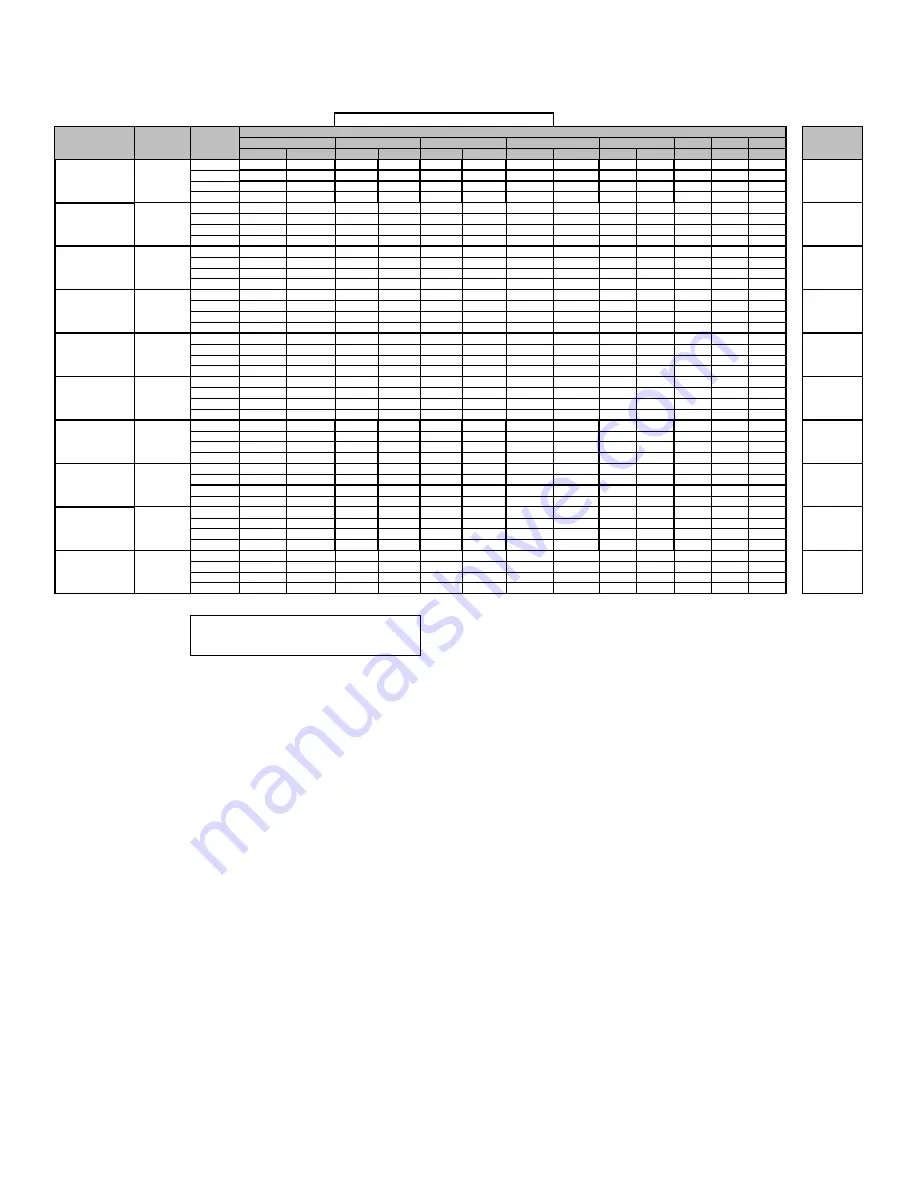
AIRFLOW TABLES
45
GM9S80
0.6
0.7
0.8
CFM
RISE
CFM
RISE
CFM
RISE
CFM
RISE
CFM
RISE
CFM
CFM
CFM
F01^^
658
N/A
585
N/A
545
N/A
495
N/A
444
N/A
390
332
151
F02^
749
40
697
42
652
45
607
49
554
53
509
459
406
F03
925
32
881
34
840
35
800
37
760
39
721
681
645
F04
882
34
841
35
800
37
760
39
719
41
678
641
602
F01^^
659
N/A
599
N/A
542
N/A
490
N/A
437
N/A
383
320
N/A
F02^
1268
35
1221
36
1188
37
1154
38
1122
40
1091
1060
1029
F03
1087
41
1044
43
1008
44
973
46
938
47
905
871
841
F04
1118
40
1070
42
1033
43
997
45
963
46
929
896
865
F01^^
720
N/A
660
N/A
614
N/A
542
N/A
468
N/A
413
359
313
F02^
1289
34
1260
35
1232
36
1194
37
1161
38
1125
1087
1073
F03
1125
40
1089
41
1052
42
1013
44
973
46
947
909
863
F04
1252
36
1198
37
1153
39
1110
40
1069
42
1028
990
953
F01^^
764
N/A
695
N/A
630
N/A
559
N/A
485
N/A
415
358
N/A
F02^
1287
35
1235
36
1191
37
1147
39
1104
40
1062
1020
979
F03
1339
33
1301
34
1258
35
1217
37
1174
38
1131
1090
1048
F04
1396
32
1346
33
1298
34
1257
35
1217
37
1175
1135
1098
F01^^
710
N/A
646
N/A
580
N/A
515
N/A
432
N/A
367
314
274
F02^
1298
46
1255
47
1216
49
1178
50
1140
52
1102
1067
1028
F03
1209
49
1166
51
1124
53
1083
55
1045
57
1005
964
923
F04
1138
52
1091
54
1045
57
1001
59
959
62
920
876
832
F01^^
841
N/A
657
N/A
595
N/A
522
N/A
439
N/A
367
315
N/A
F02^
1141
52
1089
54
1045
57
1001
59
958
62
914
869
823
F03
1311
45
1267
47
1226
48
1189
50
1150
52
1114
