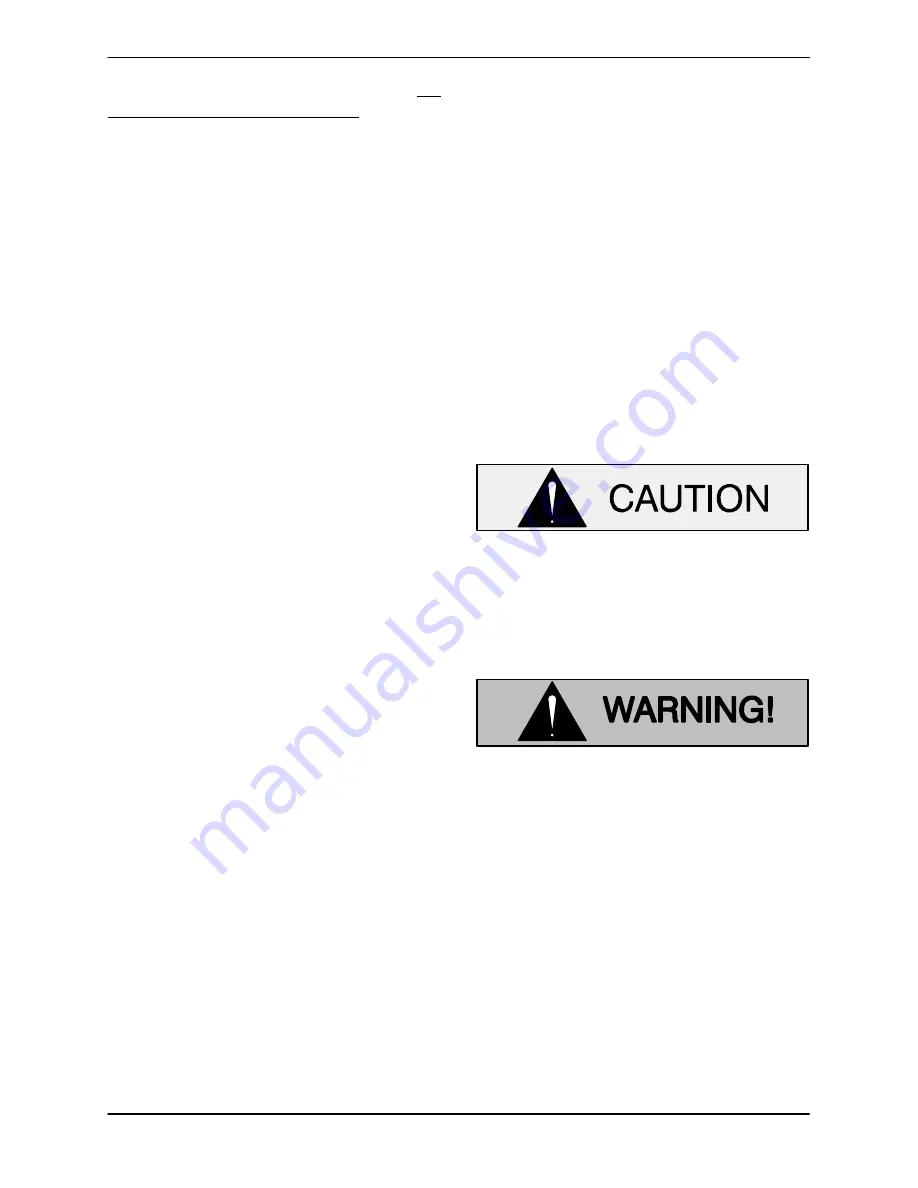
SUPER T SERIES
OM-05498
OPERATION
PAGE C - 3
gaged to be ejected with great force. Af
ter the pump completely cools, drain the
liquid from the pump by removing the
casing drain plug. Use caution when re
moving the plug to prevent injury to per
sonnel from hot liquid.
As a safeguard against rupture or explosion due to
heat, this pump is equipped with a pressure relief
valve which will open if vapor pressure within the
pump casing reaches a critical point. If overheating
does occur, stop the pump immediately and allow
it to cool before servicing it.
Approach any over
heated pump cautiously
. It is recommended that
the pressure relief valve assembly be replaced at
each overhaul, or any time the pump casing over
heats and activates the valve.
Never
replace this
valve with a substitute which has not been speci
fied or provided by the Gorman‐Rupp Company.
Strainer Check
If a suction strainer has been shipped with the
pump or installed by the user, check the strainer
regularly, and clean it as necessary. The strainer
should also be checked if pump flow rate begins to
drop. If a vacuum suction gauge has been in
stalled, monitor and record the readings regularly
to detect strainer blockage.
Never
introduce air or steam pressure into the
pump casing or piping to remove a blockage. This
could result in personal injury or damage to the
equipment. If backflushing is absolutely neces
sary, liquid pressure
must
be limited to 50% of the
maximum permissible operating pressure shown
on the pump performance curve.
Pump Vacuum Check
With the pump inoperative, install a vacuum gauge
in the system, using pipe dope on the threads.
Block the suction line and start the pump. At oper
ating speed the pump should pull a vacuum of 20
inches (508,0 mm) or more of mercury. If it does
not, check for air leaks in the seal, gasket, or dis
charge valve.
Open the suction line, and read the vacuum gauge
with the pump primed and at operation speed.
Shut off the pump. The vacuum gauge reading will
immediately drop proportionate to static suction
lift, and should then stabilize. If the vacuum reading
falls off rapidly after stabilization, an air leak exists.
Before checking for the source of the leak, check
the point of installation of the vacuum gauge.
STOPPING
Never halt the flow of liquid suddenly. If the liquid
being pumped is stopped abruptly, damaging
shock waves can be transmitted to the pump and
piping system. Close all connecting valves slowly.
On engine driven pumps, reduce the throttle
speed slowly and allow the engine to idle briefly be
fore stopping.
If the application involves a high discharge
head, gradually close the discharge
throttling valve before stopping the pump.
After stopping the pump, lock out or disconnect
the power source to ensure that the pump will re
main inoperative.
Do not operate the pump against a
closed discharge throttling valve for
long periods of time. If operated against
a closed discharge throttling valve,
pump components will deteriorate, and
the liquid could come to a boil, build
pressure, and cause the pump casing to
rupture or explode.
Cold Weather Preservation
In below freezing conditions, drain the pump to
prevent damage from freezing. Also, clean out any
solids by flushing with a hose. Operate the pump
for approximately one minute; this will remove any
remaining liquid that could freeze the pump rotat
ing parts. If the pump will be idle for more than a