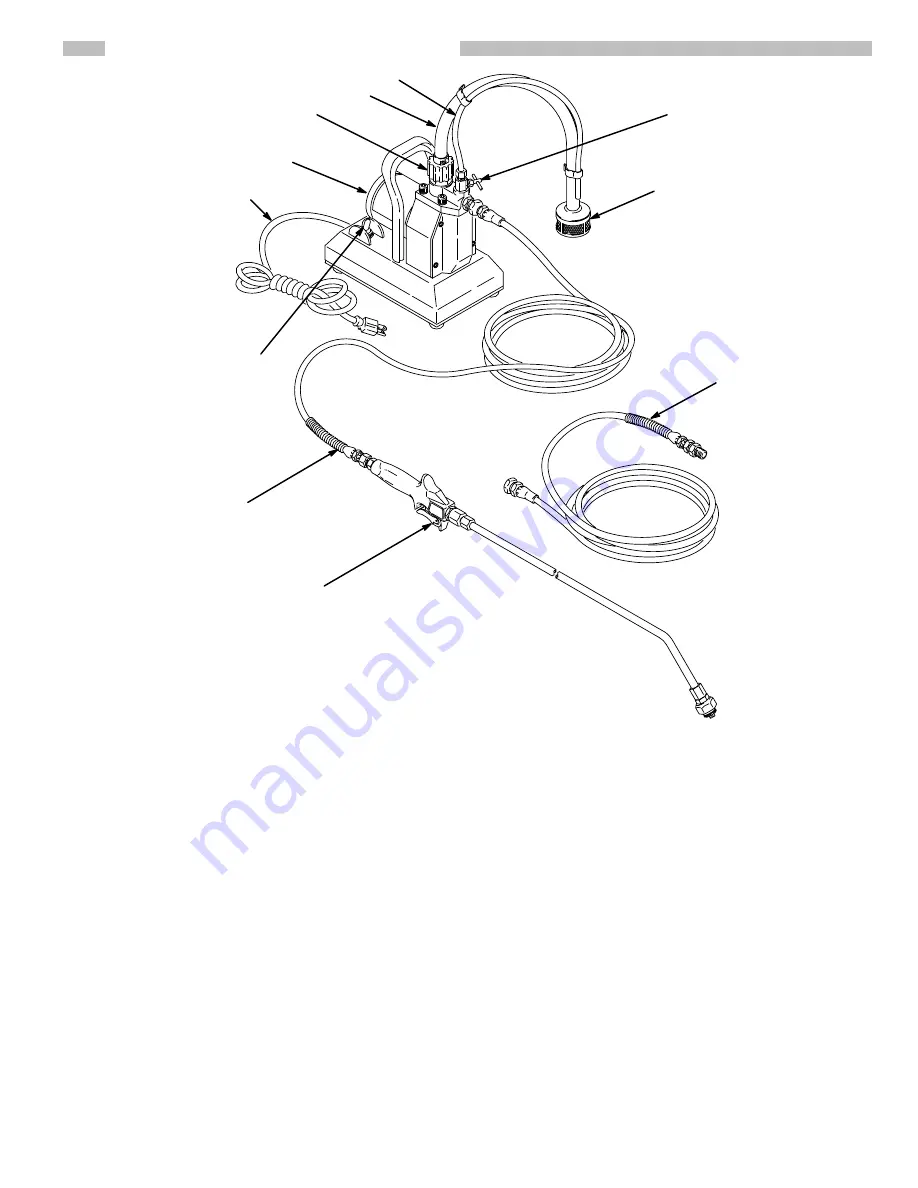
5
307-922
MINI-WETTER SYSTEM DESCRIPTION
SUCTION HOSE
PRIMING TUBE
INLET VALVE
MOTOR
ON/OFF SWITCH
POWER SUPPLY CORD
PRIMING VALVE
50 FT. (15 M) HOSE
SPRAY WAND
STRAINER
50 FT. (15 M) HOSE
0335
0285
Motor
The motor drives the connecting rod which moves the
diaphragm.
Pressure Switch
The pressure switch at the pump outlet turns the motor
on and off to control material pressure.
Diaphragm
The diaphragm is the heart of the pump. Driven by the
connecting rod and motor , the movement of the dia-
phragm draws material through the suction hose and to
the outlet valve.
Priming Valve
The priming valve assists in priming the pump during
startup. Turning the priming valve
counterclockwise
causes the material to drain directly back into the pail
through the priming tube. T urning the knob
clockwise
causes the to flow through the fluid outlet valve and to
the hose and spray valve.
Outlet Valve
The outlet valve has a ball check which prevents material
from flowing backwards into the pump. This helps keep
an even supply of material to the roller each time you trig-
ger the spray valve.
Inlet Valve
As the diaphragm draws material from the suction tube,
the material passes through the inlet valve which opens
to allow material into the pump.
Outlet Hose
The hoses have swivel-type couplings for easy assem-
bly. A larger diameter outlet hose and chemical-resistant
outlet and suction hoses are available. See ACCESSO-
RIES on page 19.
Spray Valve
The spray valve controls material flow by triggering it on
and off.
Summary of Contents for 222-340
Page 9: ...9 307 922 NOTES...