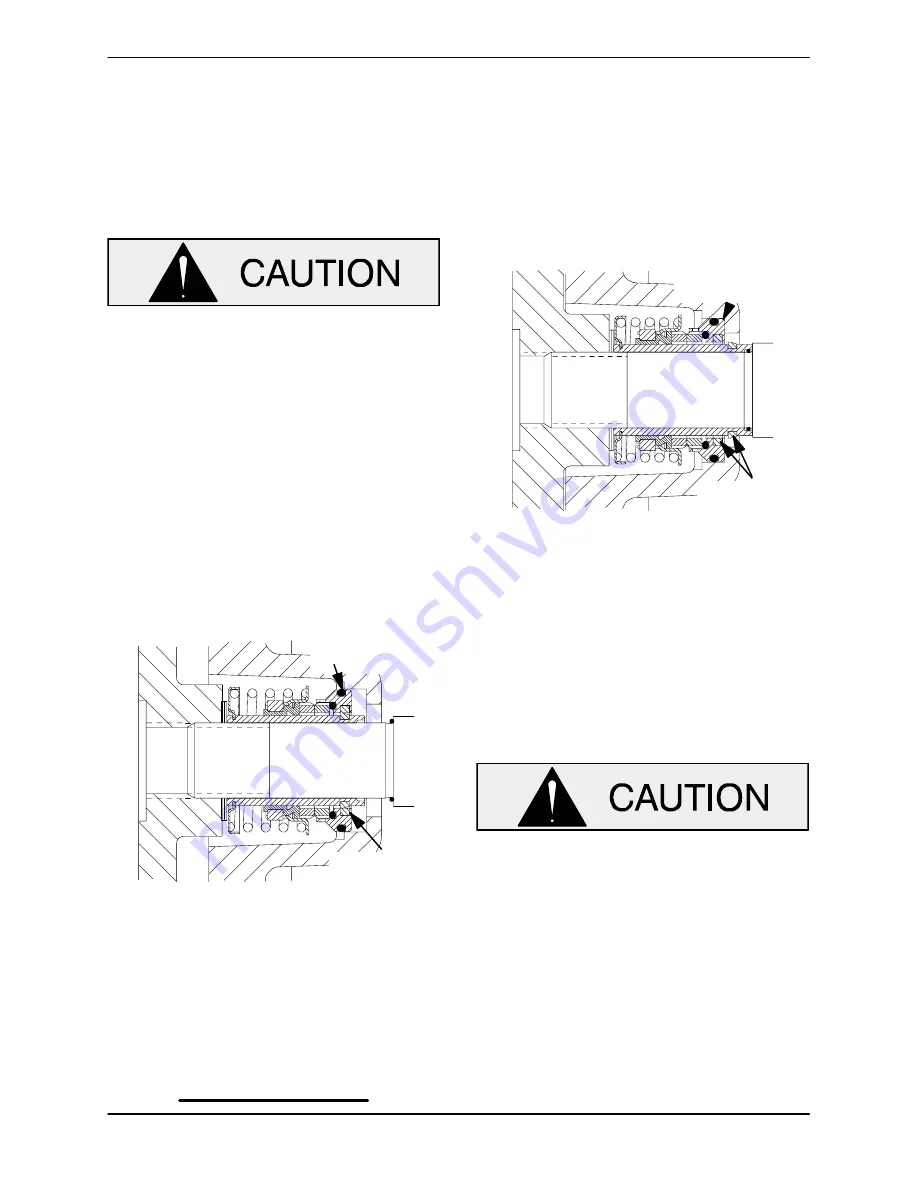
OM--01930--03
T SERIES
MAINTENANCE & REPAIR
PAGE E -- 12
continue to slide the O-ring down the shaft until it
seats against the shaft shoulder.
When installing a new cartridge seal assembly
,
remove the seal from the container, and remove
the mylar storage tabs from between the seal
faces.
New cartridge seal assemblies are
equipped with mylar storage tabs between
the seal faces. These storage tabs
must
be
removed before installing the seal.
Lubricate the external stationary seat O-ring with
light oil. Slide the seal assembly onto the shaft until
the external stationary seat O-ring engages the
bore in the seal plate.
Clean and inspect the impeller as described in
Im-
peller Installation and Adjustment
. Install the full
set of impeller shims (10) provided with the seal,
and screw the impeller onto the shaft until it is
seated against the seal (see Figure 6).
O-RING ENGAGED
WITH SEAL PLATE
BORE
SHEAR RING
(UNSHEARED)
Figure 6. Seal Partially Installed
Continue to screw the impeller onto the shaft. This
will press the stationary seat into the seal plate
bore.
NOTE
A firm resistance will be felt as the impeller presses
the stationary seat into the seal plate bore.
As the stationary seat becomes fully seated, the
seal spring compresses, and the shaft sleeve will
break the nylon shear ring. This allows the sleeve
to slide down the shaft until seated against the
shaft shoulder. Continue to screw the impeller onto
the shaft until the impeller, shims, and sleeve are
fully seated against the shaft shoulder (see Figure
7).
STATIONARY SEAT
FULLY SEATED IN
SEAL PLATE BORE
SHEAR RING
(SHEARED)
Figure 7. Seal Fully Installed
Measure the impeller-to-seal plate clearance, and
remove impeller adjusting shims to obtain the
proper clearance as described in
Impeller Instal-
lation and Adjustment
.
If necessary to reuse an old seal
in an emer-
gency, carefully separate the rotating and station-
ary seal faces from the bellows retainer and sta-
tionary seat.
A new seal assembly should be installed
any time
the old seal is removed from the
pump. Wear patterns on the finished faces
cannot be realigned during reassembly.
Reusing an old seal could result in prema-
ture failure.
Handle the seal parts with extreme care to prevent
damage. Be careful not to contaminate precision
finished faces; even fingerprints on the faces can
shorten seal life. If necessary, clean the faces with a
non-oil based solvent and a clean, lint-free tissue.
Wipe
lightly
in a concentric pattern to avoid
scratching the faces.