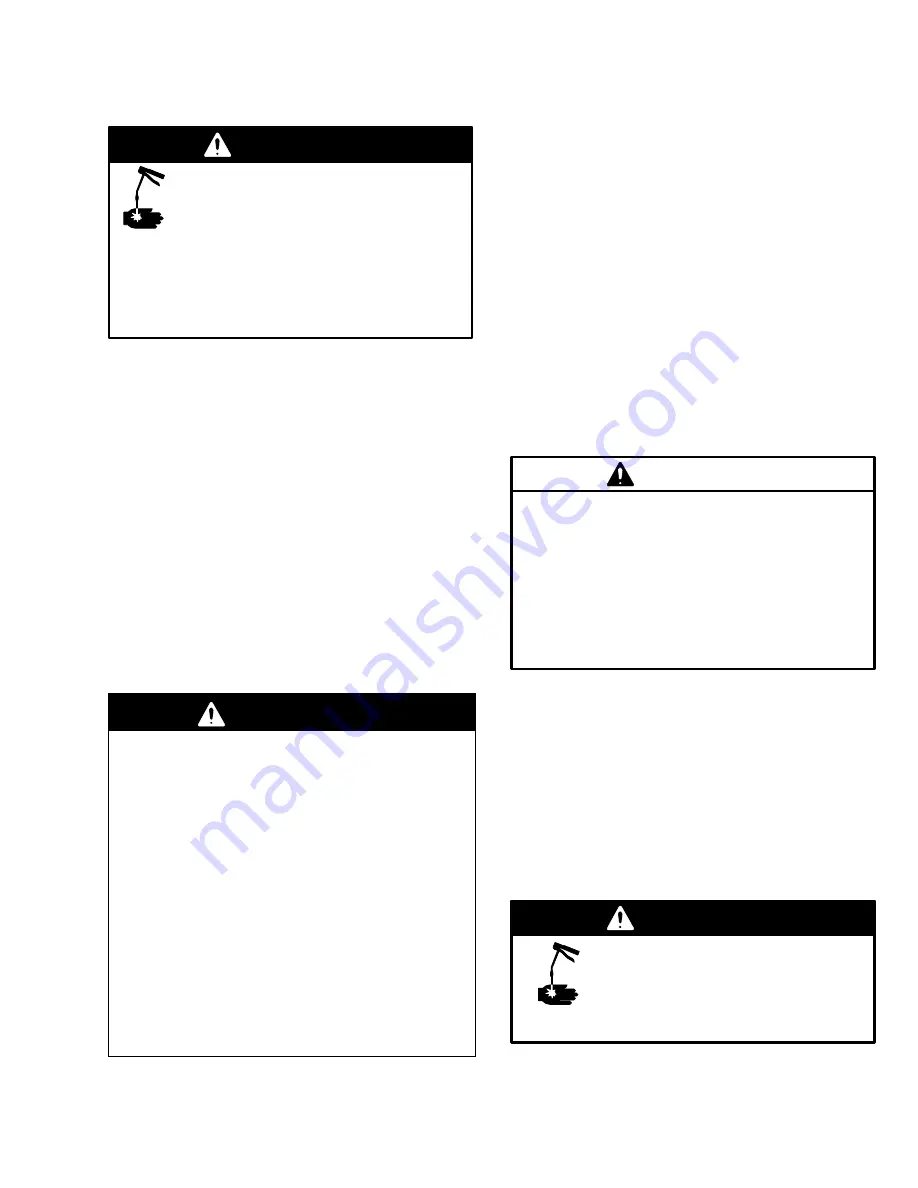
307882 7
Operation
Pressure Relief Procedure
INJECTION HAZARD
To reduce the risk of serious bodily
injury, including fluid injection, injury from
moving parts, or splashing in the eyes or
on the skin, always follow this procedure whenever
you shut off the pump, when checking or servicing
any part of the system, when installing or changing
dispensing devices, and whenever you stop dis-
pensing.
WARNING
1.
Close the pump air regulator.
2.
Close the pump’s bleed-type master air valve (re-
quired in the system).
3.
Hold a metal part of the gun or valve firmly to a
grounded metal waste container and trigger to re-
lieve the fluid pressure.
If you suspect that the dispensing valve is clogged, or
that pressure has not been fully relieved after following
the steps above,
very slowly
loosen the dispensing
valve coupler or hose end coupling to relieve pressure
gradually, then loosen completely. Then clear the clog.
Startup – Single or Multiple Pump Systems
1.
Close the air regulators and bleed-type master air
valves to all but one pump.
2.
Open the master air valve from the compressor.
WARNING
The maximum working pressure of each pump in
your system may not be the same. To reduce the risk
of overpressurizing any part of your system, be sure
you know the maximum working pressure rating of
each pump and its connected components. Never
exceed the maximum working pressure of the lowest
rated component connected to a particular pump.
To determine the fluid output pressure using the air
regulator reading, multiply the ratio of the pump by
the air pressure shown on the regulator gauge. For
example:
10 (:1) ratio x 100 psi air =
1000 psi fluid output
[10:(1) ratio x 7 bar air = 70 bar fluid output]
Limit the air to the pump so that no air line or fluid line
component or accessory is overpressurized.
3.
For the pump which is connected, trigger the dis-
pensing valve into a grounded metal waste con-
tainer, making firm metal-to-metal contact between
the container and valve. Open the bleed-type master
air valve and open the pump air regulator slowly, just
until the pump is running. When the pump is primed
and all air has been pushed out of the lines, release
the trigger.
4.
If you have more than one pump, repeat this proce-
dure for each pump.
NOTE:
When the pump is primed, and with sufficient air
supplied, the pump starts when the dispensing valve is
opened and shuts off when it is closed.
5.
Set the air pressure to each pump at the lowest pres-
sure needed to get the desired results. Use the regu-
lator to adjust pump speed and pressure.
Never allow the pump to run dry of the fluid
being pumped. A dry pump quickly accelerates
to a high speed and could possibly damage
itself. If the pump accelerates quickly, stop it
immediately, and check the fluid supply. If the
supply container is empty and air has been
pumped into the lines, prime the pump and lines
with fluid, or flush it and leave it filled with a
compatible solvent. Be sure to eliminate all air
from the fluid system.
CAUTION
NOTE:
A pump runaway valve (E) can be installed on the
air line to automatically shut off the pump if it starts to run
too fast.
7.
Read and follow the instructions supplied with each
component in your system.
8.
To shut off system, always
relieve the pressure
.
INJECTION HAZARD
To reduce the risk of serious injury
whenever you are instructed to relieve
pressure, always follow the
Pressure
Relief Procedure
at left.
WARNING
Summary of Contents for 220170
Page 11: ...307882 11 Notes...