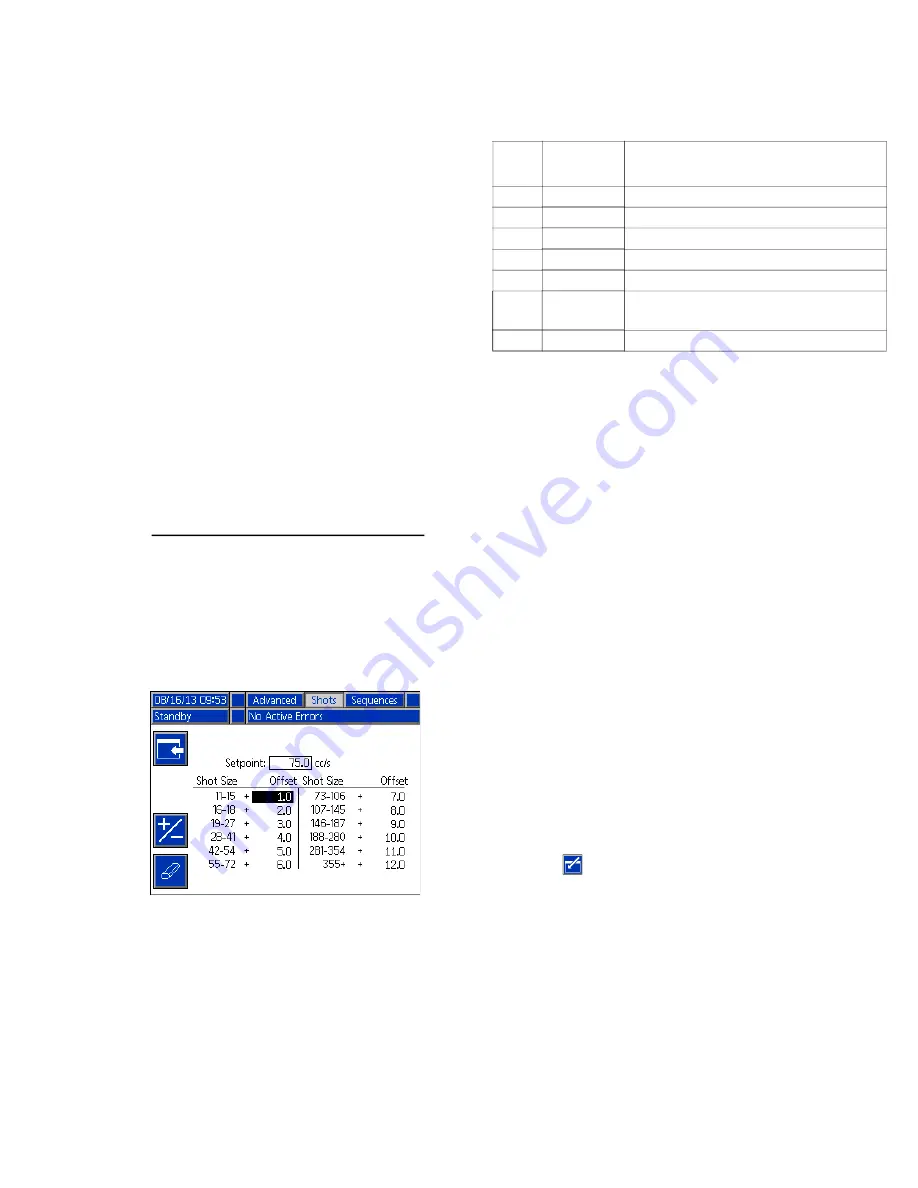
Appendix B - ADM Setup Screens Overview
3A2797ZAA
57
Weight Based Example Using Shot Calibration
Table:
NOTE:
The offset needs to be determined for each
range and may need to be modified if the flow rate
changes. Visit www.graco.com and search for PKE
“Shot Calibration Table Worksheet” to assist in the cal
-
culations for the following procedure.
NOTE:
Offset ranges are dependent on material ratio
and material specific gravity. The values shown are for
reference only.
1. Dispense five shots into separate containers for an
average range.
2. Measure the amount for each shot size and record
the data.
3. Repeat steps 1 and 2 for all twelve ranges.
4. Calculate the average for each range and record
the data.
5. Calculate the offset of each shot size and record
the data.
6. Enter the offset into the table.
7. Repeat steps 1 through 6 for more precise offsets.
Example:
Sequences Screen
These screens allow the user to select a sequence of
shot numbers or recipe numbers previously defined in
the Shot screens. After a sequence is defined, the user
can dispense the sequence starting from the first posi
-
tion containing a shot number, and ending with the last
position containing a non-zero number. The Sequence
screens will only allow the user to select a shot number
previously defined in the Shot screens. Shot numbers
containing blank data will not be available for selection
in a sequence. Blank positions (containing a 0) in
sequence will be skipped by the HFR sequence logic.
For example, sequence “Y” in the screen shown below
will dispense shot numbers 11, 12, 13, 14, 15, and end
with 16 if executed completely.
See
on page 72 for
information on how to use predefined sequences.
NOTE:
26 (A-Z) sequences with up to 20 positions each
are available across 52 pages.
NOTE:
Sequence positions are made from shots
defined in the
To edit a sequence:
1. Press
then use the arrow keys to navigate to
the desired value.
(Shot1 + Shot2 + Shot3 + Shot4 + Shot5)
5
Target Shot Size - Average Shot Size
Step
Ref.
Shot
Number
Range: 11-15g
Target Shot Size: 13g
1,2
Shot 1
11.600
1,2
Shot 2
12.200
1,2
Shot 3
12.400
1,2
Shot 4
11.900
1,2
Shot 5
12.000
4
Average
Shot Size
12.02
5
Offset
0.98
Summary of Contents for 24N572
Page 31: ...Setup 3A2797ZAA 31...