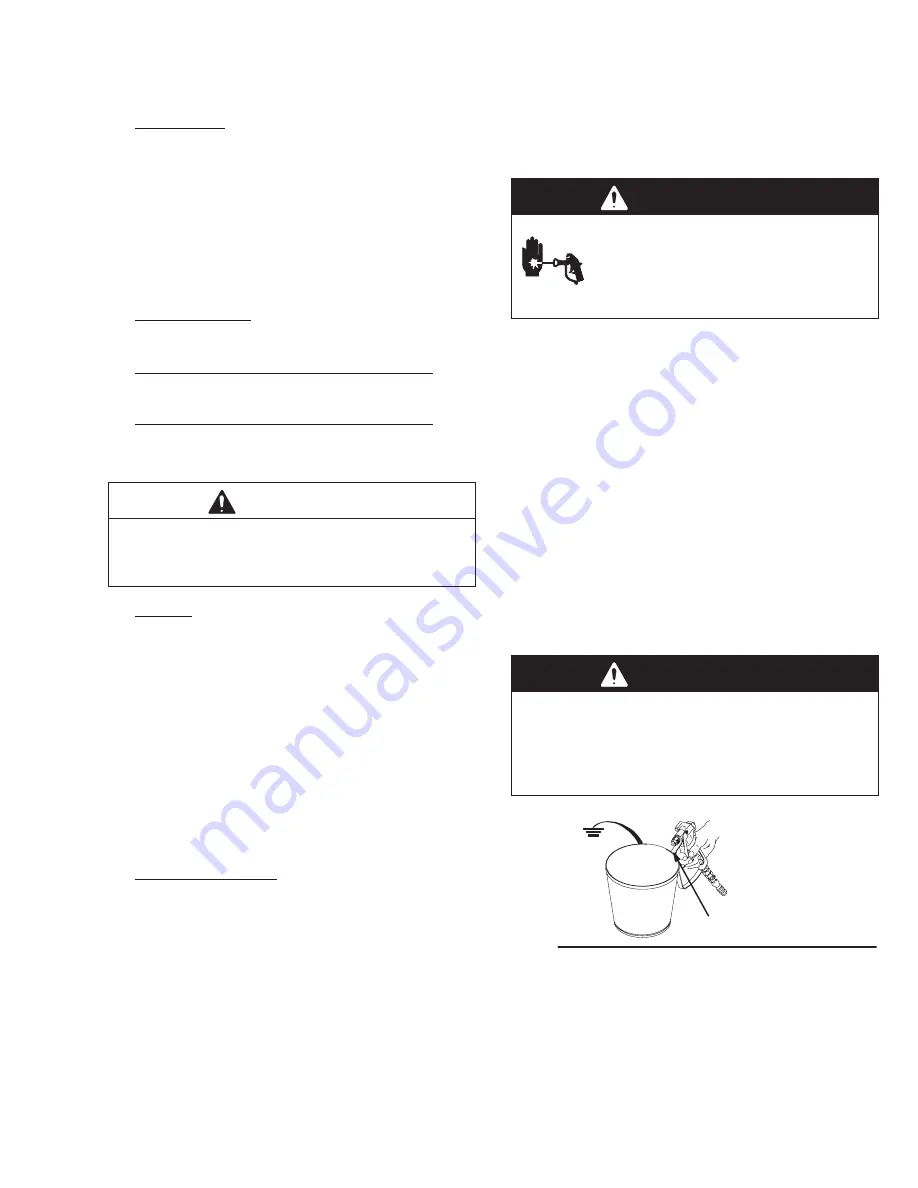
308398
11
Flushing
When to Flush
1.
New Sprayer. This sprayer was factory tested in
lightweight oil,which was left in to protect the pump
parts.
Before using water–base paint,
flush with mineral
spirits, followed by a soapy water flush, and then a
clean water flush.
Before using oil–base paint,
flush with mineral
spirits.
2.
Changing Colors. Flush with a compatible solvent
such as mineral spirits or water.
3.
Changing from water–base to oil–base paint.
Flush
with warm, soapy water, then mineral spirits.
4.
Changing from oil–base to water–base paint.
Flush
with mineral spirits, followed by warm, soapy
water, and then a clean water flush.
CAUTION
To prevent pump corrosion, never leave water or
any type of paint in the sprayer when it is not in use.
Pump the water or the paint out with mineral spirits.
5.
Storage.
Water base paint:
flush with water, then mineral
spirits and leave the pump, hose and gun filled
with mineral spirits. Shut off the sprayer, remove
the spark plug cable, and open the pressure drain
valve to Relieve the pressure. Leave the drain
valve open.
Oil base paint:
flush with mineral spirits and leave
the pump, hose and gun filled with mineral spirits.
Shut off the sprayer, remove the spark plug cable,
and open the pressure drain valve to relieve the
pressure. Leave the drain valve open.
6.
Startup after storage.
Before using water–base paint
, flush out the
mineral spirits with soapy water, and then with
clean water.
When using oil–based paint,
flush out the mineral
spirits with the paint to be sprayed.
How to Flush
WARNING
INJECTION HAZARD
To reduce the risk of serious injury,
whenever you are instructed to relieve
pressure, follow the
Pressure Relief
Procedure
on page 10.
NOTE:
The word solvent refers to water or oil-based
solvent.
1.
Relieve pressure.
2.
Remove the filter bowl (A) and screen (B); see
instruction manual 307273, supplied. Install the
bowl and support (C), without the screen, to flush.
Clean the screen separately. See Fig. 5.
3.
Close the pressure drain valve.
4.
Put the suction tube in a grounded pail of solvent.
5.
Remove the spray tip from the gun(s).
WARNING
To reduce the risk of static sparking and splashing
when flushing, always remove the spray tip from
the gun, and hold a metal part of the gun firmly to
the side of, and aimed into, a grounded metal pail.
See Ref. A in Fig. 4.
Fig. 4
01024
A