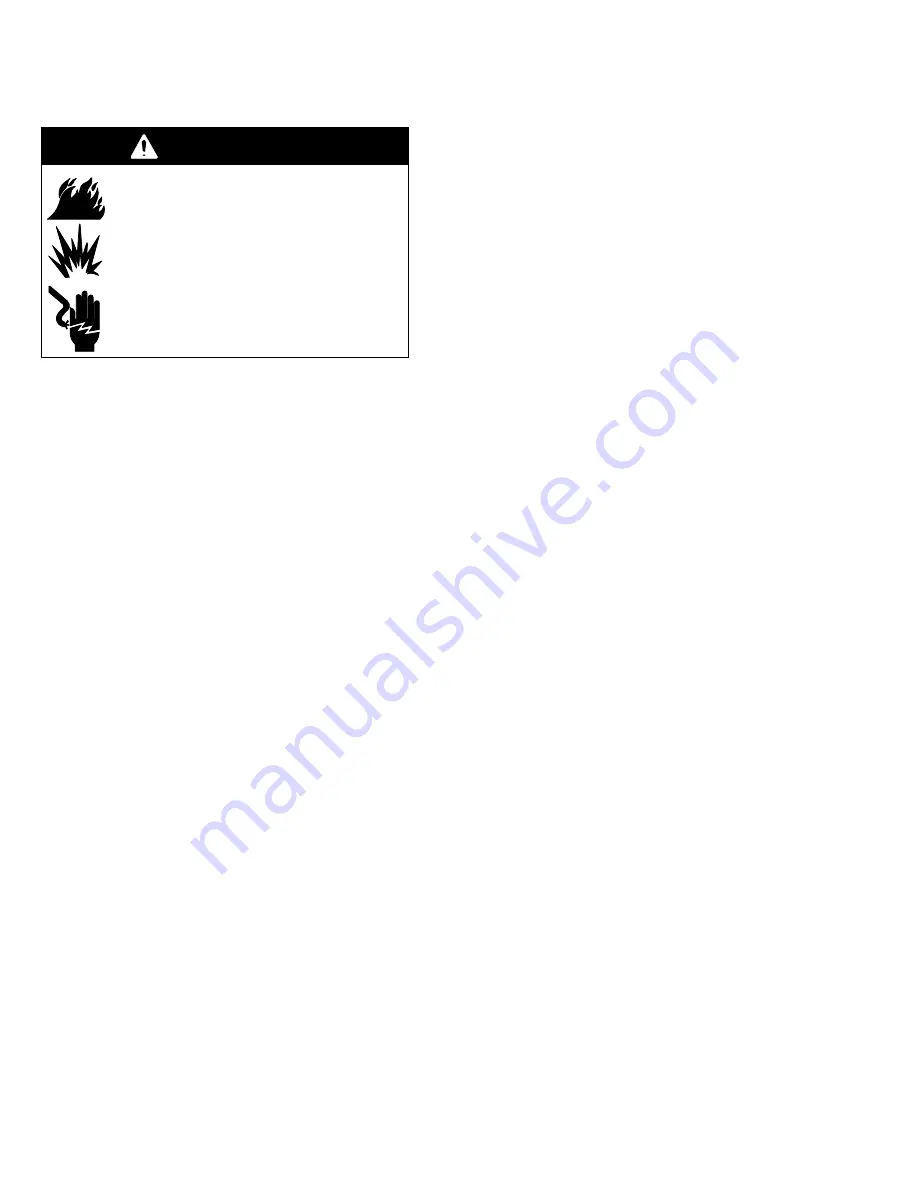
8 307912
Installation
Ground the System
WARNING
FIRE, EXPLOSION, AND
ELECTRIC SHOCK HAZARD
When operating the electrostatic device,
any ungrounded objects in the spray
area (such as people, containers, tools,
etc.) can become electrically charged.
Improper grounding can result in static
sparking, which can cause a fire, explo-
sion, or electric shock. Follow the
grounding instructions below.
The following are minimum grounding requirements for
a basic electrostatic system. Your system may include
other equipment or objects which must be grounded.
Check your local electrical code for detailed grounding
instructions. Your system must be connected to a true
earth ground.
1.
Pump: ground the pump by connecting a ground
wire and clamp as described in your separate
pump instruction manual.
2.
Air compressors and hydraulic power supplies:
ground the equipment according to the manufac-
turer’s recommendations.
3.
Electrostatic Air Spray Gun: ground the gun by
connecting the Graco Electrically Conductive Air
Hose and connecting the air hose ground wire to a
true earth ground. Check the electrical grounding
of the gun as instructed on page 9.
4.
All air and fluid lines must be properly grounded.
Use only grounded hoses with a maximum of 500
feet (150 m) combined hose length to ensure
grounding continuity.
5.
All electric cables must be properly grounded.
6.
All persons entering the spray area: their shoes
must have conductive soles, such as leather, or
personal grounding straps must be worn. Rubber
or plastic soles are not conductive. The operator
must not wear gloves that insulate the hand from
the spray gun. The gloves must be conductive or
modified as shown in Fig. 3, page 11.
7.
Object being sprayed: keep the workpiece hangers
clean and grounded at all times. Contact points
must be sharp points or like knife edges.
8.
The floor of the spray area: must be electrically
conductive and grounded. Do not cover the floor
with cardboard or any non-conductive material
which would interrupt grounding continuity.
9.
Flammable liquids in the spray area: must be kept
in approved, grounded containers. Do not store
more than the quantity needed for one shift.
10. All electrically conductive objects or devices in the
spray area: including fluid containers and wash
cans, must be properly grounded.
Summary of Contents for 222300
Page 10: ...10 307912 Notes...
Page 33: ...307912 33 Notes...