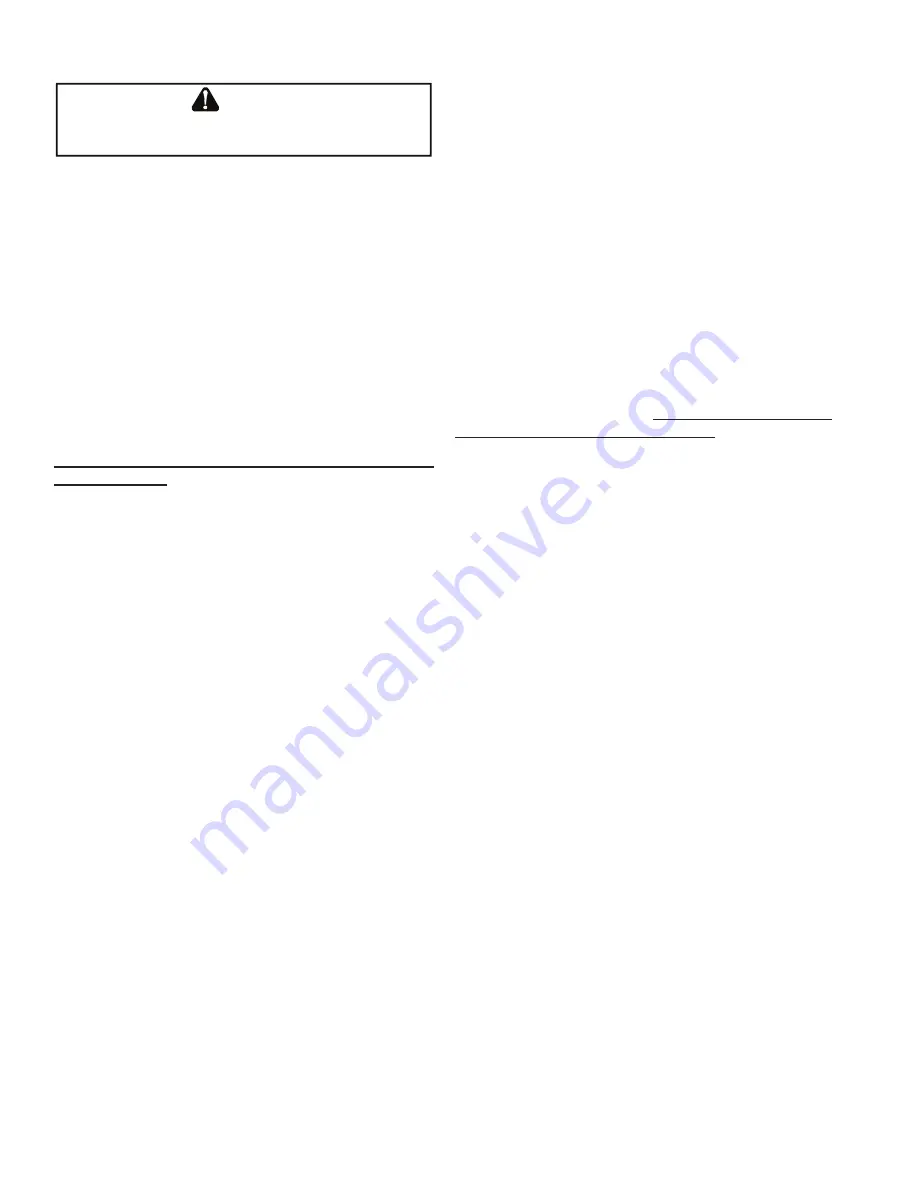
12
SYSTEM OPERATION
T
O
AVOID
PERSONAL
INJURY
OR
DEATH
DUE
TO
ELECTRICAL
SHOCK
,
TURN
OFF
POWER
TO
THE
FURNACE
BEFORE
CHANGING
SPEED
TAPS
.
WARNING
Circulator Blower Speed Facts
1. Motor speed Tap wiring must remain in factory position
on the control board and motor.
2. There are 4 speed Tap wires to the motor T1, T2, T3,
T4.
3. There are 5 speeds available, depending on DIP switch
settings and found in air flow table for each size fur
-
nace.
4. Heating input (W1/ W2) always has priority over all
other thermostat input.
5. Cooling input (YLo/ Y) has priority over continuous fan
input.
6. Continuous fan input (G) has lowest priority.
*The blower speed wiring connections must remain in
factory position
.
1. Refer to the air flow table for your specific model fur
-
nace.
2. If a cooling or heat pump condensing unit is being used
in conjunction with this furnace, the three DIP switches
in S2 are used to select the proper cooling speeds to
match the outdoor unit size. Typical CFM requirements
are 400 CFM / Ton.
1. Turn OFF power to the furnace.
2. Select the cooling blower speeds that match the instal
-
lation requirements from the airflow table in this manual
or the Installation Manual, If factory cooling speeds do
not match the installation requirements, the dip switch
settings must be changed from factory position
3. Turn ON power to furnace.
4. Verify proper temperature rise in heat modes and CFM
in cooling modes
CIRCULATING AIR AND FILTERS
DUCTWORK - AIR FLOW
Duct systems and register sizes must be properly designed
for the C.F.M. and external static pressure rating of the
furnace. Ductwork should be designed in accordance with
the recommended methods of "Air Conditioning Contractors
of America" manual D.
A duct system should be installed in accordance with
Standards of the National Board of Fire Underwriters for
the Installation of Air Conditioning, Warm Air Heating and
Ventilating Systems, Pamphlets No. 90A and 90B.
A return air filter is not supplied with the furnace. The
installer must supply a means of filtering all of the return
air. Filter(s) shall comply with UL900 or CAN/ULC-S111
Standards. If the furnace is installed without filters, and is
not covered by the warranty.
Upflow furnaces with air delivery of less than 1800 CFM:
Use one side return or one bottom return ductwork con
-
nection.
Upflow furnaces with air delivery of 1800 CFM or higher:
Use two side returns or one side return and one bottom
return connection.
Guide dimples locate the side and bottom return cutout
locations. Use a straight edge to scribe lines connecting
the dimples. Cut out the opening on these lines. An un
-
dersized opening will cause reduced airflow. For bottom
return connection, remove the bottom of the cabinet before
setting the furnace on the raised platform or return air duct.
A closed return duct system must be used, with the return
duct connected to the furnace.
NOTE:
Ductwork must nev
-
er be attached to the back of the furnace.
Supply and return
connections to the furnace may be made with flexible joints
to reduce noise transmission, if desired. If a central return
is used, a connecting duct must be installed between the
unit and the utility room wall so the blower will not interfere
with combustion air or draft. The room, closet, or alcove
must not be used as a return air chamber.
When the furnace is used in connection with a cooling unit,
the furnace should be installed in parallel with or on the
upstream side of the cooling unit to avoid condensation
in the heating element. With a parallel flow arrangement,
the dampers or other means used to control the flow of
air must be adequate to prevent chilled air from entering
the furnace and, if manually operated, must be equipped
with means to prevent operation of either unit unless the
damper is in the full heat or cool position.
When the furnace is heating, the temperature of the return
air entering the furnace must be between
55°F
and
100°F
.