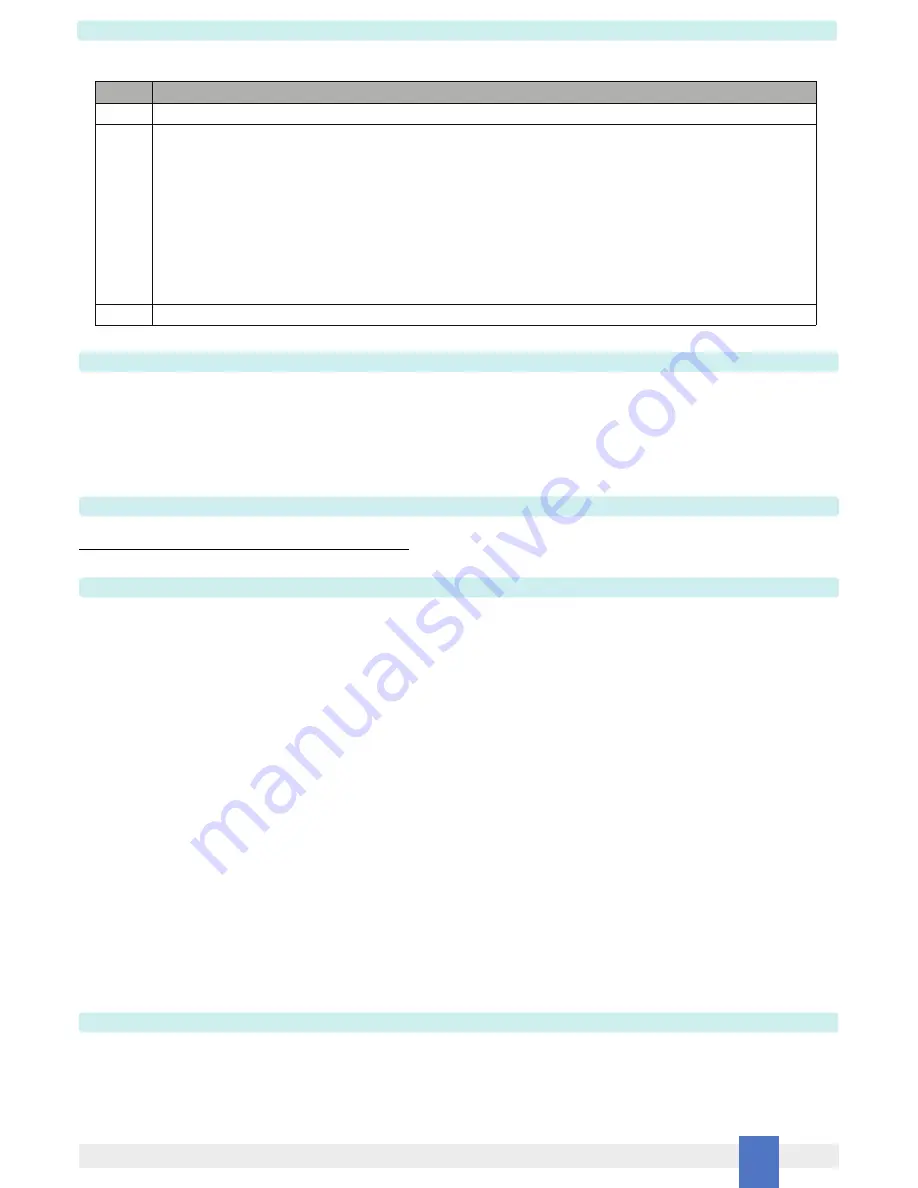
9
D5290S-079
- 5 A SIL 3 Relay Output Module (115 Vac coil voltage)
G.M. International ISM0153-2
Warning
Operation
D5290S-079 relay module is suitable for the switching of safety related circuits, providing isolation between the input and output contacts.
See the previous pages for Functional Safety applications with related SIL value.
A “RELAY STATUS” yellow led lights when input is powered, showing that relay is energized.
Installation
D5290S-079 is a relay output module housed in a plastic enclosure suitable for installation on T35 DIN-Rail according to EN50022.
D5290S-079 unit can be mounted with any orientation over the entire ambient temperature range.
Electrical connection of conductors up to 2.5 mm² are accommodated by polarized plug-in removable screw terminal blocks which can be plugged in/out into a powered unit without
suffering or causing any damage.
The wiring cables have to be proportionate in base to the current and the length of the cable.
On the section “Function Diagram” and enclosure side a block diagram identifies all connections.
Identify the function and location of each connection terminal using the wiring diagram on the corresponding section, as an example (n° 1 application):
Connect 115 Vac signal lines at input terminals “1” and “2” (input terminals “3” and “4” are provided for daisy chain connection to the next module).
For Load A and its service load:
- connect positive or AC load supply line to terminals “13” and “18”;
- connect SIL 3 Normally Energized (NE) Load between terminals “14” and “16”;
- connect Not SIL Service Load between terminal “17” and negative or AC load supply line;
- connect terminal “15” to negative or AC load supply line.
