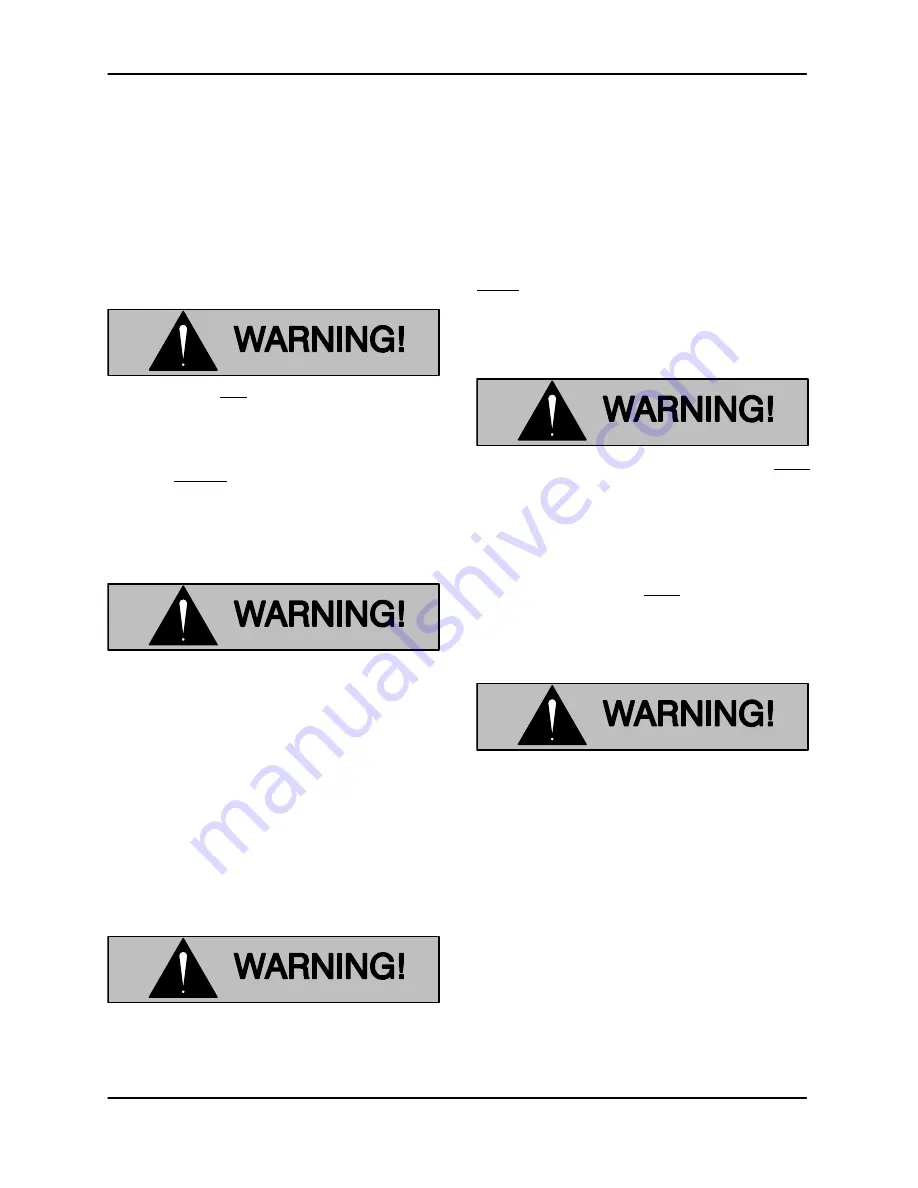
OM-06628
SFV & SFEV SERIES X‐PROOF PUMPS
PAGE A - 2
SAFETY
that the pump and control box are prop
erly grounded and that the incoming
power matches the requirements of the
pump and controls. Install and operate
the control box in accordance with the
National Electric Code and all local
codes. Failure to follow the instructions
in this warning could result in injury or
death to personnel.
This pump is not designed to pump vol
atile, flammable, or corrosive liquids.
The maximum temperature of the liquid
being pumped should not exceed 104
_
F
(40
_
C); do not apply the pump at higher
temperatures. Do not attempt to pump
any liquids which may damage the
pump or endanger personnel as a result
of pump failure.
The following precautions should be
taken before attempting to open or ser
vice the pump; otherwise, injury or
death could result.
1. Familiarize yourself with this man
ual.
2. Lock out incoming power to the
control box to ensure that the
pump will remain inoperative.
3. Allow the pump to completely cool
if overheated.
4. Close the discharge valve (if
used).
Death or serious personal injury and
damage to the pump or components
can occur if proper lifting procedures
are not observed. Make certain that
hoists, chains, slings or cables are in
good working condition and of suffi
cient capacity. Do not attempt to lift this
pump by the motor or control cables, or
the piping. Attach proper lifting equip
ment to the lifting bail fitted on the
pump. Discharge hoses and piping
must be removed from the pump before
lifting. Lift the pump only as high as ne
cessary and keep personnel away from
suspended objects.
This pump was wired at the factory only
for the voltage shown on the nameplate.
Do not attempt to change the voltage on
a dual‐voltage motor. If desired to have
the voltage changed, return the pump to
the factory or to an authorized Gorman‐
Rupp repair facility only; otherwise, the
pump warranty will be negated, and
damage to the pump, and injury or death
to personnel can result.
The electrical power used to operate
this pump is high enough to cause inju
ry or death. Obtain the services of a
qualified electrician to make all electri
cal connections. Make certain that the
pump and enclosure are properly
grounded; never use gas pipe as an
electrical ground. Be sure that the in
coming power matches the voltage and
phase of the pump and control before
connecting the power source. Do not
run the pump if the voltage is not within
the limits. If the overload unit is tripped
during pump operation, correct the
problem before restarting the pump.