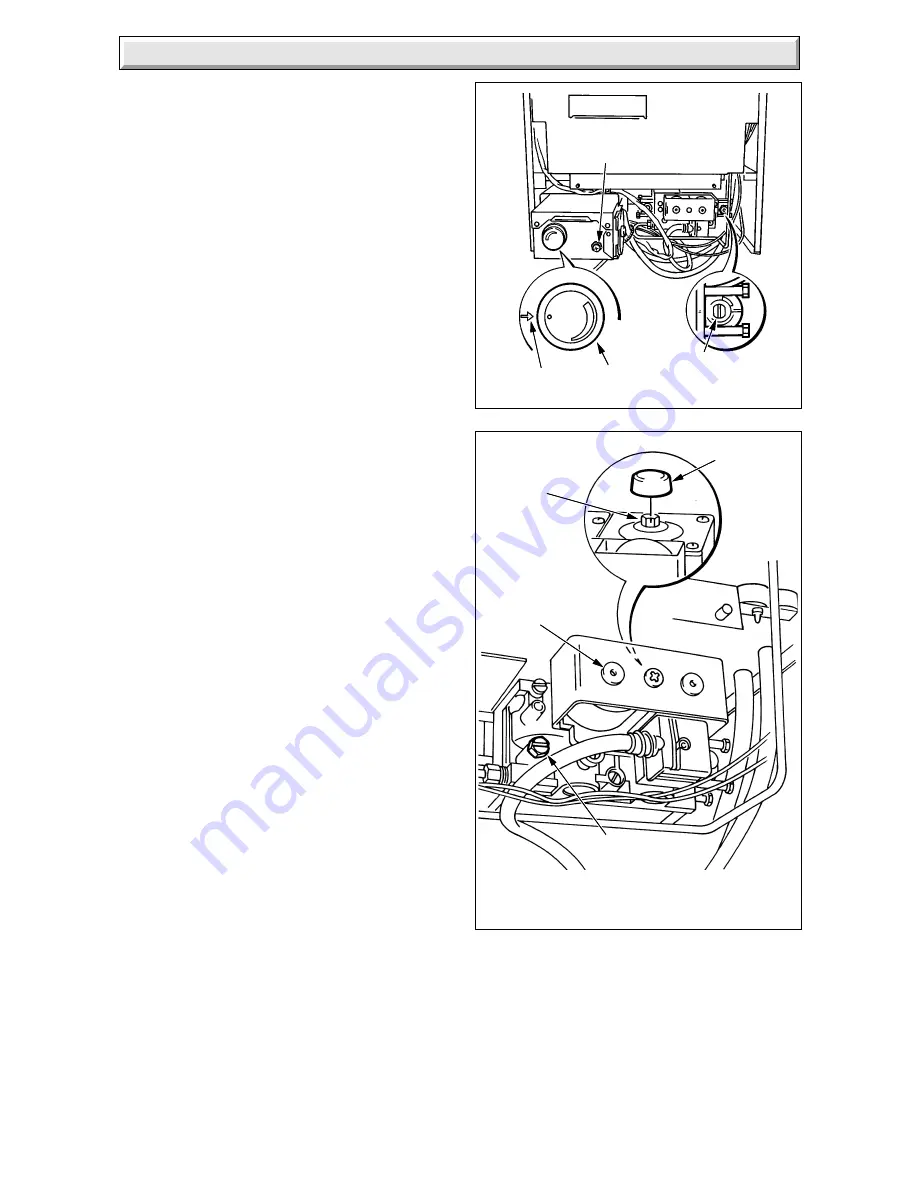
22
220683B
6 C o m m i s s i o n i n g
6.1 All Systems
Commissioning should be carried out by a competent
person in accordance with the current issue of BS6798.
Make sure that the system has been thoroughly flushed
out with cold water without the pump in place.
Refit the pump, fill the system with water, making sure
that all air is properly vented from the system and pump.
Before operating the boiler check that all external
controls are calling for heat.
6.2 Sealed Water Systems Only
Flush the whole of the system with cold water without
the pump in place. Refit the pump and fill until the
pressure gauge registers 2.7bar (40lbf/in
2
). Clear any air
locks and check for water soundness.
Check the operation of the safety valve, by allowing the
water pressure to rise until the valve opens. The valve
should open /-0.3bar (+/-4.3lbf/in
2
) of the preset
pressure. Where this is not possible conduct a manual
check and test.
Release cold water to initial system design pressure.
The set pointer on the pressure gauge should be set to
coincide with the indicating pointer.
6.3 Initial Lighting and Testing
CAUTION. This work must be carried out by a
competent person, in accordance with the current issue
of BS6798.
Make sure that all naked lights and cigarettes are out.
Identify the controls by reference to diagram 6.1.
Check that the boiler is isolated from the electrical
supply.
Makes sure that the control thermostat is turned to “O”
the “Off” position.
Turn the gas service cock “On”, see diagram 6.1.
Test the pilot supply tube and its connections for gas
soundness as follows:
Disconnect the ignition lead from the PCB, see
diagram 5.9.
Diagram 6.1
Diagram 6.2
NOTE:
DO NOT ADJUST ANY
OTHER SETTING SCREWS
MAIN BURNER
PRESSURE TEST
SCREW
MULTI-
FUNCTIONAL
CONTROL
OVERHEAT
SAFETY
CUT OFF
GAS SERVICE COCK
(SHOWN OFF)
SETTING
POINT
CONTROL
THERMOSTAT
KNOB
PLASTIC
COVER
4085
4108
GAS
PRESSURE
ADJUSTMENT
SCREW