1072
1034
F04
1395
42
1347
44
1309
45
1270
47
1233
48
1199
1164
1125
F01^^
831
N/A
750
N/A
671
N/A
588
N/A
501
N/A
405
348
300
F02^
1214
49
1158
51
1103
54
1045
57
989
60
936
883
823
F03
1303
45
1249
47
1191
50
1136
52
1081
55
1028
974
928
F04
1426
42
1375
43
1324
45
1277
46
1229
48
1177
1124
1078
F01^^
837
N/A
752
N/A
671
N/A
576
N/A
501
N/A
426
361
315
F02^
1316
45
1270
47
1218
49
1166
51
1114
53
1061
1000
962
F03
1353
44
1323
45
1286
46
1235
48
1183
50
1131
1085
1040
F04
1587
37
1544
38
1506
39
1459
41
1416
42
1372
1323
1281
F01^^
802
N/A
724
N/A
637
N/A
551
N/A
468
N/A
389
342
294
F02^
1405
53
1356
55
1308
57
1262
59
1210
61
1155
1102
1057
F03
1574
47
1531
48
1484
50
1440
51
1392
53
1357
1306
1256
F04
1619
46
1575
47
1526
49
1489
50
1446
51
1404
1355
1313
F01^^
851
N/A
774
N/A
692
N/A
615
N/A
535
N/A
470
411
359
F02^
1677
53
1629
55
1583
56
1540
58
1498
59
1449
1399
1349
F03
1537
58
1489
60
1444
62
1404
63
1365
65
1322
1272
1211
F04^^
1416
N/A
1365
N/A
1315
N/A
1267
N/A
1220
N/A
1163
1106
1048
20-50
20-50
20-50
35-65
35-65
35-65
35-65
35-65
40-70
W/W1
*M9S800603A*
W/W1
*M9S800603B*
W/W1
*M9S800604B*
W/W1
*M9S800803B*
W/W1
*M9S800804B*
W/W1
TEMP RANGE
25-55
W/W1
*M9S800403A*
MODEL
THERMOSTAT
CALL
^DEFAULT & RECOMMENDED
^^NOT RECOMMENDED FOR HEATING
NOTE:
HEATING AIRFLOW
TAP #
EXTERNAL STATIC PRESSURE, (INCHES WATER COLUMN)
0.1
0.2
0.3
0.4
0.5
*M9S800804C*
W/W1
*M9S800805C*
W/W1
*M9S801005C*
W/W1
*M9S801205D*