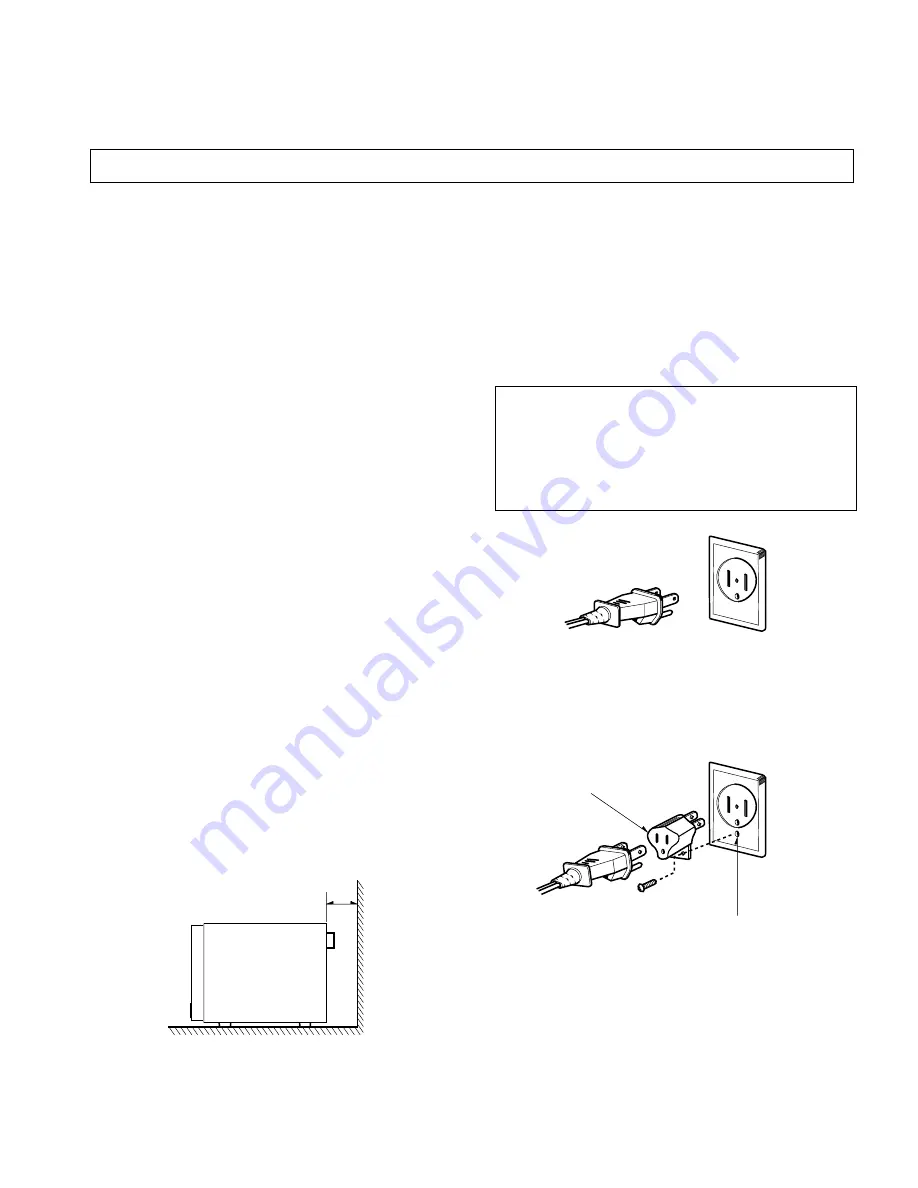
INSTALLATIONS
3-1
INSTALLING
1. Empty the microwave oven and clean inside it with
a soft, damp cloth. Check for damage such as
misaligned door, damage around the door or dents
inside the cavity or on the exterior.
2. Put the oven on a counter, table, or shelf that is
strong enough to hold the oven and the food and
utensils you put in it. (The control panel side of the
oven is the heavy side. Use care when handling.)
3. Do not block the vent and the air intake openings.
Blocking vent or air intake openings can cause
damage to the oven and poor cooking results.
Make sure the microwave oven legs are in place to
ensure proper air flow.
4. The oven should not be installed in any area where
heat and steam are generated, because they may
damage the electronic or mechanical parts of the
unit.
Do not install the oven next to a conventional
surface unit or above a conventional wall oven.
5. Use microwave oven in an ambient temperature
less than 104°F (40°C).
6. Place the microwave oven on a sturdy and flat
surface at least 10 cm (4 inches) from the wall.
7. Place the microwave oven as far away as possible
from TV, RADIO, COMPUTER, etc., to prevent
interference.
GROUNDING INSTRUCTIONS
For personal safety, this appliance must be fully
grounded at all times.
In the event of an electrical short circuit, grounding
reduces the risk of electrical shock.
The plug must be plugged into an outlet that is
properly installed and grounded.
BEFORE YOU BEGIN, READ THE FOLLOWING INSTRUCTIONS COMPLETELY AND CAREFULLY.
10cm
WARNING
Improper use of the grounding plug can result in a
risk of electric shock.
Do not, under any circumstances, cut or remove
the third ground prong from the power cord plug.
PREFERRED METHOD
ENSURE PROPER GROUND
EXISTS BEFORE USE
TEMPORARY METHOD
(ADAPTER PLUGS NOT
PERMITTED IN CANADA)
ALIGN LARGE
PRONGS/SLOTS
ENSURE PROPER GROUND
AND FIRM CONNECTION
BEFORE USE
Summary of Contents for MA2120B
Page 27: ...6 2 13552A 13213A 13352A 13581A 13720D 13806D 14970A 14026A 13536A DOOR PARTS ...
Page 28: ...6 3 24781M 23506A 23572A 268711 WTP018 23550D CONTROLLER PARTS ...
Page 30: ...6 5 56912B 43500A 44510A 466003 466001 466002 55262A 43501A WSZ085 LATCH BOARD PARTS ...
Page 32: ...6 7 63302L 63303L 65006B 948501 63302R 56170D WSZ002 WTT021 63303R BASE PLATE PARTS ...
Page 41: ...8 1 SCHEMATIC DIAGRAM OF P C B ...
Page 42: ...8 2 PRINTED CIRCUIT BOARD ...