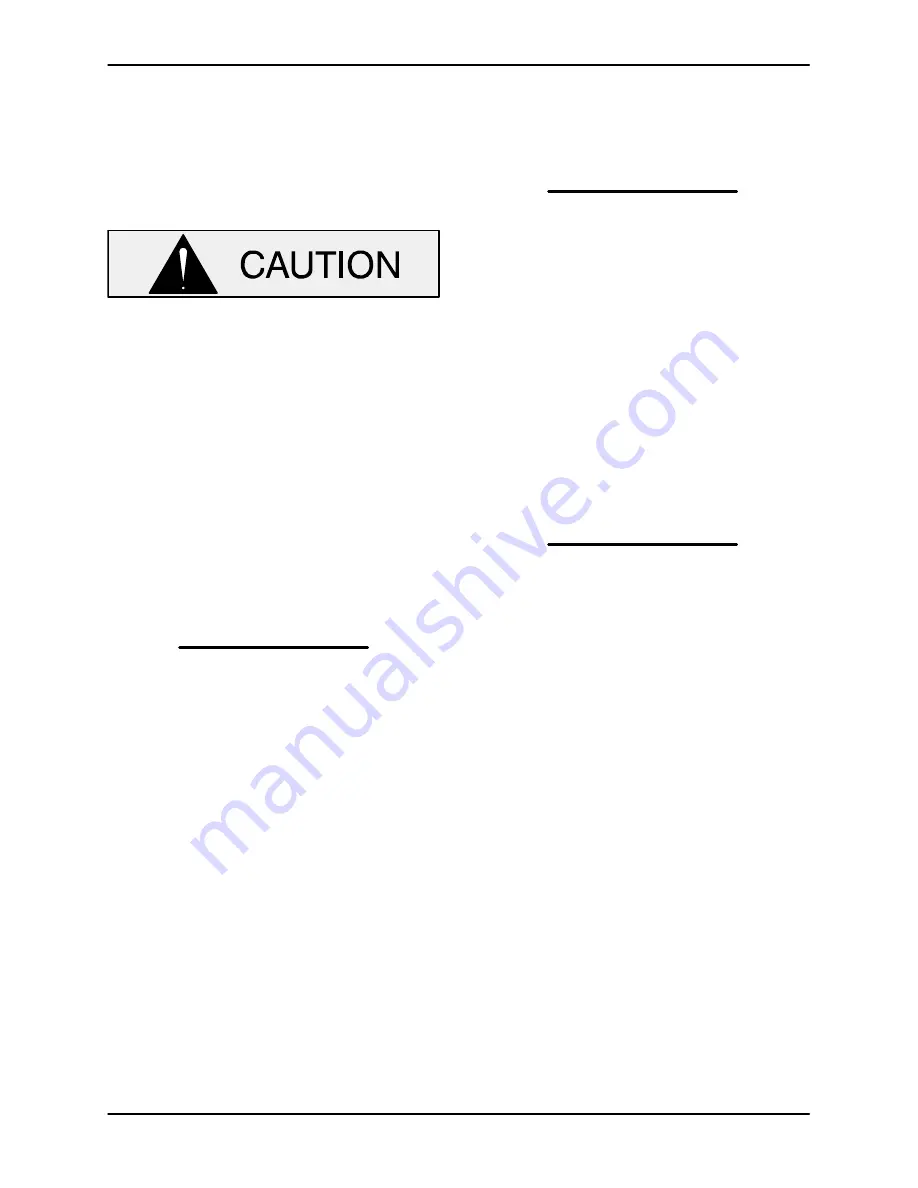
10 SERIES
OM−00698
MAINTENANCE & REPAIR
PAGE E − 14
Impeller Installation And Adjustment
(Figure 2)
Inspect the impeller, and replace it if cracked or
badly worn.
The shaft and impeller threads
must
be
completely clean before reinstalling the im-
peller. Even the slightest amount of dirt on
the threads can cause the impeller to seize
to the shaft, making future removal difficult
or impossible without damage to the im-
peller or shaft.
Install the same thickness of impeller adjusting
shims (22) as previously removed, and screw the
impeller onto the shaft until tight.
NOTE
At the slightest sign of binding,
immediately
back
the impeller off, and check the threads for dirt.
Do
not
try to force the impeller onto the shaft
.
A clearance of .020 to .040 inch (0,51 to 1,02 mm)
between the impeller and the seal plate is neces-
sary for maximum pump efficiency. Measure this
clearance, and add or remove impeller adjusting
shims as required.
Remove the two capscrews temporarily holding
the seal plate, and install the same thickness of
casing gaskets (52) as previously removed. Se-
cure the seal plate and pump casing to the inter-
mediate with the nuts (26).
Do not
fully tighten the
nuts until the impeller face clearance has been set.
A clearance of .010 to .020 inch (0,25 to 0,51 mm)
between the impeller and the wear plate is also rec-
ommended for maximum pump efficiency. This
clearance must be set after installing the back
cover, by adding or removing gaskets in the pump
casing gasket set until the impeller scrapes against
the wear plate when the shaft is turned. After the
impeller scrapes, add approximately .010 inch
(0,25 mm) of gaskets.
NOTE
An alternate method of adjusting this clearance is to
reach through the discharge port with a feeler
gauge and measure the gap. Add or subtract pump
casing gaskets accordingly.
Suction Check Valve Installation
(Figure 2)
Inspect the check valve components, and replace
the parts as required. Subassemble the check
valve gasket (75) and weights (74 and 76) with the
hardware (72 and 73). Position the assembled
check valve in the mounting slot in the check valve
seat (77).
NOTE
Apply ‘Permatex Aviation No. 3 Form-A-Gasket’ or
equivalent compound to the suction flange and
check valve seat mating surfaces before reassemb-
ly.
Replace the seat gasket (78) and secure the check
valve and seat to the pump casing with the round
head machine screws (69).
Replace the suction flange gasket (65) and secure
the suction flange to the check valve seat and
pump casing with the hardware (67 and 68).
Back Cover Installation
(Figure 2)
If the wear plate (53) was removed for replace-
ment, carefully center it on the back cover and se-
cure it with the hardware (55 and 56). The wear
plate
must
be concentric to prevent binding when
the back cover is installed.
Clean any scale or debris from the contacting sur-
faces in the pump casing that might interfere or
prevent a good seal with the back cover. Replace
the back cover gasket (57) and slide the back
cover assembly into the pump casing. Be sure the
wear plate does not bind against the impeller.
NOTE
To ease future disassembly, apply a film of grease
or ‘Never-Seez’ on the back cover shoulder, or any