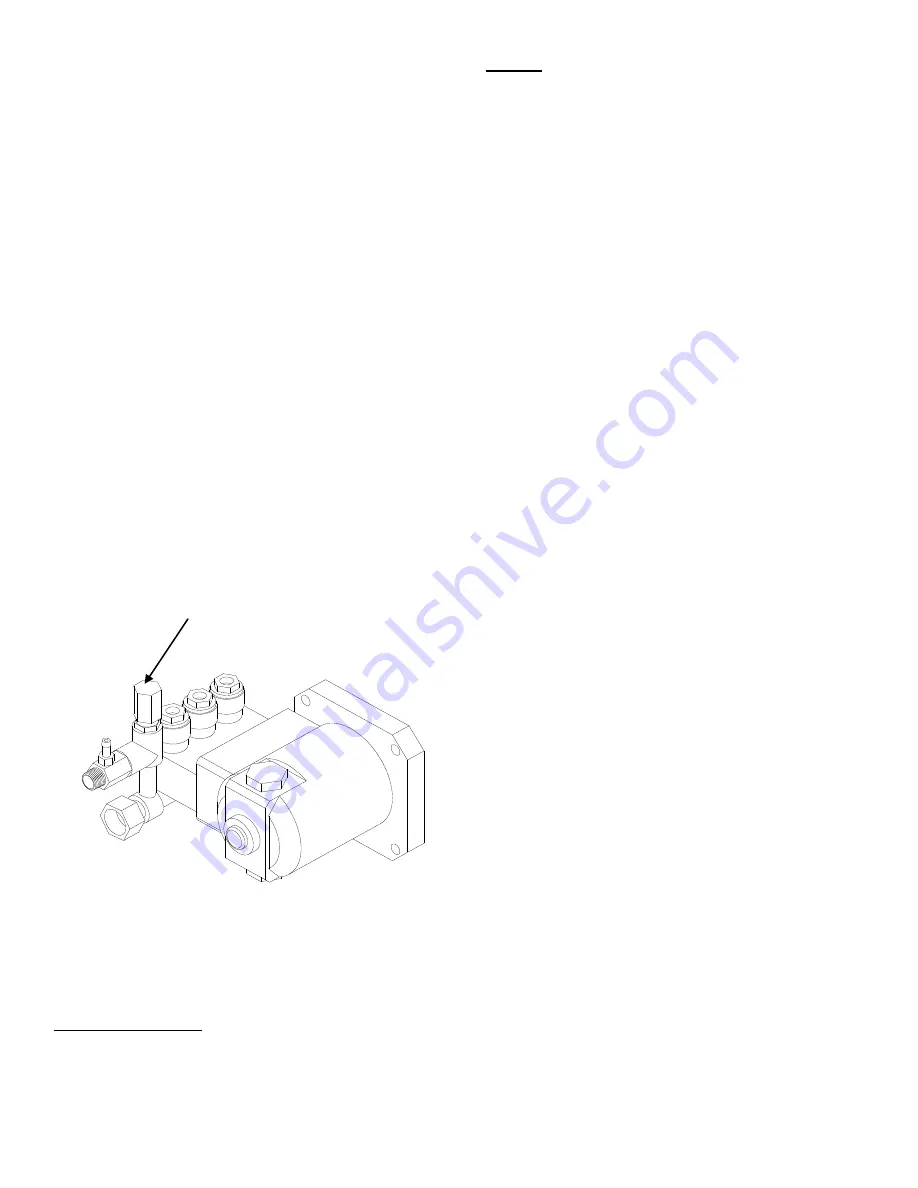
12
2. The black, low-pressure chemical nozzle must be
used to spray chemicals.
3. Squeeze the spray gun trigger. The chemical injector
will draw the chemical into the water stream.
4. Spray detergent onto the surface and allow it to soak.
Chemicals need time to work properly. Follow the
chemical manufacturer’s recommendations for the
recommended time.
5. Change back to high pressure to rinse by inserting one
of the high-pressure nozzles.
6. Hold the lance with two hands in a sturdy stance
position.
7. Point lance at dirty surface and squeeze trigger.
8. Wash from the bottom to the top, using side-to-side
motions. This washes away heavy dirt and allows the
detergent to soak as you work toward the top.
9. Use the width of the spray pattern to wash in a wide
path. Overlap spray paths for complete coverage.
10.The nozzle should be 12” to 24” from the work, closer
for tough areas.
Caution: Be careful on painted or delicate surfaces,
the pressure may damage the surface if the nozzle is
too close.
11. Small parts should be washed in a basket so the
pressure does not push them away. Larger,
lightweight parts should be clamped down.
12. The pressure washer is set to the maximum rated
pressure when it leaves the factory. To adjust the
pressure, turn the unloader knob counter-clockwise.
WARNING: Do not alter the unloader valve’s
maximum pressure. Excess pressures could cause
serious injury and/or pump damage. Any alteration
other than turning the adjustment knob will void
your warranty.
For Steam (Optional)
1. Set the thermostat to 250
F.
2. Turn the Heat switch ON.
3. Insert the steam nozzle into the nozzle holder.
To Stop
1. If detergents were used, draw clear water through the
detergent inlet line to purge detergent. Failure to do
so may clog the chemical injector.
2. If the burner was used, turn off the “Heat” switch and
pump cold water through the coil for 3 minutes.
Insufficient cool down period of high pressure hose
will cause excessive wear and eventual rupturing of
hose.
3. Turn the pump switch OFF.
4. Turn OFF the water supply.
5. Squeeze the trigger to relieve the system pressure.
Unloader
Summary of Contents for 157307
Page 20: ...20 157307 Rev A Parts Breakdown ...
Page 23: ...23 ...
Page 24: ...24 ...
Page 25: ...25 ...
Page 26: ...Cat 2DX Pump Exploded View 26 ...
Page 28: ...28 Distributed by GNE 20195 S Diamond Lake Rd STE 100 Rogers MN 55374 ...