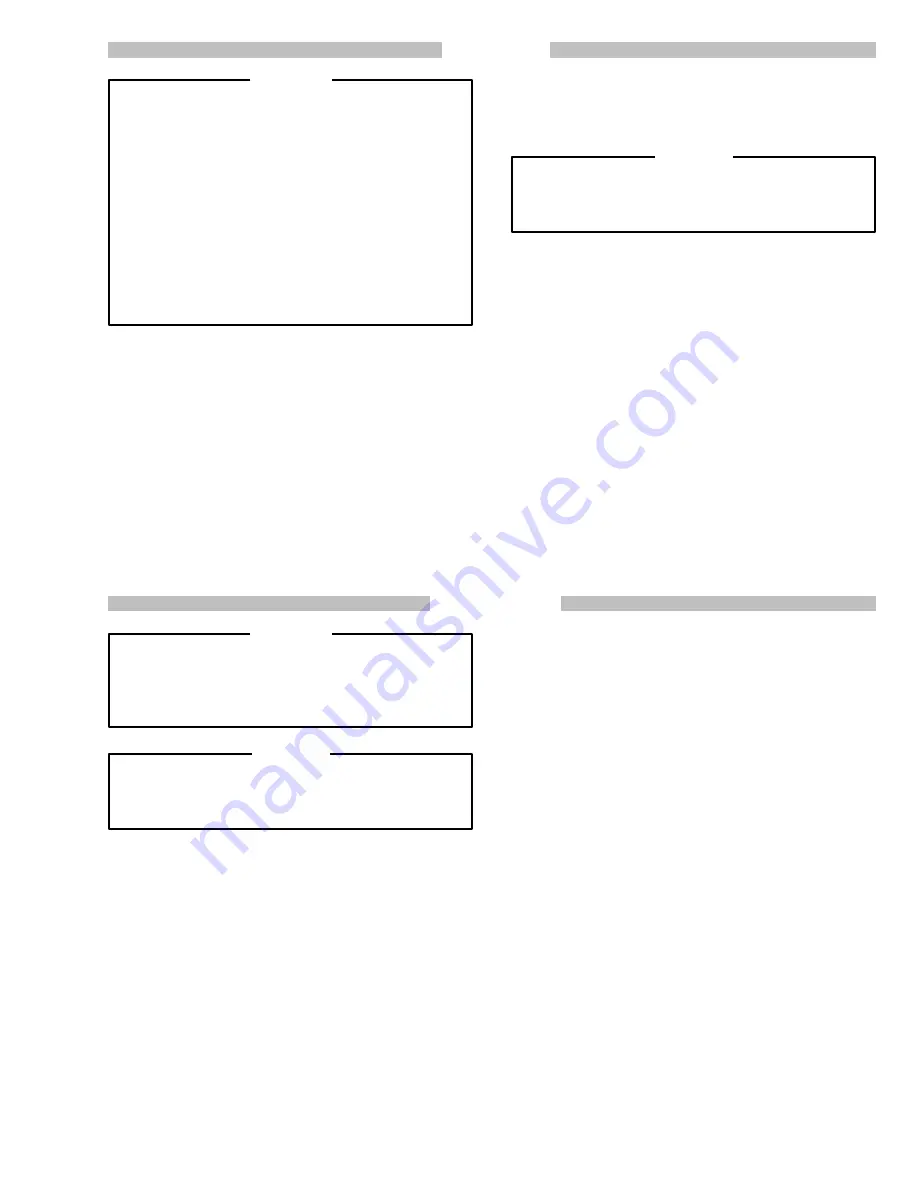
7
307-730
STARTUP
Pressure Relief Procedure
To reduce the risk of serious bodily injury, including
injury from moving parts, or electric shock, always
follow this procedure whenever you shut off the sys-
tem, when checking or servicing any part of the sys-
tem and whenever you stop painting.
1. Turn the ON/OFF switch to OFF.
2. Unplug the power supply cord.
3. Trigger the roller valve to relieve pressure.
If you suspect that pressure is not fully relieved after
following the steps above, open the priming valve 2
turns counterclockwise.
WARNING
1. Place the suction hose in the pail of paint.
2. Plug in the sprayer.
3. Open the priming valve 2 turns
counterclockwise.
4. Turn the ON/OFF switch ON.
5. You can see the paint being drawn into the suction
hose (if the hose is clean). As soon as you see paint
flow through the priming tube, close the priming
valve. This usually takes less than 30 seconds.
CAUTION
Failure to completely close the priming valve after
the system is primed will cause the valve to erode,
greatly shortening the valve life.
NOTE:
If your system is hard to prime, first try to force
feed the suction tube. Hold the suction tube in a
vertical position and pour paint into it. Turn on the
system. If the system does not prime within one
minute, shut it of f. Heavy viscosity paint may
need to be thinned. Be sure to follow the paint
manufacturer’s recommendations on thinning.
6. Trigger the roller valve to prime the outlet hose and
extension. Once primed, the motor will run when
there is paint demand, but appears to shut itself of f
when there is no paint demand.
NOTE:
An occasional start and stop of the motor when
the roller valve is not triggered is normal.
OPERATION
WARNING
To reduce the risk of electric shock, do not expose
the system to rain. Always store the system indoors.
Do not operate the pump with the base cover
removed.
CAUTION
Always allow cold equipment to warm to room tem-
perature before using it to prevent damaging the
system.
1. With the system fully primed, trigger the roller valve
briefly until paint comes to the roller.
2. Experiment with triggering and rolling the paint until
you determine just how often you need to trigger the
roller valve to keep an even flow of paint to the roller.
3. Whenever you stop painting, turn the ON/OFF
switch to OFF, and trigger the roller valve. Then ele-
vate the roller end of the extension to prevent paint
from draining out the roller end.
4. Thoroughly flush the system immediately after each
use to keep it in good working order. See page 8.