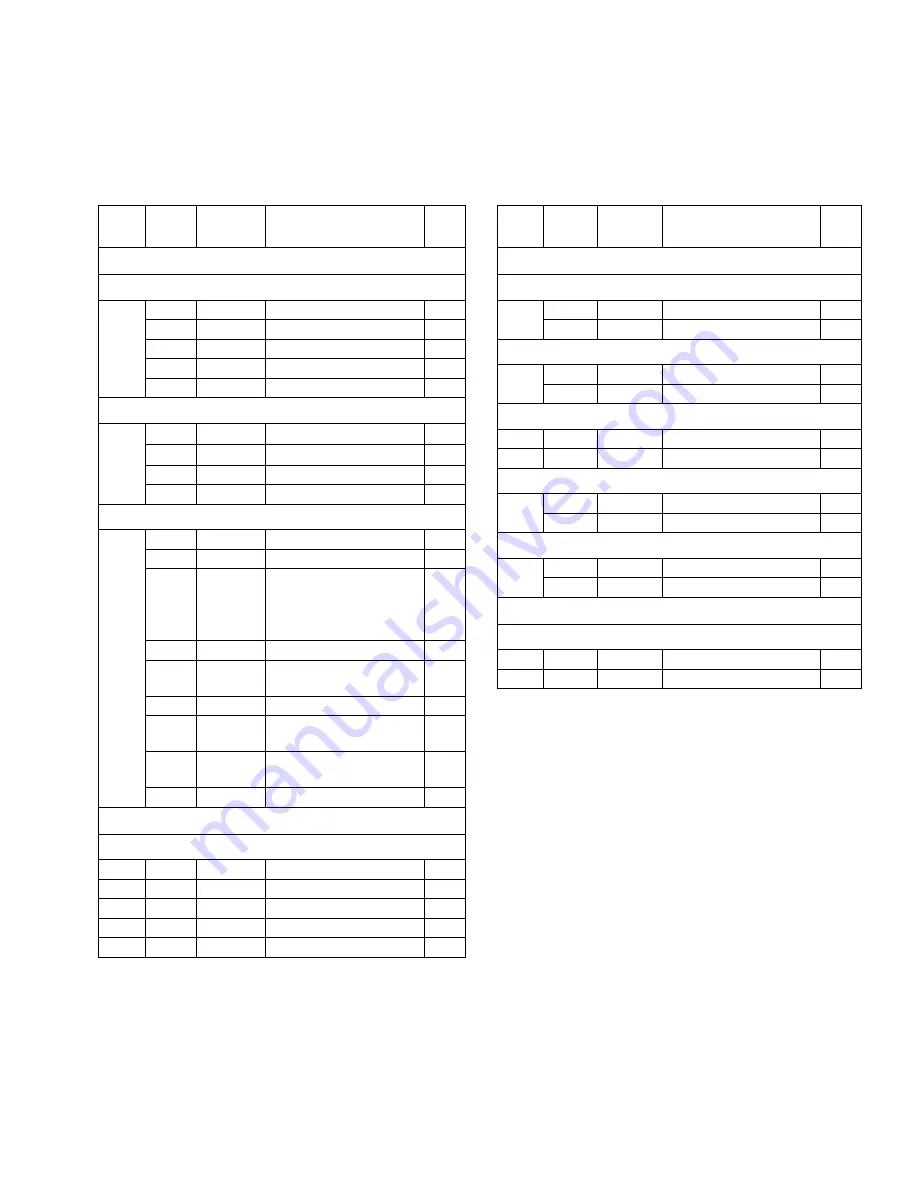
Parts List
310622L
27
Parts List
Pump Configuration Parts List
* Indicates replacement parts.
Inlet and Outlet Parts List
* Indicates replacement parts.
Digit Ref.
No.
Part No. Description
Qty
Model 3150
A
3A Approved Ball Check
132
510490
CLAMP, 4 in.
4
2XB
15H406
SEAT
4
234
249533
COVER, fluid
2
240*
15H460
GASKET, 4 in., EPDM
12
2XA
15H407
STOP, ball
4
B
Ball Check
233
15D026
SEAT
4
234
234530
COVER, fluid
2
240*
15H460
GASKET, 4 in., EPDM
4
242*
15D346
GASKET, ball stop
4
F
Flapper Check
234
234530
COVER, fluid
2
240*
15H460
GASKET, 4 in., EPDM
8
200
249535
MODULE, flapper;
includes items 232,
248, 250, 251, 252,
253
4
232
510490
CLAMP, 4 in.
4
248
15D079
HOUSING, lower
flapper
4
250*
15H460
GASKET, 4 in., EPDM 4
251
15D091
VALVE, flapper,
weldment
4
252
15D090
HOUSING, upper
flapper
4
253*
15K693
RETAINER, flapper
4
Model 1590
3A Approved Ball Check
All
132
15D475
CLAMP, 3 in.
4
All
2XB
15H481
SEAT
4
All
234
249892
COVER, Fluid
2
All
240*
15H459
GASKET, 3 in., EPDM
12
All
2XA
15H482
STOP, Ball
4
Digit Ref.
No.
Part No. Description
Qty
Model 3150
1
1 1/2 x 1 1/2 in. tee
331*
234536
TEE, inlet
1
339*
234536
TEE, outlet
1
2
2 x 2 in. tee
331*
234534
TEE, inlet
1
339*
234534
TEE, outlet
1
3
3 x 3 in. tee
331*
234532
TEE, inlet
1
339*
234532
TEE, outlet
1
4
4 x 4 in. tee
331*
234535
TEE , inlet
1
339*
234535
TEE, outlet
1
5
3 x 2 in. tee
331*
234532
TEE , inlet
1
339*
234534
TEE, outlet
1
Model 1590
2 x 2 in. Tee
All
331*
249893
TEE, Inlet
1
All
339*
249893
TEE, Outlet
1
Summary of Contents for 1590 SA
Page 13: ...Maintenance 310622L 13...
Page 39: ...Model 3150 310622L 39...