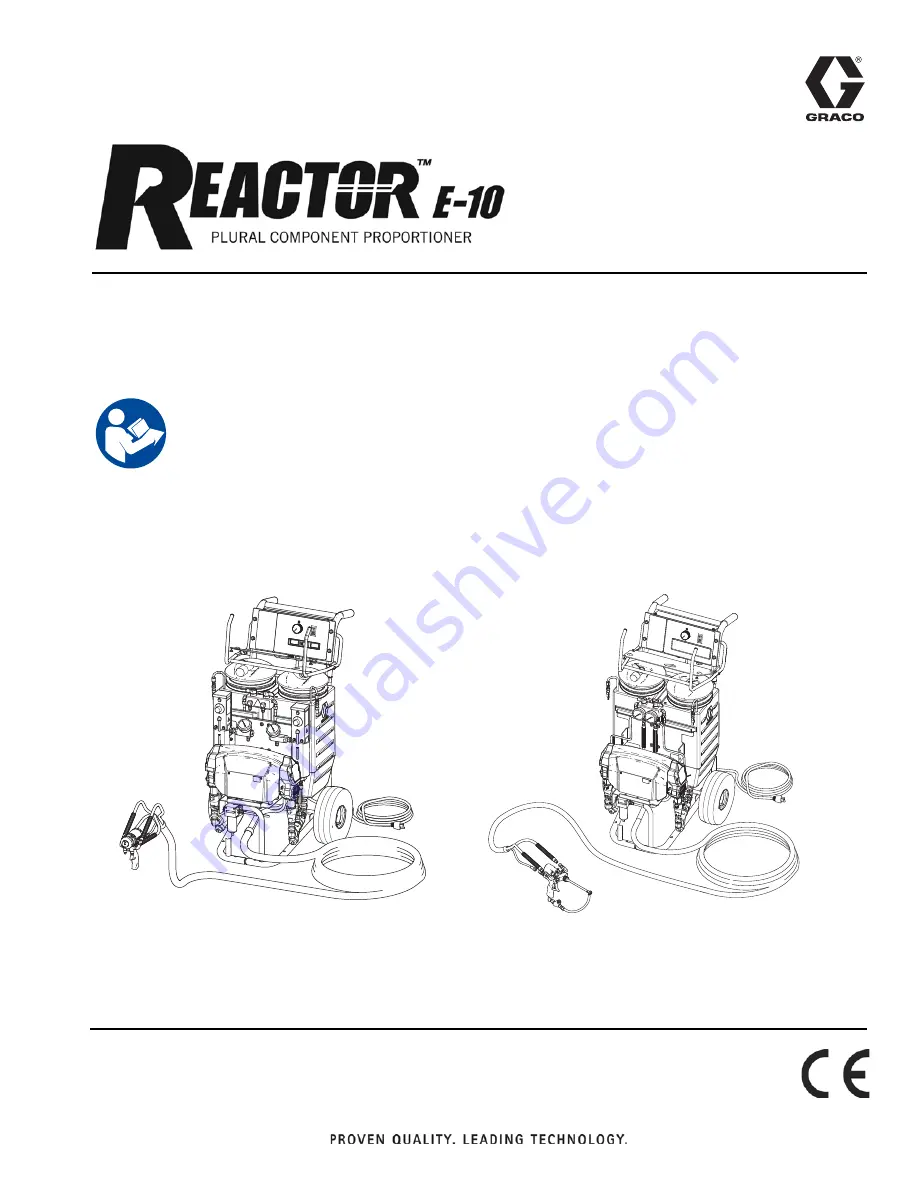
Instructions - Parts List
For spraying or dispensing 1:1 mix ratio materials, including epoxies, polyurethane
foam, polyurea coatings, and joint fill materials. For professional use only.
Not approved for use in European explosive atmosphere locations.
See page 4 for a list of models and maximum working pressures.
Important Safety Instructions
Read all warnings and instructions in this manual
before using the equipment. Save these
instructions.
WLD
WLD
Nonheated Package, MD2 Cold Spray
Gun
Heated Package, with Fusion
™
Gun
311075ZAB
EN