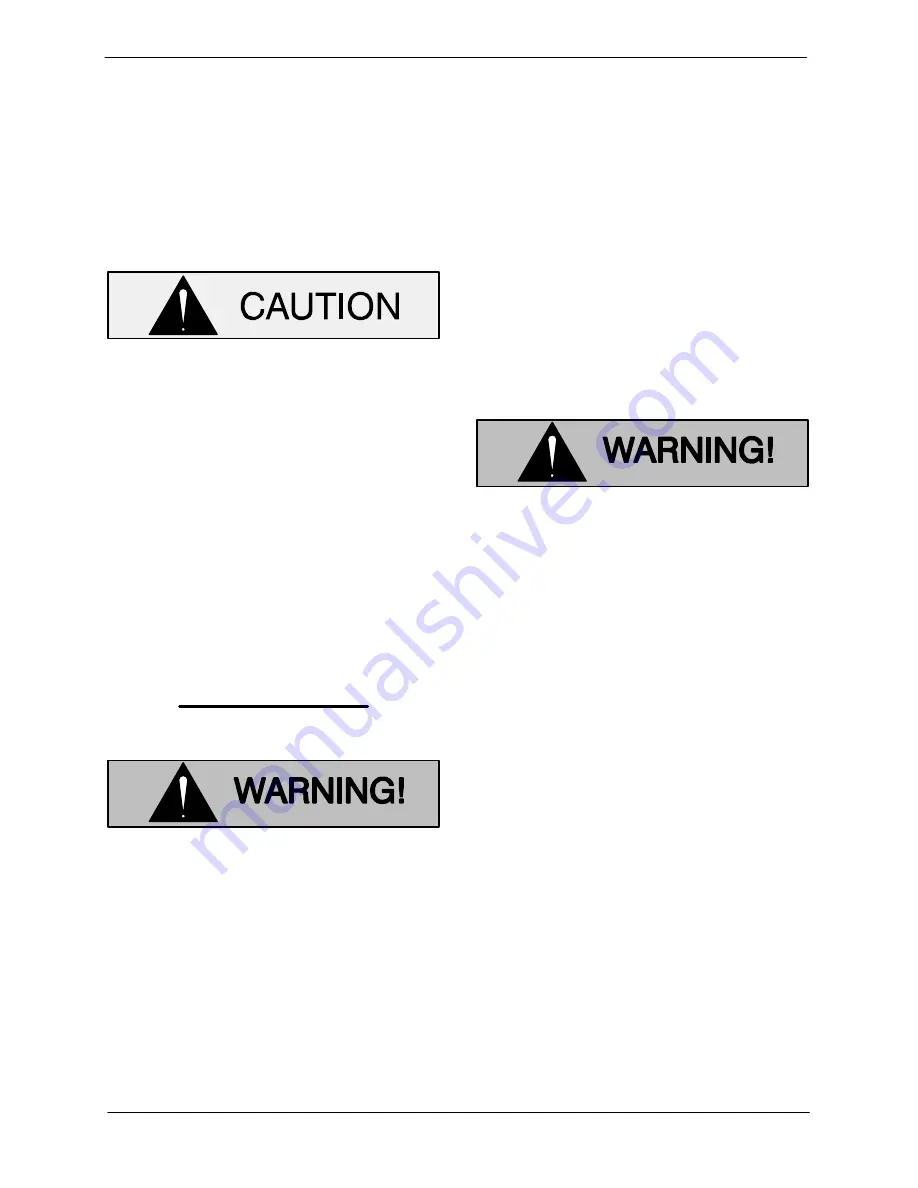
0 SERIES
OM-01194
PAGE B - 3
INSTALLATION
Lifting
Pump unit weights will vary depending on the
mounting and drive provided. Check the shipping
tag on the unit packaging for the actual weight, and
use lifting equipment with appropriate capacity.
Drain the pump and remove all customer‐installed
equipment such as suction and discharge hoses
or piping before attempting to lift existing, installed
units.
The pump assembly can be seriously
damaged if the cables or chains used to lift
and move the unit are improperly wrapped
around the pump.
Due to the confined mounting location,
specialized equipment such as a transmis
sion jack with custom brackets should be
used to lift and position the pump and
gearbox.
NOTE
If the gearbox is rotated out of the standard position
shown in Figure 1, the oil fill and drain plugs must
be relocated. The oil vent must be relocated to the
highest port. Consult the factory for correct posi
tioning of the fill plug to provide for proper lubrica
tion of the gearbox.
ALIGNMENT
When installing and/or aligning univer
sal shaft assemblies, disconnect the
power source to ensure that the pump
will remain inoperative.
The alignment of the pump and its power source is
critical for trouble‐free mechanical operation. Be
fore checking alignment, make sure that the gear
box mounting bolts are tight.
When connecting the universal joint drive shaft as
sembly to a PTO unit, install, support, and align the
drive shaft in accordance with the manufacturer's
instructions. The pump and the drive power source
are generally positioned so that shaft centerlines
are parallel and horizontal. The maximum operat
ing angle should not exceed 15
_
(see Figure 2).
Check the direction of rotation of the PTO unit be
fore starting the pump. The drive shaft must rotate
in the direction shown on the body of the pump,
gearbox, and/or decals, tags, and labels.
Do not operate the pump without the
guard in place over the rotating parts.
Exposed rotating parts can catch cloth
ing, fingers, or tools, causing severe in
jury to personnel.
After the power take‐off has been aligned, block
the wheels of the external power source, engage
the braking system, or take other precautions to
ensure that the power source will remain station
ary. Block the wheels on the unit to prevent creep
ing.