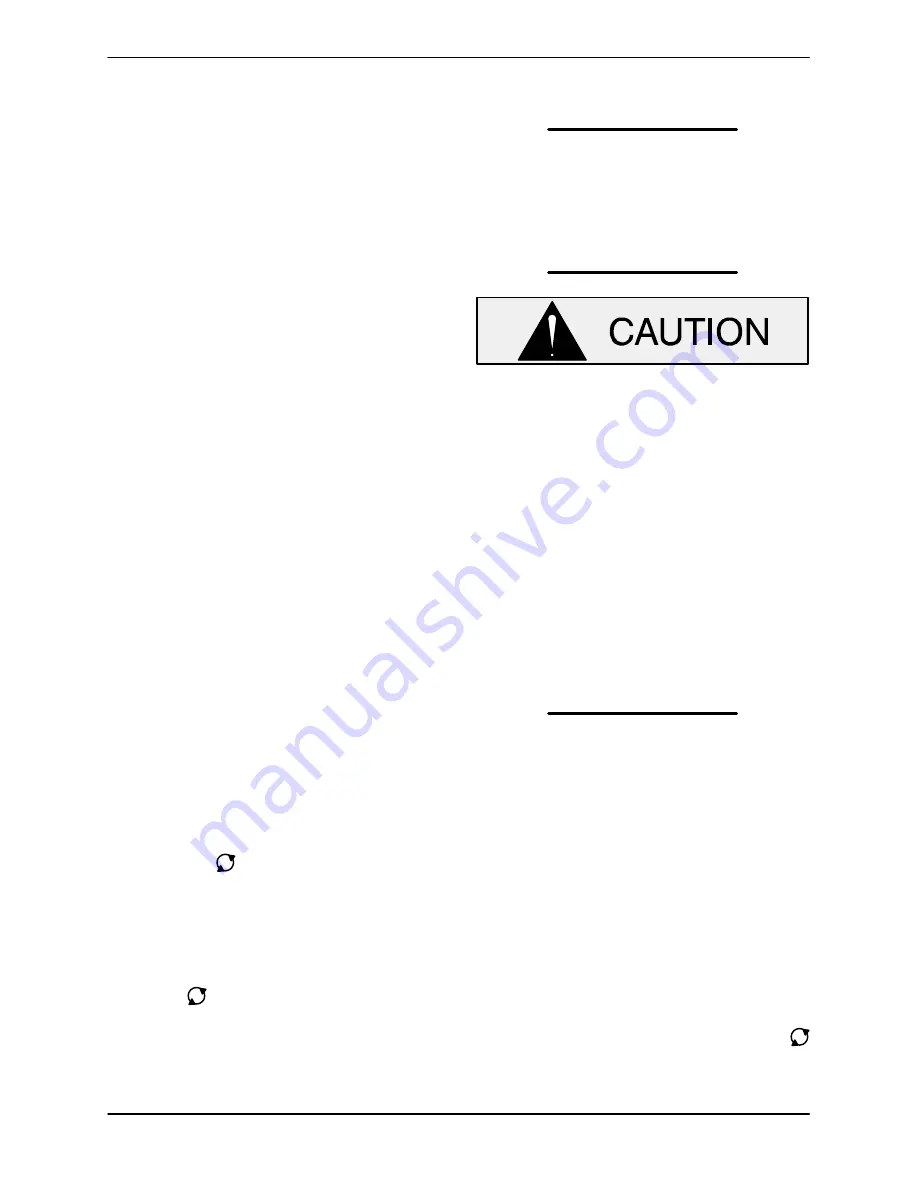
OM-05514
SUPER T SERIES
OPERATION
PAGE C - 4
EPS Functions
Actual functions of the control occur as follows:
Power is applied to the unit.
Unit performs display test for approximately 4
seconds.
When the pressure level showing is equal to or
greater than the “A.on” setpoint, the Horn out
put contacts will close in approximately 1 sec
ond and a delay, equal to the “Hrn dLy” time,
will occur before the A output contacts close.
When the level showing is equal to or greater
than the “B.on” setpoint, the B output contacts
will close in approximately 1 second.
When the pressure decreases to a level equal
to or less than the “B.of” setpoint, B output
contacts will open in approximately one sec
ond.
When the pressure decreases to a level equal
to or less than the “A.of” setpoint, A output con
tacts will open in approximately one second.
If an optional Low Temperature Thermostat is
connected to the unit and the thermostat con
tacts close, the unit displays “lo tpt” on the dis
play. In approximately 1 second, the Horn out
put contacts close, then after the “Hrn dLy”
time, A output contacts close. A output con
tacts will remain closed as long as Low Tem
perature Thermostat contacts are closed.
When the Low Temperature Contacts open, A
output contact will open
only
if the level is
equal to or less than the “A.off” setpoint.
As long a the Low Temperature Thermostat
contacts are closed, the display will show “lo
tpt” unless
switch is pressed to display
some other information. Level is not viewable
until the Low Temperature Thermostat con
tacts open.
The user may wish to check Setpoints Off/On
and Horn output/A output delay times. “Bump
ing” the
switch will display all of the informa
tion desired.
NOTE
One second delays in contact opening/closing is a
result of time sampling of the pressure signal to fil
ter false signals that could cause “nuisance” trip
ping of the contacts.
NOTE
If the “Hrn dLy” is changed during the actual A out
put delay cycle, the current cycle is not changed;
the change becomes effective on the next A output
delay cycle.
Use caution to ensure that the “‐‐.on” set
point (i.e. “A.on”) is not adjusted to a level
less than the corresponding “‐‐.of” set
point (i.e. “A.of”). Improper adjustment of
the off/on setpoints will render the unit non‐
functional, resulting in flooding.
EPS Calibration
NOTE
Zero offset and span adjustments are only neces
sary to calibrate a new unit, or when replacing the
transducer. Once calibrated, “ON” and “OFF” set
points will be stored in the unit's memory. Liquid
level adjustments will be used whenever “ON” and
“OFF” liquid levels must be reset.
There are two reasons for the user to calibrate the
unit. When power is applied, the unit confirms set
points and other calibration information for validity.
If the setpoints are not valid, the LCD screen shows
“EEP bAd” and the unit must be recalibrated. Also,
if the unit is moved, or some other external change
takes place, the unit must be recalibrated.
Zero Adjustment
Zero adjustment tells the unit when the transducer
is exposed to zero water (atmospheric) pressure.
When recalibration is desired, hold the transducer
in hand and apply power to the unit. The LCD
screen will display “Level ABC”. Press and hold
for 5 seconds. The LCD screen displays “Input?
External XDUCR”. Perform the following calibration
procedures.