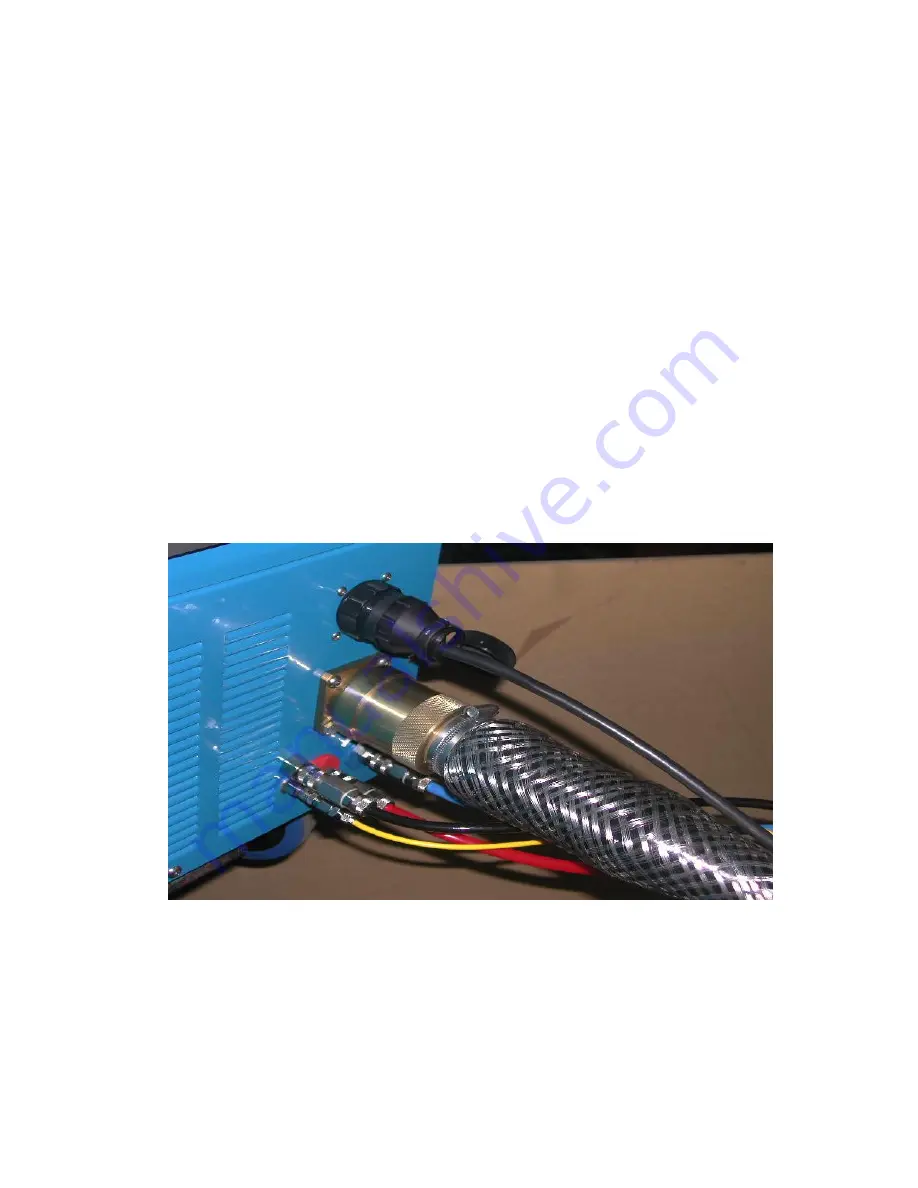
P30U Instruction Manual Revision : 1
1st December 2006
Page 9
4.
PLASMA AND TORCH CONNECTIONS
4.1 Connecting the Torch and Plasma Earth Lead to the Power Unit
Note.
Do not run the power unit without the torch connected.
The connections to the power unit are located at the front of the unit.
The PTU torch and umbilical extensions use a specially designed electrical connector for the power,
safety earth, pilot arc, and all other electrical connections. There is a central pin that carries the
power, a pin for the pilot arc connection and 5 smaller pins for safety monitoring and the diver’s
control switch. The safety earth is made through the locking sleeve. There are four hose connectors,
filled with quick acting connectors.
the blue hose is the cooling water to the torch;
the red hose is the cooling water return from the torch
the black hose carries the plasma air
the yellow hose is a “pneumo” connection to allow the plasma air pressure to
automatically track the working depth
The water connections are not polarised but it is advisable to follow the colour coding.
These connectors are found on the machine front panel and replicated at the socket end of the ex-
tension umbilicals.
The supervisor’s remote control panel connects to a multiway socket above the torch connectors.
(Note that this is an “analogue” lamp, therefore it may be illuminated but not at full brightness,
and the indicator (which is “digital”) on the front panel and the supervisors panel still fail to
light because of a poor connection).
When first switching on, allow enough time for the water to circulate through the system. Top up the
header tank as required. Use only distilled or de-ionised water. (See section 7.1 regarding use of
methanol in freezing conditions).
The two earth connectors (insert and twist clockwise to lock) are located on the left hand side of
the front panel. An indicator lamp indicates when an earth loop has been successfully made.