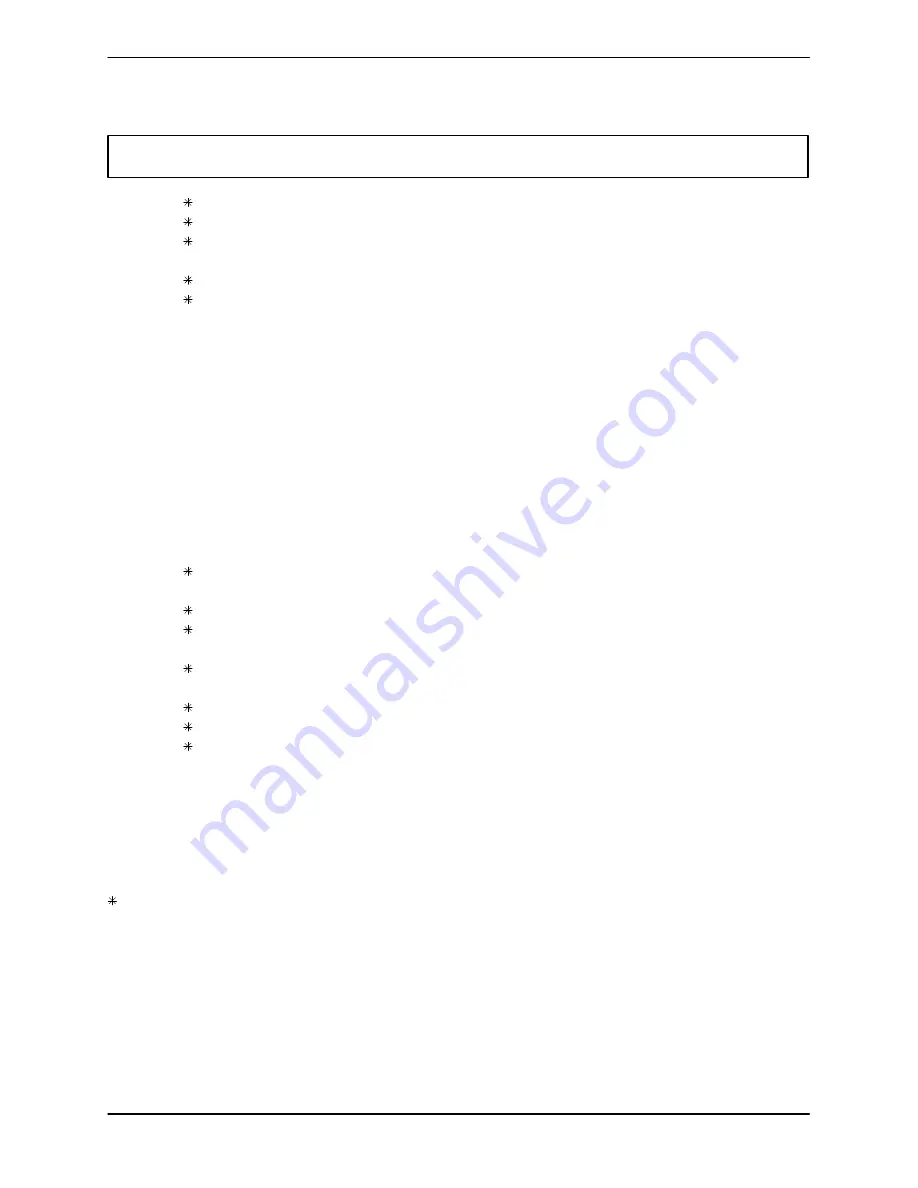
SUPER T SERIES
OM-05512
MAINTENANCE & REPAIR
PAGE E - 8
PARTS LIST
Repair Rotating Assembly
ITEM
NO.
PART NAME
PART
NUMBER
QTY
1
IMPELLER
10528 11010
1
2
ADJ. SHIM SET
37J 17090
REF
3
1.50 SEAL ASSY
46513-151
1
4
SEAL PLATE
38272-234 10010
1
5
GASKET
10959G 20000
1
6
OIL SEAL
S1352
3
7
LOCK WASHER
J08 15991
4
8
HEX HEAD CAP SCREW
B0805-1/2 15991
4
9
BEARING HOUSING
38251-415 10000
1
10
VENTED PIPE PLUG
4823A 15079
1
11
AIR VENT
S1530
1
12
REDUCER PIPE BUSHING
AP0802 15079
1
13
PIPE PLUG
P12 15079
1
14
SIGHT GAUGE
S1471
2
15
PIPE PLUG
P04 15079
2
16
CAPSCREW - .375 x 1.375
21632-936
8
17
LOCK WASHER
J06 15991
8
18
DRIVE FLANGE
38545-005 10000
1
19
INTERMEDIATE GUARD
42381-509 24152
2
20
GASKET
38683-275 18000
1
21
RETAINING RING
S442
1
22
BALL BEARING
S375
1
23
KEY
N0608 15990
1
24
v
IMPELLER SHAFT
38514-822 1706H
1
25
BALL BEARING
S1088
1
26
PIPE PLUG
PC20 10009
1
27
O‐RING
25152-273 1
28
ADJ. SHIM
13130-3 17040
8
29
O‐RING
S1674 1
30
ASSEMBLY PLATE
2613GG 13990
1
31
DRIVE SCREW
BM#04-03 17000
2
32
SHIPPING PLUG
11495B 15079
2
NOT SHOWN:
INSTRUCTION TAG
6588U
1
WARNING DECAL
38817-102
1
INDICATES PARTS RECOMMENDED FOR STOCK