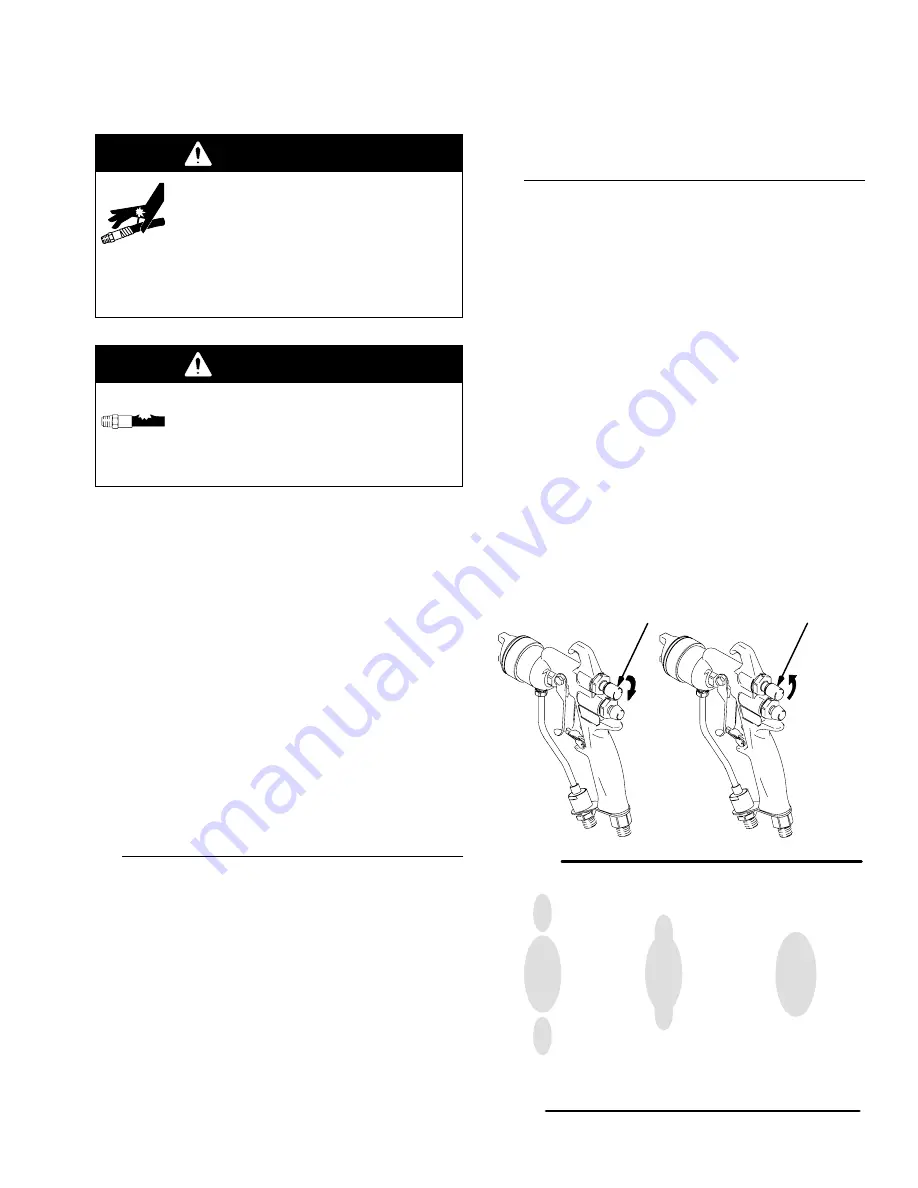
308993 11
Operation
Adjust the Spray Pattern
WARNING
INJECTION HAZARD
To reduce the risk of component rupture
and serious injury, including injection, do
not exceed the gun’s maximum fluid
working pressure of 1500 psi (10 MPa, 105 bar) or
the maximum working pressure of the lowest rated
component in the system.
WARNING
COMPONENT RUPTURE HAZARD
Do not exceed the
maximum fluid and
air pressure
of this gun. Higher pressur-
es can cause parts to rupture and result in serious
injury.
1.
Do not turn on the air supply yet. Set the fluid
pressure at a low starting pressure. For low vis-
cosity fluids (less than 25 sec, #2 Zahn cup) with
lower percent solids (typically less than 40%), start
at 300 psi (2.1 MPa, 21 bar) at the pump outlet.
For fluids with higher viscosity or higher solids
content, start at 600 psi (4.2 MPa, 42 bar). If a
fluid pressure regulator is installed, use it to make
the adjustments.
If your system does not have a fluid regulator,
such as a Falcon I or Falcon II package, the fluid
pressure is controlled by the air regulator supplying
the pump. See the example below.
Example:
Pump Ratio
x
Pump Air Regulator
Setting
=
Fluid
Pressure
Falcon I
(10:1 ratio)
x
30 psi (0.21 MPa,
2.1 bar)
=
300 psi
(2.1 MPa,
21 bar)
Falcon II
(20:1 ratio)
x
30 psi (0.21 MPa,
2.1 bar)
=
600 psi
(4.2 MPa,
42 bar)
2.
Trigger the gun to check the atomization; do not be
concerned about the pattern shape yet.
3.
Increase the fluid pressure in 100 psi (0.7 MPa, 7
bar) increments, just to the point where a further
increase in fluid pressure does not significantly
improve fluid atomization. See the example below.
Example:
Pump
Ratio
x
Pump Air Regulator
Setting (increments)
=
Fluid
Pressure
(increments)
Falcon I
(10:1
ratio)
x
10 psi (0.07 MPa,
0.7 bar)
=
100 psi
(0.7 MPa,
7 bar)
Falcon II
(20:1
ratio)
x
5 psi (0.035 MPa,
0.35 bar)
=
100 psi
(0.7 MPa,
7 bar)
4.
Close off the pattern adjustment air by turning the
knob (S, see Fig. 5) clockwise (in) all the way. This
sets the gun for its widest pattern.
5.
Set the atomizing air pressure at about 5 psi (0.35
bar, 35 kPa) when triggered. Check the spray
pattern, then slowly increase the air pressure until
the tails are completely atomized and pulled into
the spray pattern. See Fig. 6. Do not exceed 100
psi (0.7 MPa, 7 bar) air pressure to the gun.
For a narrower pattern,
turn the pattern adjustment
valve knob (S, see Fig. 5) counterclockwise (out).
If the pattern is still not narrow enough, increase
the air pressure to the gun slightly or use a differ-
ent size tip.
ÎÎ
ÎÎ
ÎÎ
ÎÎÎ
ÎÎÎ
ÎÎÎ
ÎÎ
ÎÎ
ÎÎ
ÎÎÎ
ÎÎÎ
ÎÎÎ
9131A
Fig. 5
S
Out
(narrower
pattern)
In
(wider
pattern)
S
No Air
Too Little Air
Right Amount
of Air
Fig. 6
0792
Summary of Contents for 241508
Page 4: ...4 308993 Notes...