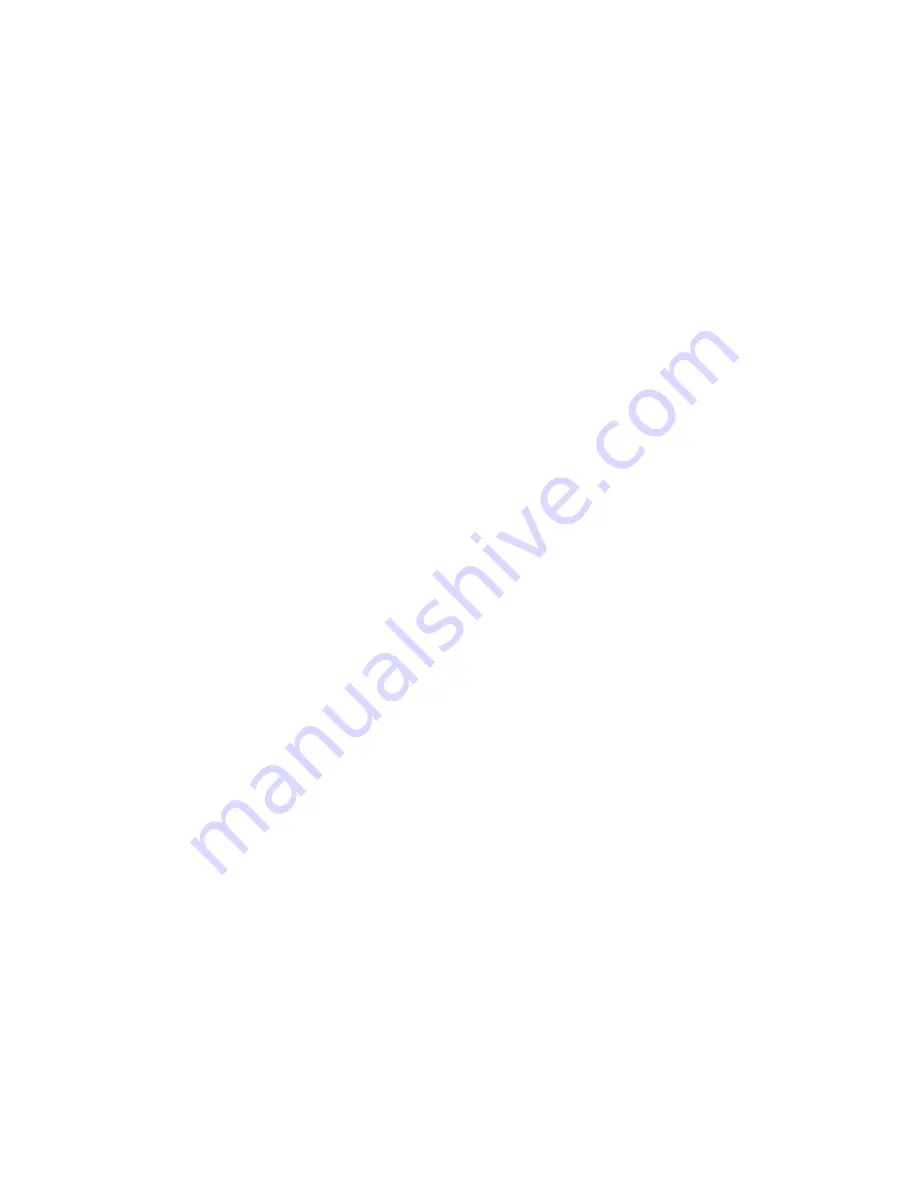
31
New packing should be placed carefully into the
stuffing box. If molded rings are used, the rings should
be opened sideways, and the joints pushed into the
stuffing box first. The rings are installed one at a time,
each ring seated firmly, and the joints staggered so
they are not in line. The joints should be kept toward
the upper side of the shaft and should be at about a
90 degree angle from each preceding joint.
If coil packing is used, cut one ring to accurate size
with either a butt or mitered joint. An accurately cut
butt joint is superior to a poor fitting mitered joint.
Fit the ring over the shaft to assure proper length.
Then remove and cut all other rings to the first
sample. When the rings are placed around the shaft,
a tight joint should be formed. Place the first ring
in the bottom of the stuffing box. Then install each
succeeding ring, staggering the joints as described
above, making sure each ring is firmly seated.
Make sure the seal cage is properly located in the
stuffing box under the sealing water inlet. The function
of the seal cage is to establish a liquid seal around the
shaft, prevent leakage of air through the stuffing box,
and lubricate the packing. If it is not properly located,
it serves no purpose.
Mechanical shaft seals
General
A mechanical shaft seal is supplied in place of a
packed stuffing box where specifically requested.
Mechanical seals are preferred over packing on some
applications because of better sealing qualities and
longer serviceability. Leakage is eliminated when a
seal is properly installed, and normally the life of the
seal is much greater than that of packing on
similar applications.
General instructions for operation of the various
mechanical sealing arrangements are included below.
It is not feasible to include detailed instructions for all
mechanical seals in this booklet because of the almost
unlimited number of possible combinations and
arrangements. Instead, seal manufacturer's
instructions will be included as a separate
supplement to this book where required.
1. Mechanical seals are precision products and
should be treated with care. Use special care
when handling seals. Clean oil and clean parts are
essential to prevent scratching the finely lapped
sealing faces. Even light scratches on these faces
could result in leaky seals.
2. Normally, mechanical seals require no adjustment
or maintenance, except routine replacement of
worn, or broken parts.
3. A mechanical seal which has been used should not
be put back into service until the sealing faces have
been replaced or relapped. (Relapping is generally
economical only in seals two inches in size and
above.)
Four important rules which should always be followed
for optimum seal life are:
1. Keep the seal faces as clean as possible.
2. Keep the seal as cool as possible.
3. Assure that the seal always has proper lubrication.
4. If seal is lubricated with filtered fluid, clean filter
frequently.
Cleaning without dismantling
pump
We recommend that an increasing suction nozzle
or suction diffuser, bolted to the suction flange, be
supplied by Goulds Water Technology. (If this is not
done, a short section of pipe so designed that it can
be readily dropped out of the line can be installed
adjacent to the suction flange.) With this arrangement,
any matter clogging the impeller is accessible by
removing the nozzle (or pipe section).
Other cleaning methods include running an auger
into the pump through the clean out hole in the
suction nozzle, or through the casing handhole. This
should free any clogging in the impeller eye.
If the pump cannot be freed of clogging after the
above methods have been tried, dismantle the unit
as previously described to locate the trouble.