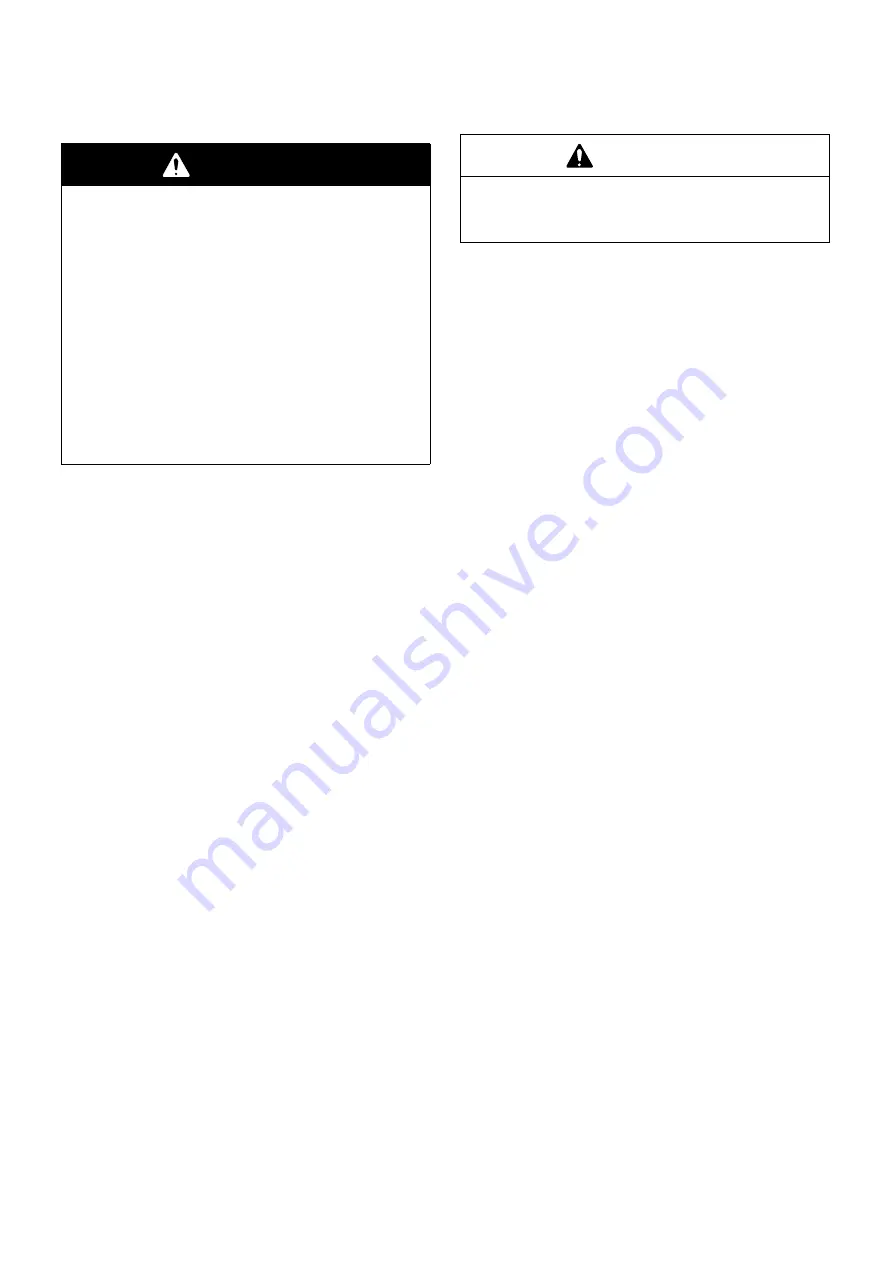
307552
7
Operation
Pressure Relief Procedure
Starting and Operating the Pump
This pump is designed to be used with a Graco Foam-Cat
Sprayer. If you have purchased such a sprayer, complete
warning and operating instructions are contained in the
manual (307541 or 307542) which accompanied the
sprayer. If you have misplaced these manuals, obtain
additional copies by contacting your Graco distributor.
In general operation, when the pump is used for transfer
and supply operations with no dispensing valve, the pump
will run whenever air is supplied.
Normally, the Feed Pump air valve is opened before any
other equipment in the spray system is turned on. This is
so fluid can be supplied to the components immediately.
For shutdown, disconnect the air line coupler (13). See Fig
4.
Never let the pump run when the drum is empty. A dry
pump can quickly accelerate to a high speed and damage
itself. If the pump is running too fast, stop it immediately
and check and refill the material supply, or flush the pump
with a compatible solvent if you stop spraying for the day.
Always prime the entire system with fluid to remove any air
pumped into the system. Refer to Manual 307541 or
307542. Don’t let the material harden in the pump.
Feed Pump Kit
Refer to the operation instructions on page 2 of manual
307548, which was supplied with the Air Dryer, and the
above instructions for operating the Feed Pumps.
Changing Drums
1. Disconnect the hose coupler (N) from the Air Dryer
drum fittings (H). See Fig 3.
2. Leave the ball valve (K) open for a few minutes to
release the air pressure in the drum, then close the
valves.
3. Remove the pump and the drum fittings from the
drum cover and install them in the new drum of
material.
4. Repeat this procedure for the other material.
WARNING
PRESSURIZED EQUIPMENT HAZARD
The system pressure must be manually relieved to
prevent the system from starting or spraying
accidentally. To reduce the risk of an injury from
accidental spray from the gun, splashing fluid, or moving
parts, follow the
Pressure Relief Procedure
whenever
you:
•
are instructed to relieve the pressure,
•
have an air supply interruption,
•
stop spraying,
•
check or service any of the system equipment,
•
or install or clean the spray nozzle.
CAUTION
To avoid crossing material when changing drums,
complete the changing of one type of material before
starting the other.