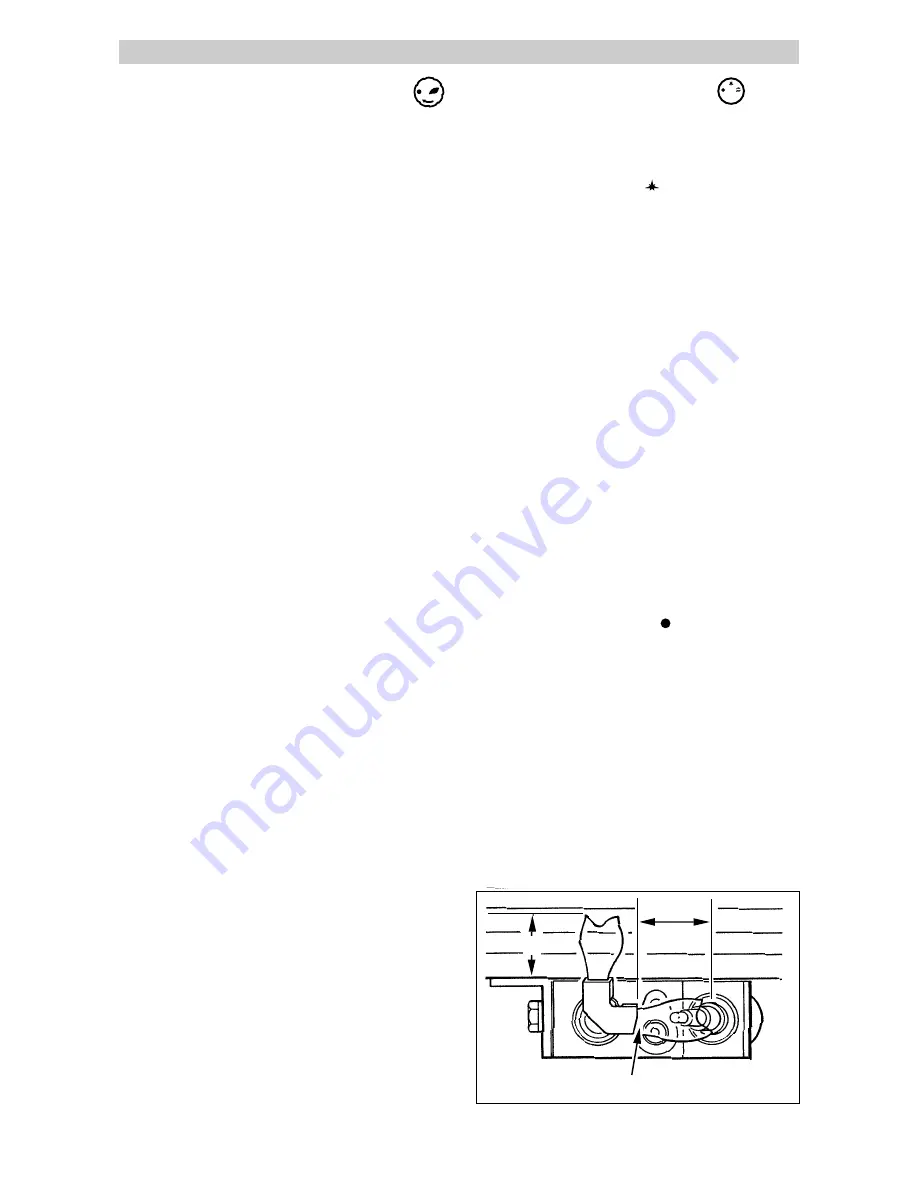
23
221129A
1 1 C o m m i s s i o n i n g
Diagram 11.4
12 to 14mm
12 to 14mm
SPARK GAP 3 TO 4 mm
2273
11.4 Initial Lighting of Pilot - Honeywell
Identify the boiler controls, see diagram 11.1.
Check that the boiler is isolated from the electrical
supply at the external isolator.
Fully depress and hold in gas control knob “D”. Press
and release piezo button “E” until the pilot burner lights,
(at this stage, air may be present in the gas components
of the boiler, therefore this operation may need to be
repeated). When the pilot flame has lit and is stable,
keep knob “D” fully depressed for 15 seconds, then
release. The pilot burner should then stay alight.
If the pilot flame goes out now or at any time, a safety
device prevents immediate relighting. Wait four minutes
before attempting to relight.
If the pilot burner goes out on releasing knob “D”, repeat
the above lighting sequence but this time keep knob “D”
depressed for a little longer.
The pilot flame size is preset and should envelop the
thermocouple, the approximate flame size is shown in
diagram 11.4. If the flame size is incorrect refer to the
adjusting instructions in “Pilot Burner” in “Replacement
of Parts” section of the Servicing Instructions.
Check for gas soundness of the pilot supply using leak
detection fluid. Take care not to splash any of the
electrical components.
Test the operation of the thermocouple flame failure
system to ensure the boiler shuts down within 60
seconds, indicated by a “click” from the gas valve.
If the pilot burner will not stay alight, refer to
“Thermocouple and Overheat Cutoff” in “Fault Finding”
section of the Servicing Instructions.
Fit the cover of the inner case, making sure that it is
fitted and seals correctly, using the four screws
previously removed, see diagram 6.2.
Make sure that all hot water draw off taps are closed then
set switch “C” to “Off” as shown in diagram 11.1.
With the boiler isolated from the electrical supply the
pilot flame may go out. If this should happen, wait four
minutes then relight the pilot burner following the above
lighting instructions but with the electrical
supply connected.
11.4 Initial Lighting of Pilot - SIT
Identify the boiler controls, see diagram 11.1.
Check that the boiler is isolated from the electrical
supply at the external isolator.
Turn gas control knob “D” to
pilot/ignition position
and depress. Press and release piezo button “E” until the
pilot burner lights, at this stage air may be present in the
gas components, so the operation may need repeating.
When the pilot flame has lit and is stable, keep knob “D”
fully depressed for about 15 seconds and then release.
The pilot burner should stay alight.
If the pilot flame goes out now or at any time, a safety
device prevents immediate relighting. Wait four minutes
before attempting to relight.
If the pilot goes out on releasing knob “D” repeat the
lighting instructions but now keep knob “D” depressed
for a little longer after the pilot has lit.
If the pilot burner will not stay alight, refer to
“Thermocouple and Overheat Cutoff” in Fault Finding
section of the Servicing Instructions.
The pilot flame size is factory preset and should envelop
the thermocouple to about the size given in diagram
11.4. If the flame size is incorrect, refer to “Pilot
Burner” in Servicing Instructions.
Check for soundness of the pilot supply using a suitable
leak detection fluid.
Test the operation of the flame supervision system by
turning knob “D” clockwise to “
” position to make
sure that it shuts down within 60 seconds, indicated by a
click from the valve.
Fit the cover of the inner case, making sure that it is
fitted and seals correctly, using the four screws
previously removed, see diagram 6.2.
Make sure that all hot water draw off taps are closed then
set switch “C” to “Off” as shown in diagram 11.1.
With the boiler isolated from the electrical supply the
pilot flame may go out. If this should happen, wait four
minutes then relight the pilot burner following the above
instructions but with the electrical supply connected.