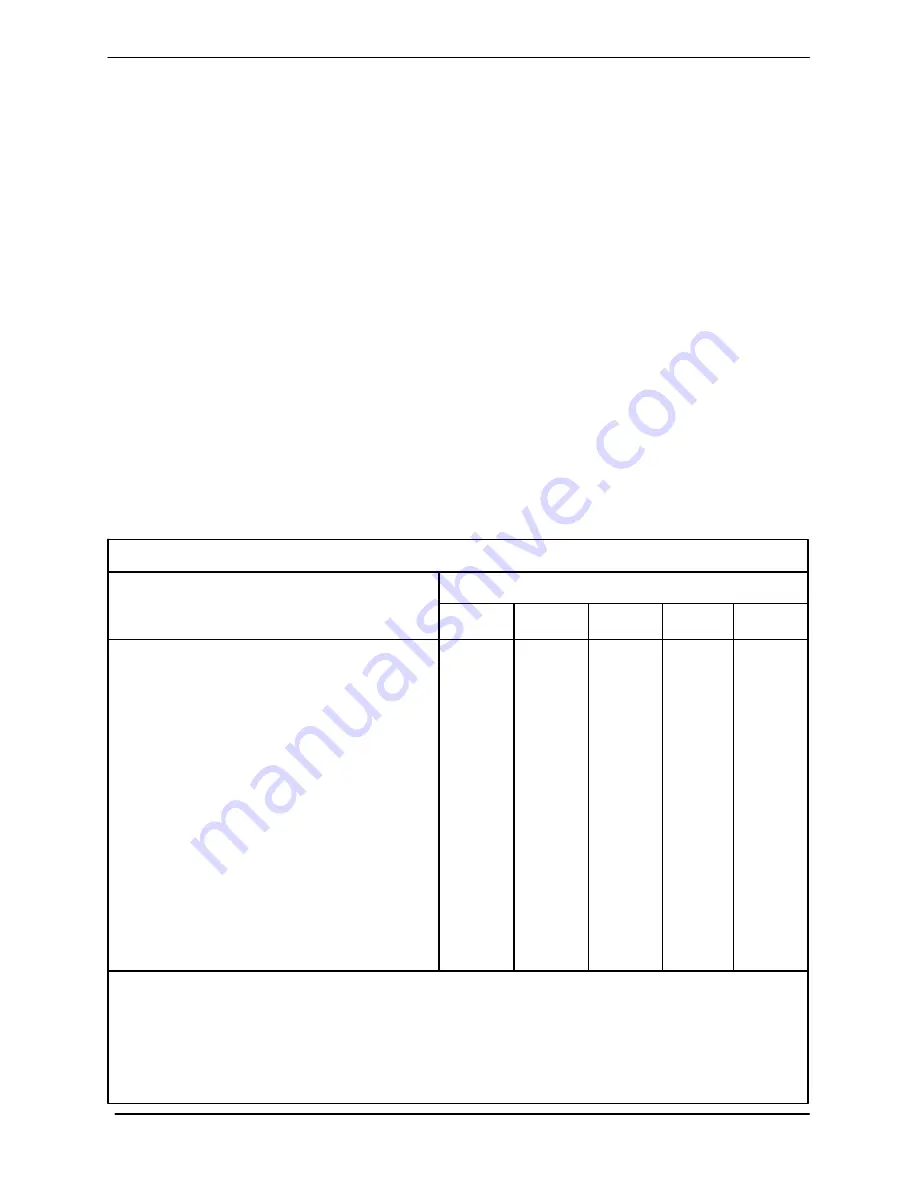
OM−05850
G-R
TROUBLESHOOTING
PAGE D − 2
PUMP PREVENTIVE MAINTENANCE
The following preventive maintenance information
applies to self-priming centrifugal pumps only. Un-
der normal conditions, the Air Release Valve re-
quires no preventive or routine maintenance. How-
ever, in extreme conditions dust or dirt may clog
the spring cavity, preventing full valve closure.
Check the spring cavity regularly and, if blockage
occurs, flush with clean water.
Since pump applications are seldom identical, and
pump wear is directly affected by such things as
the abrasive qualities, pressure and temperature
of the liquid being pumped, this section is intended
only to provide general recommendations and
practices for pump preventive maintenance. Re-
gardless of the application however, following a
routine preventive maintenance schedule will help
assure trouble-free performance and long life from
your Gorman-Rupp pump. For specific questions
concerning your application, contact your Gor-
man-Rupp distributor or the Gorman-Rupp Com-
pany.
Record keeping is an essential component of a
good preventive maintenance program. Changes
in suction and discharge gauge readings (if so
equipped) between regularly scheduled inspec-
tions can indicate problems that can be corrected
before system damage or catastrophic failure oc-
curs. The appearance of wearing parts should also
be documented at each inspection for comparison
as well. Also, if records indicate that a certain part
(such as the seal) fails at approximately the same
duty cycle, the part can be checked and replaced
before failure occurs, reducing unscheduled down
time.
For new applications, a first inspection of wearing
parts at 250 hours will give insight into the wear rate
for your particular application. Subsequent inspec-
tions should be performed at the intervals shown
on the chart below. Critical applications should be
inspected more frequently.
General Condition (Temperature, Unusual
Noises or Vibrations, Cracks, Leaks,
Loose Hardware, Etc.)
I
Pump Performance (Gauges, Speed, Flow)
I
Bearing Lubrication
I
R
Seal Lubrication (And Packing Adjustment,
If So Equipped)
I
R
V-Belts (If So Equipped)
I
Front Impeller Clearance (Wear Plate)
I
Rear Impeller Clearance (Seal Plate)
I
Check Valve
I
Pressure Relief Valve (If So Equipped)
C
Pump and Driver Alignment
I
Shaft Deflection
I
Bearings
I
Bearing Housing
I
Piping
I
Driver Lubrication − See Mfgr’s Literature
Legend:
I = Inspect, Clean, Adjust, Repair or Replace as Necessary
C = Clean
R = Replace
* Service interval based on an intermittent duty cycle equal to approximately 4000 hours annually.
Adjust schedule as required for lower or higher duty cycles or extreme operating conditions.
Pump Preventive Maintenance Schedule
Item
Daily
Weekly
Monthly
Semi-
Annually
Annually
Service Interval*