For Load B and its service load:
- connect positive or AC load supply line to terminals “19” and “24”;
- connect SIL 3 Normally Energized (NE) Load between terminals “23” and “21”;
- connect Not SIL Service Load between terminal “20” and negative or AC load supply line;
- connect terminal “22” to negative or AC load supply line.
Installation and wiring must be in accordance to the relevant national or international installation standards, make sure that conductors are well isolated from each other and
do not produce any unintentional connection.
Connect SPST relay contacts checking the load rating to be within the contact maximum rating (5 A 250 Vac 1250 VA, 5 A 250 Vdc 175 W (resistive load)).
To prevent relay contacts from damaging, connect an external protection (fuse or similar), chosen according to the relay breaking capacity diagram on data sheet.
The enclosure provides, according to EN60529, an IP20 minimum degree of mechanical protection (or similar to NEMA Standard 250 type 1) for indoor installation, outdoor installation
requires an additional enclosure with higher degree of protection (i.e. IP54 to IP65 or NEMA type 12-13) consistent with the effective operating environment of the specific installation.
Units must be protected against dirt, dust, extreme mechanical (e.g. vibration, impact and shock) and thermal stress, and casual contacts.
If enclosure needs to be cleaned use only a cloth lightly moistened by a mixture of detergent in water.
Any penetration of cleaning liquid must be avoided to prevent damage to the unit. Any unauthorized card modification must be avoided.
Relay output contact must be connected to load non exceeding category II overvoltage limits.
Warning: de-energize main power source (turn off power supply voltage) and disconnect plug-in terminal blocks before opening the enclosure to avoid electrical shock
when connected to live hazardous potential.
Start-up
Before powering the inputs of unit check that all wires are properly connected. Check conductors for exposed wires that could touch each other causing dangerous unwanted shorts.
Enabling input, the “RELAY STATUS” yellow led must be lit, all relays must be energized, so that: contacts of terminals “13”-”14” (Out S_1), “15”-”16” (Out S_2), “21”-”22” (Out S_4) and
“23”-”24” (Out S_3) must be closed, while contacts of terminals “17”-”18” (Out P_1) and “19”-”20” (Out P_2) must be open.
Instead, disabling input, the “RELAY STATUS” yellow led must be turned off, all relays must be de-energized, so that: contacts of terminals “13”-”14” (Out S_1),
“15”-”16” (Out S_2), “21”-”22” (Out S_4) and “23”-”24” (Out S_3) must be open, while contacts of terminals “17”-”18” (Out P_1) and “19”-”20” (Out P_2) must be closed.
D5290S-079 is an electrical apparatus installed into standard EN50022 T35 DIN-Rail located in Safe Area / Non Hazardous Location within the specified operating temperature limits
Tamb - 40 to +60 °C. D5290S-079 must be installed, operated and maintained only by qualified personnel, in accordance to the relevant national/international installation standards,
following the established installation rules.
Warning: de-energize main power source (turn off power supply voltage) and disconnect plug-in terminal blocks before opening the enclosure to avoid electrical shock
when connected to live hazardous potential
.
Failure to properly installation or use of the equipment may risk to damage the unit or severe personal injury.
The unit cannot be repaired by the end user and must be returned to the manufacturer or his authorized representative.
Any unauthorized modification must be avoided.
The proof test shall be performed to reveal dangerous faults which are undetected by diagnostic. This means that it is necessary to specify how dangerous undetected faults, which
have been noted during the FMEDA, can be detected during proof test. The Proof test consists of the following steps:
Testing procedure at T-proof
Steps
Action
1
Bypass the safety-related PLC or take other appropriate action to avoid a false trip when removing the unit for test.
2
Verify the input-to-output functionality (for a min to max input voltage change 95 to 130 Vac), considering the input signal and each relay output contact state:
□
Out S_1 (NO contact) at terminals “13”-“14”: when input is energized, Out S_1 must be closed;
while shutdown of the input channel, Out S_1 must be open;
□
Out S_2 (NO contact) at terminals “15”-“16”: when input is energized, Out S_2 must be closed;
while shutdown of the input channel, Out S_2 must be open;
□
Out P_1 (2 NC contacts in parallel connection) at terminals “17”-“18”: when input is energized, Out P_1 must be open;
while shutdown of the input channel, Out P_1 must be closed;
□
Out S_3 (NO contact) at terminals “23”-“24”: when input is energized, Out S_3 must be closed;
while shutdown of the input channel, Out S_3 must be open;
□
Out S_4 (NO contact) at terminals “21”-“22”: when input is energized, Out S_4 must be closed;
while shutdown of the input channel, Out S_4 must be open;
□
Out P_2 (2 NC contacts in parallel connection) at terminals “19”-“20”: when input is energized, Out P_2 must be open;
while shutdown of the input channel, Out P_2 must be closed.
3
Remove the bypass from the safety-related PLC or restore normal operation inserting the unit.
This test detects almost 100 % of all possible Dangerous Undetected failures in the relay module.