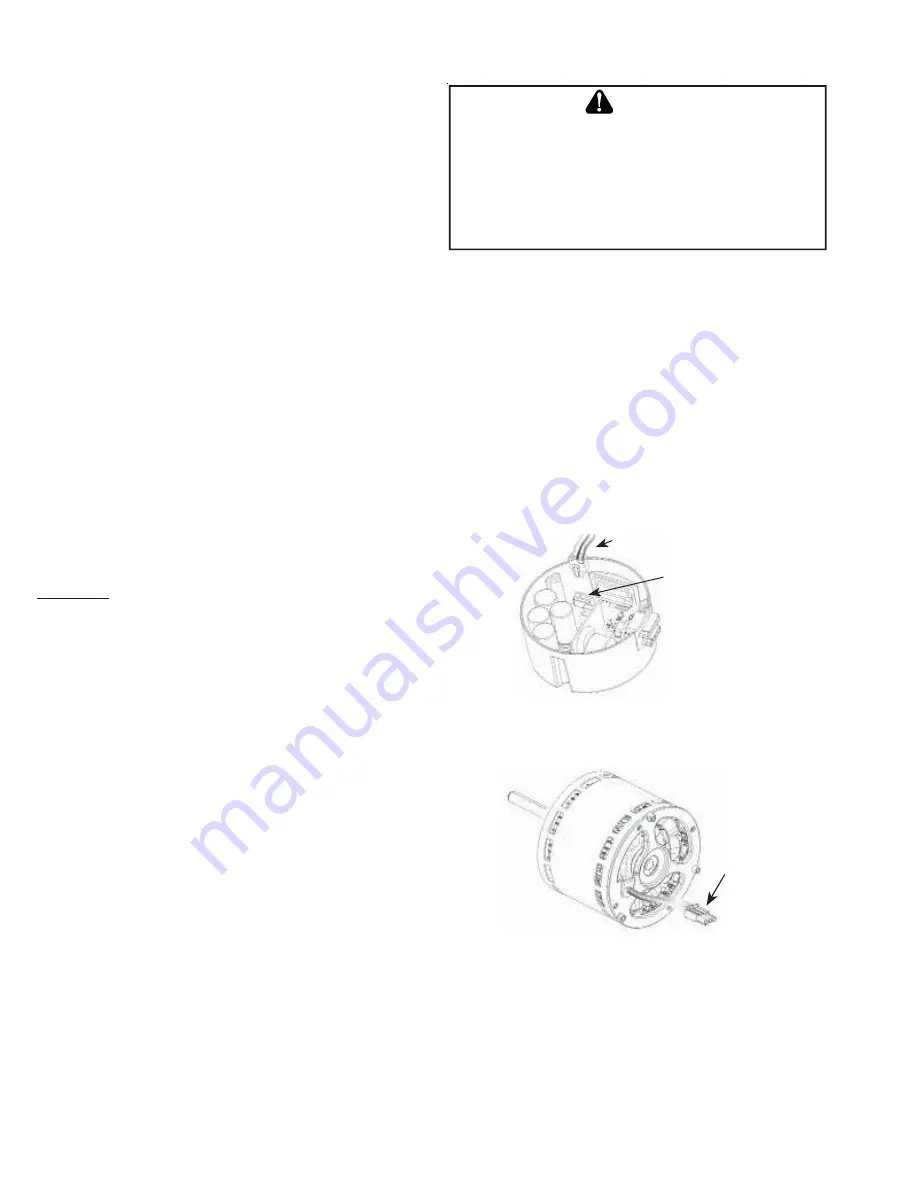
62
High Pressure Switch Operation
•
High Pressure Switch action is used to determine the
inducer speed required to achieve the 100% firing rate
of the appliance. The determination is made by the
IFC during the calibration process.
•
The HPS must remain closed during 100% fire opera-
tion. If it opens during 100% fire operation, the IFC will
increase the inducer speed at a rate of 1% per sec in
an attempt to re-close the pressure switch up to the
maximum allowed RPM. If the HPS is re-closed suc-
cessfully, the IFC will complete the Heat mode and
perform the Calibration routine on the next call for heat.
If the HPS remains open, the IFC will end the Heat
mode through the Post-purge and perform the Calibra-
tion routine immediately (error code “E9” is flashed until
calibration routine is successful).
•
High Pressure Switch check takes place during the
Calibration routine. If the switch is stuck open or closed
calibration will not be completed and the appropriate
error code will be logged and displayed.
Hot Surface Igniter Operation
The IFC energizes a relay to control the line voltage Hot Sur-
face Igniter. The HSI warm up time will be fixed for all ignition
trials. Both the continuity of the igniter and the ability of the
relay to energize the igniter are continuously monitored dur-
ing the Igniter Warm-up and Ignition Activation Periods.
ECM Motor
An Emerson® UltraTech® four wire indoor fan motor provides
supply air to the conditioned space. This is the same motor
used on Goodman & Amana previous generation communi-
cating furnaces.
The ECM motor consists of two sections;
1.
A motor body containing 3 phase motor windings
2.
An electronic control module (end bell).
In the event of a non-operating motor; the following items
should be checked. There are two harnesses which connect
the blower motor to the IFC. The line voltage (5 Pin) harness
provides 115 volts directly off of the IFC L1 and neutral termi-
nals on ½ hp ECM motors. On furnaces with ¾ and 1 HP
ECM motors, L1 is fed to the motor through an inductor coil.
The inductor coil conditions the power supply to the motor
smoothing out spikes and electrical noise. The low voltage
harness is a 4 wire harness that supplies 12 volts DC to
terminals 1 & 4 of the motor and communicating signals on
terminals 3 & 4.
SERVICE & OPERATION
T
HE
CONTROL
MODULE
CONTAINS
COMPONENTS
WHICH
CAN
HOLD
AN
ELECTRICAL
CHARGE
FOR
SEVERAL
MINUTES
. B
EFORE
THE
MOTOR
IS
TAKEN
APART
,
IT
MUST
BE
ALLOWED
TO
DISSIPATE
VOLTAGE
BY
WAITING
FIVE
MINUTES
BEFORE
IT
IS
INSPECTED
INTERNALLY
. T
HE
END
BELL
CAN
BE
SEPARATED
FROM
THE
MOTOR
BODY
BY
REMOVING
THE
THREE
SCREWS
WHICH
JOIN
THEM
. O
NCE
THE
SCREWS
ARE
REMOVED
,
THE
INTERANL
HARNESS
CAN
BE
SEPARATED
. T
HE
CONTROL
MODULE
AND
MOTOR
CAN
THEN
BE
INSPECTED
SEPARATELY
.
WARNING
The motor contains three windings of equal resi / -
10%. Resistance between windings is generally less than
10 ohms and will vary between models. To take this read-
ing; the ohm meter leads are placed in the wiring harness,
previously disconnected from the internal control unit con-
nector.
Inspect capacitors inside the control unit for bulging or swol-
len caps. The end bell should be replaced if components
appear swollen or bulging. A functioning control unit should
have a phase to phase resistance of greater than 100K
between any two pins. A separated control unit is shown
below. To take this reading; the ohm meter leads are placed
in the end bell socket and not in the wiring harness.
3 Wire
Motor-to-Control Harness
3 Pin Connector
Motor
Connector
Beyond basic visual checks and voltage / resistance checks;
the Emerson ECM motor may be tested with an Emerson
UltraCheck-EZ™ diagnostic tool (Goodman Part UTT-01).
This tool will test the motor windings and also the commu-
nicating module of the motor.