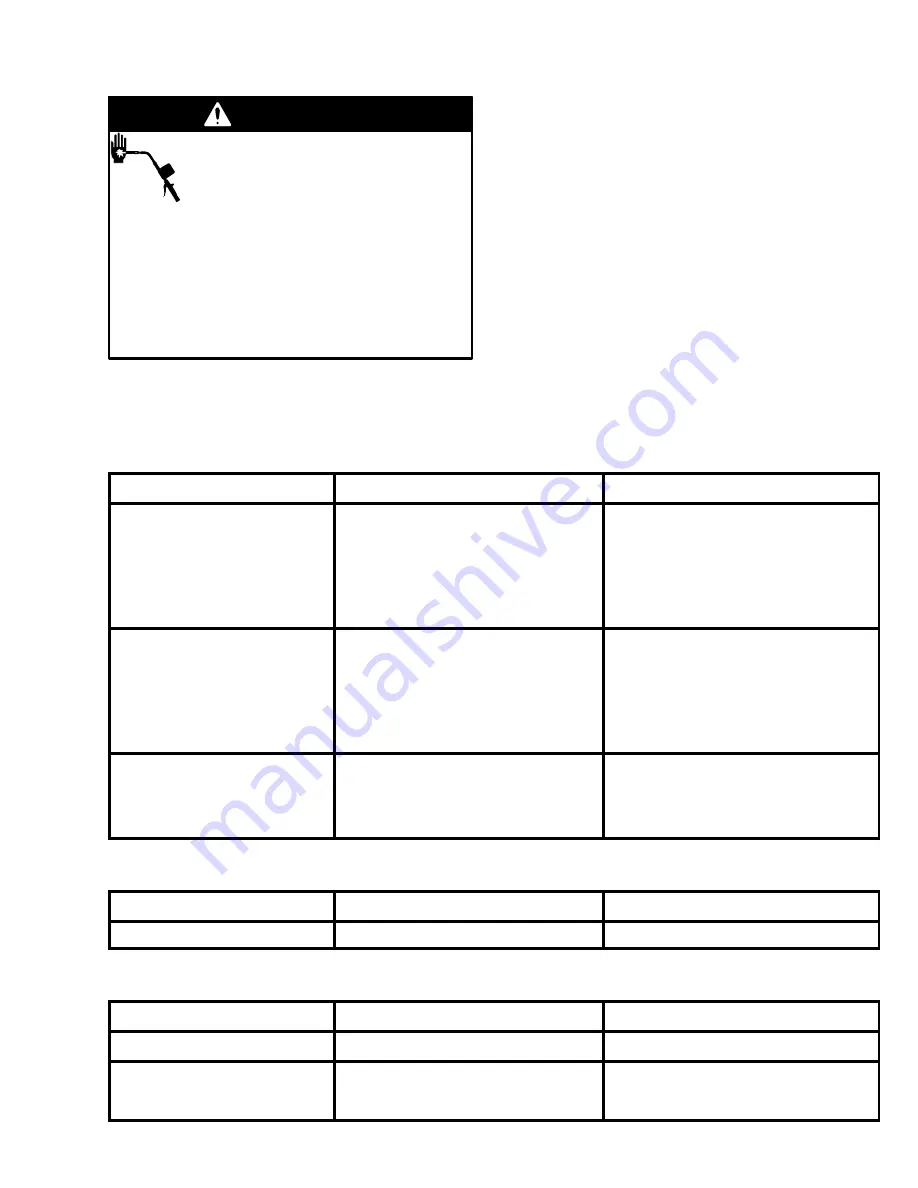
Troubleshooting
PRESSURIZED EQUIPMENT HAZARD
The equipment stays pressurized until
pressure is manually relieved. To
reduce the risk of serious injury from
pressurized fluid, accidental spray from the
dispenser or splashing fluid, follow the Pressure
Relief Procedure whenever you:
Are instructed to relieve pressure
Stop dispensing
Check, clean, or service any system equipment
Install or clean fluid nozzles
WARNING
Pressure Relief Procedure
1.
Turn off the power supply to the pump.
2.
Trigger the valve into a waste container to relieve
pressure.
3.
Open any bleed-type master air valves and fluid
drain valves in the system.
4.
Leave the drain valve open until you have com-
pleted repairs and are ready to pressurize the sys-
tem.
Electronic Meter
NOTE: Before you check or repair the meter, be sure all other valves, controls, and the pump are operating
properly.
Problem
Cause
Solution
Digital display does not
activate.
Electronic control is malfunctioning.
Replace the electronic control.
Order Part No. 235–878
for gallons/quarts/pints.
Order Part No. 235–901
for liters.
There is no fluid flow.
Metering unit is malfunctioning.
Replace the metering unit.
Order Part No. 235–873
for gallons/quarts/pints.
Order Part No. 235–904
for liters.
Digital display is dim.
Battery in electronic control is worn.
Replace the electronic control within
approximately one week of when you
notice the dimness.
See the part numbers above.
Dispensing Valve
Problem
Cause
Solution
There is no fluid flow.
Strainer is clogged.
Remove and clean strainer.
Mechanical Meter
Problem
Cause
Solution
There is no fluid flow.
Strainer is clogged.
Remove and clean strainer.
Meter does not register.
Loose cap or dirt in chamber.
Screw cap on tightly with o-ring in
proper position, or clean and
inspect meter.
Summary of Contents for 222-411
Page 15: ...307 995 15 Notes...