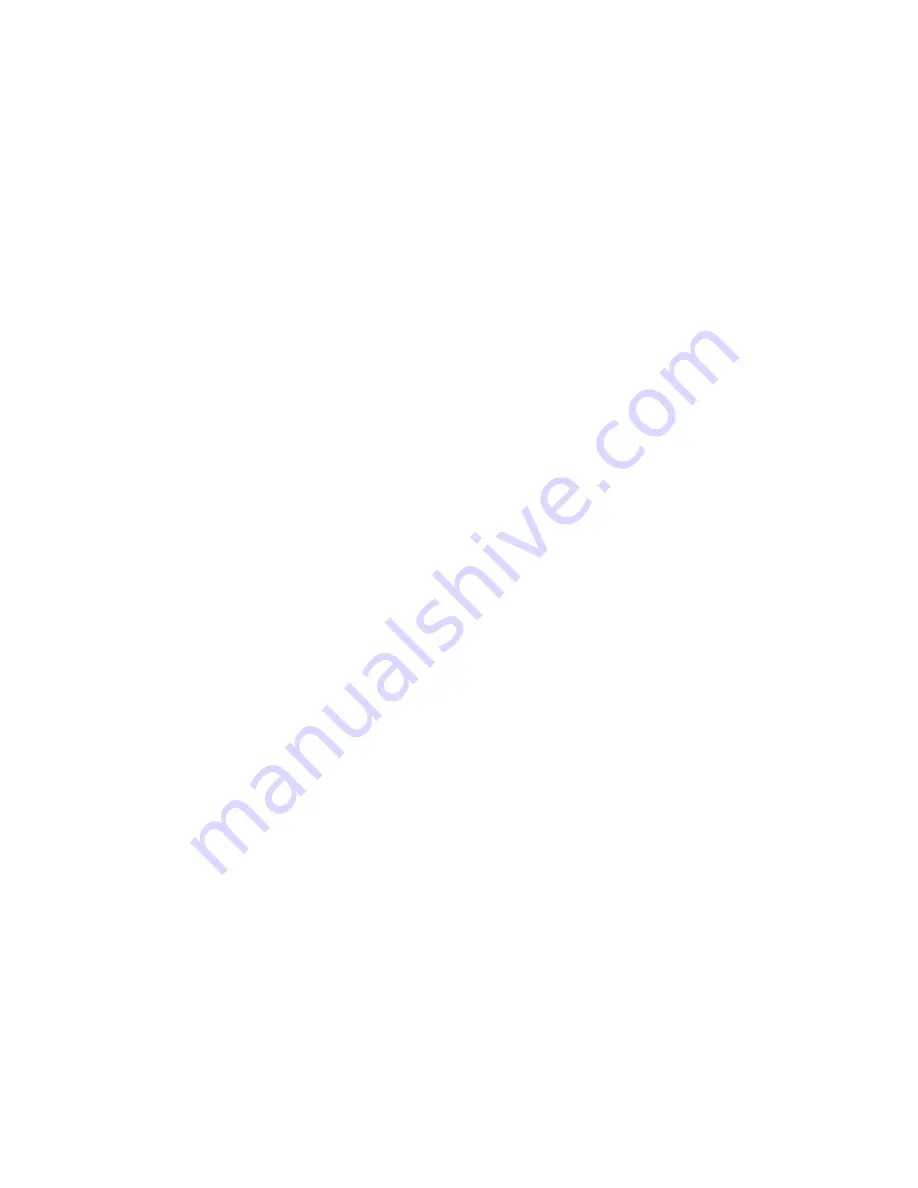
20
309828
Packings
Disassembly
1. To access water seals for inspection or replace-
ment, remove head of pump.
Note:
It is important to note the order in which the
components of the packing stack are arranged and
facing during disassembly.
2. Remove head bolts.
3. Insert a small pry bar between head and body at
opposite corners and apply pressure down on one
pry bar and up on the other pry bar.
4. Lift head up and away from body.
Note:
Packing stack will not always stay in head of
pump when it is removed. Sometimes one or more
components of the packing stack will come out of the
head and stay on the plunger.
5. To remove any components that stay on plungers
twist back and forth while pulling up.
6. Remove low–pressure seals by inserting a flat
screwdriver under seal lip and lifting up.
7. Remove piston guides from head by using a re-
verse pliers (preferably rubber coated) inserted
into center of piston guide.
8. Use back and forth twisting motion while pulling up
(clockwise and counter–clockwise).
9. Another method is to use a two–prong slide ham-
mer puller. Insert prongs into piston guide allowing
prongs to grab under support ring, then use slide
hammer to pull packing stack up and out of head.
Note:
Damage to piston guides and or seals may
occur during removal. Inspect carefully before reusing
any components of packing stack.
10. Remove high–pressure packing by pulling straight
out with your finger.
Assembly
1. Install high–pressure seal into head.
Note:
It should fit snugly. The packing support is part
of the valve cage.
2. Place high–pressure seal at an angle and work it
into cylinder.
Note:
The point of the “v” or flat side of packing is
pointed at you.
3. Lubricate packing retainer o–ring with a light film of
oil and install it into cylinder.
4. Push it completely into place.
Note:
O–ring will seat just inside manifold and you will
hear a slight pop.
5. Insert low–pressure seal by placing it into cylinder
at an angle and pushing it into place.
6. Put a thin coat of oil on plungers and packings.
7. Carefully install manifold and torque bolt to 443
in.–lbs (37 ft–lbs).
Note:
Valve life is dependant on many variables.
Hard water, cavitation, corrosion, chemicals and
equipment care. The valves are a wear item and need
periodic replacement. Worn o–rings or damaged
valves will cause pressure loss and pulsations.
Water seals are wear items. Lift of seals is dependent
on many factors. Water seals should be replaced
when water leak or loss of performance is noticed.
Prompt replacement of worn seals will insure peak
operating performance and trouble–free operation.